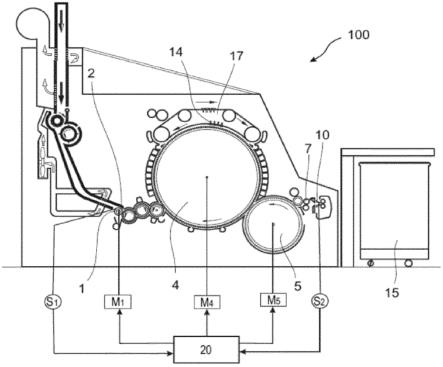
1.本发明涉及根据权利要求1和10的前序部分所述的生产纤维条的方法和梳理机。
背景技术:2.在梳理机上制造纤维条时很高的生产速度下,每次条筒更换时必须停止生产,这对用于随后进一步处理的纤维条的质量产生负面影响。在加速或减速阶段中的梳理机生产期间应使条子重量符合其额定值。在具有降低的纤维条生产量的条筒更换即将到来时,改变梳理机的喂入罗拉的转速,随后随时间延迟而降低道夫的转速或圆周速度。此外,在喂入罗拉转速的降低与道夫转速的降低之间的时间延迟通过纤维质量(材料、纤维尺寸等)和梳理机的锡林占用率来确定。但是因为所述时间延迟对于条子重量的变化非常重要,这会导致纤维条中的薄段或厚段进而影响与额定值的偏差,所以这种时间延迟借助经验值存储在梳理机的控制装置中。在梳理机加速运行的情况下在进行条筒更换之后同样必须再次考虑这种时间延迟。
3.ep 0799915b2描述了在梳理机上在条筒更换时的减速和加速阶段的条子调节。该文献声称使用一种利用在一段时间间隔内由制动/加速斜坡得出的积分部分的调节算法,但没有公开这些值如何影响时间延迟的细节。
技术实现要素:4.从现有技术出发,本发明的任务在于,这样优化在喂入罗拉转速的降低或提高与道夫转速的降低或提高之间的时间延迟,以便可以在条筒更换期间生产尽可能均匀的梳理机条子。
5.本发明通过具有权利要求1中给出的特征的方法和根据权利要求10所述的梳理机来解决所述任务。本发明的有利的扩展方案在从属权利要求中限定。
6.本发明涉及一种用于控制具有至少一个喂入罗拉和道夫的的梳理机,所述喂入罗拉和道夫分别具有单独可控的驱动器,其中,梳理机构造用于由纤维束或棉样品制造纤维条,纤维条能堆置在条筒中,其中,为了条筒更换而改变喂入罗拉的圆周速度并且在一时间延迟(
△
ts;
△
te)之后改变道夫的圆周速度。为此,梳理机具有传感器,其构造用于确定生产的纤维条的重量或生产的纤维条的重量变化。在此,梳理机的控制装置在每次条筒更换时由传感器的信号确定纤维条的重量变化的标准差并且为标准差分配平均值。在此,控制装置构造用于借助至少两个平均值优化喂入罗拉的速度变化与道夫的速度变化之间的时间延迟。
7.利用按照本发明的方法,梳理机可以自我优化喂入罗拉与道夫的圆周速度的降低之间的时间延迟,而不依赖于纤维质量和运行条件。除了任意起始值之外,不需要在控制装置中存储纤维相关的数据。在更换批次或新的纤维混合物时,控制装置自动地确定优化的时间延迟,借助优化的时间延迟在条筒更换期间优化条子纤度或者与额定值的重量偏差。纤维条获得更均匀的质量,由此改善随后在牵伸装置和/或气流纺纱机中的处理。
8.通过在条筒更换之前降低喂入罗拉的圆周速度并且随一时间延迟降低道夫的圆周速度,可以降低在条筒更换开始时条子纤度的增加或减少或者纤维条的重量与额定值相比的增加或减少。
9.通过在条筒更换结束时提高喂入罗拉的圆周速度并且随一时间延迟提高道夫的圆周速度,可以降低在条筒更换时条子纤度的减少或增加或者纤维条重量与额定值相比的减少或增加。
10.喂入罗拉与道夫的圆周速度的变化优选可以利用相同的或不同的加速或减速来进行。在锡林占用率低时,在喂入板和出条装置处的传感器之间的调节路径减小,从而喂入罗拉和道夫的圆周速度以相同的加速或减速变化。在锡林占用率高时设定大的调节路径,从而在条筒更换期间降低纤维供应的时间内,将占用锡林的纤维进一步转交给道夫。在此,在条筒更换结束时将道夫以更高的加速度运行至额定速度并且因此运行至圆周速度的额定值是有意义的。
11.在条筒更换开始时的时间延迟优选可以与条筒更换结束的时间延迟相同或不同。在此,在喂入板和出条装置处的传感器之间的调节路径中,也要考虑锡林占用率的大小。在锡林占用率高时,条筒更换开始时的时间延迟与条筒更换结束时的时间延迟可以是不同的。在锡林占用率低时,调节路径变短并且喂入罗拉和道夫的速度变化之间的协调必须更精确,因为梳理机中用于补偿波动的纤维重量更少。
12.在一种优选的实施方式中,控制装置构造用于由多个平均值(至少两个平均值)插值计算出最小值,该最小值形成喂入罗拉和道夫的速度变化之间的最佳时间延迟。随着时间延迟的优化,在条筒更换期间能够将纤维条(条子纤度)相对于额定值的重量变化减少到最小值。为此,对于控制装置来说,两个平均值已经足够开始时间延迟的优化了。在至少三个平均值的情况下,控制装置构造用于通过这些平均值插值计算出一条曲线,该曲线的最小值可以是优化的时间延迟。
13.在第一次条筒更换开始时,优选通过至少一个可存储在控制装置中的值预先给定时间延迟。这个值可以是根据经验预先给定的并且取决于梳理机结构、使用的针布、纤维质量和生产条件。此外,锡林占用率和调节路径的一部分也与这些因素有关。
14.在一种优选的实施方式中,梳理机的控制装置构造成单独地操控梳理机的所有驱动器并且至少处理喂入槽的传感器处所确定的纤维重量与传感器处所确定的纤维条重量并且调节相关的驱动器。在控制装置中优选可以存储:喂入罗拉和道夫的速度变化之间的时间延迟的优化仅在各辊的速度差例如至少为80m/min时和/或仅在条筒更换时条子的供应速度与正常的供应速度的比例为至少80%时才开始。阈值本身(从该阈值起应使用所述方法)可以根据梳理机结构、使用的针布、纤维质量或生产条件变化并且应防止过度调节纤维条的质量,因为例如梳理间隙调节或其他因素也会影响条筒更换时的条子纤度或纤维条的重量变化。
15.按照本发明的梳理机具有至少一个喂入罗拉和道夫,所述喂入罗拉和道夫分别具有单独可控的驱动器,梳理机还具有构造用于确定喂入梳理机中的纤维或棉的重量的传感器、构造用于确定生产的纤维条的重量或生产的纤维条的重量变化的传感器、构造用于执行运行根据上述权利要求之一所述的梳理机的方法的控制装置。
附图说明
16.以下与本发明的优选的实施例的说明一起借助于附图更详细地阐述改善本发明的其它措施。
17.图中:
18.图1示出带有按照本发明的装置的梳理机的示意性的侧视图;
19.图2示出带有与本发明相关的驱动器和传感器的梳理机的示意性视图;
20.图3示出关于条筒更换时的时间延迟与喂入罗拉和道夫的相关联的速度的分布图;
21.图4示出关于条筒更换期间的纤维条的重量变化的分布图;
22.图5示出关于条筒更换期间的绝对重量变化的示意性的测量图;
23.图6示出用于呈现确定的平均值与喂入罗拉和道夫之间的相关联的时间延迟的分布图。
具体实施方式
24.下面参照图1至图6阐述按照本发明的装置和方法的优选实施方式,所述装置和方法计划在用于棉、化学纤维等的梳理机上使用。图中相同的特征均设有相同的附图标记。对此要理解,附图仅简化地示出,尤其没有按比例示出。
25.图1示出根据现有技术的梳理机100,在所述梳理机中将纤维束经过甬道导向至喂入罗拉1、喂入板2,经由一个或多个刺辊3a、3b、3c导向至锡林4或滚筒。在锡林4上,借助固定的梳理元件20、抽吸罩和斩刀并且借助布置在回转盖板系统17上的环绕的梳理元件14使得所述纤维束的纤维平行并且得到清洁。随后,通过道夫5、剥取罗拉6和多个挤压辊7、8将产生的纤维薄网运送到纤维网引导元件9,其借助集合喇叭口10将所述纤维薄网变为纤维条,所述纤维条通过分离罗拉11、12被传递至后续的加工设备或条筒15。梳理元件14相对于锡林4(梳理间隙)的调节通过未示出的、具有彼此楔形定向的元件的滑动板条进行。
26.图2中仅示出对本发明来说重要的驱动器和传感器,它们仅为所有存在的驱动器和传感器的一部分。喂入罗拉1由驱动器m1驱动。在喂入罗拉1的区域中,传感器s1布置在未详细示出的喂入槽处,利用该传感器检测进入的棉样品的量或重量。传感器s1例如可以构造为电容式或电感式传感器,其检测敏感元件(f
ü
hler)的偏移进而间接确定棉样品的重量流量。喂入罗拉1由驱动器m1以直至40u/min的转速驱动。驱动器m4驱动锡林4,其在条筒更换的加速或减速阶段内以例如1500u/min的恒定转速被驱动。道夫5由驱动器m5以例如300u/min驱动。在道夫5下游,纤维薄网借助未示出的横向带和集合喇叭口10变形为纤维条,其中,在集合喇叭口10处或者在其下游布置另一个传感器s2,利用该传感器能直接或间接地或确定纤维条的重量或与额定值的偏差。传感器s2同样可以构造为电容式或电感式的传感器,其借助敏感元件的偏移或两个彼此协调的圆盘之间的偏移来确定纤维条的重量流量或重量流量的变化。所有示出的驱动器m1、m4、m5构造为伺服电机或变频驱动器,它们由控制装置20操控和调节。所述传感器s1、s2的数据同样进入控制装置20,随后在那里被评价。由传感器s2的所确定的重量流量,控制装置20计算出条筒填充时间和条筒更换的时间点tk。利用条筒更换之前的准备时间降低喂入罗拉1的转速,道夫5的转速或圆周速度以时间上的延迟
△
ts随之降低。
27.该系统中的调节路径由梳理机100中的纤维的运行时间确定,即,从喂入罗拉1的转速变化到传感器s2处的变化的纤维重量的检测。由于锡林占用量,纤维在转移到道夫5上之前可以多次绕锡林4运输,所以调节路径可以大于相应的锡林周面上的直接运输路径。
28.随着每次条筒更换,降低道夫5的供应速度。因为锡林4以恒定的转速继续运行,所以圈条器处的纤维条的重量增加,这导致不期望的厚段。如果进行条筒更换,就提高道夫5的转速,由此,每单位时间供应的纤维重量降低,因为锡林4以恒定的转速继续运行。为此,控制装置20设定在条筒更换之前降低喂入罗拉1的转速或圆周速度,以便将较少的纤维重量输送给梳理机。在条筒更换和纤维条的供应速度降低的同时,降低道夫5的转速,这首先导致纤维条中的重量的增加。喂入罗拉1的转速的降低与道夫5的转速的降低之间的时间延迟通过在该时间点确定的条子重量来确定。由条筒更换期间的条子重量的信号确定对于条子重量的额定值的标准差ss2。由该标准差ss2得出平均值ms2。在每次条筒更换时,所述过程从具有例如0.7s的时间延迟
△
ts的起始值出发,以时间延迟
△
ts的减少的或提高的值一直重复,直至每次条筒更换都确定新的平均值ms2。由平均值ms2可以插值计算出一条曲线,由其最小值确定关于确定开始降低喂入罗拉1的转速和开始降低道夫5的转速之间的时间延迟
△
ts的最佳时间。两个平均值ms2足以使控制装置提高或减少时间延迟
△
ts。将条子重量与额定值的偏差最小时的值用作最佳时间延迟。对于每种纤维质量来说,标准差ss2和由此确定的平均值ms2可能是不同的。因此,本发明的优点在于,除了第一起始值之外不需要采集经验数据。用于条筒更换的开始的时间延迟
△
ts的第一起始值例如可以是0.7秒并且在一方面取决于调节路径和锡林占用量。根据梳理机结构和要处理的纤维质量,用于时间延迟的起始值也可以仅为0.4秒。梳理机100自动优化喂入罗拉1与道夫5的转速降低之间的时间延迟,从而客户可以在纤维质量不同且运行条件(生产量、环境温度、纤维湿度)不同的情况下操作梳理机100。用于条筒更换的开始的时间延迟
△
ts例如可以减少到0.55秒,由此将纤维条中的重量缺陷降至最低。
29.图3示出了在横坐标上以秒为单位绘制时间t的分布图。在纵坐标上以m/min为单位示出速度v,喂入罗拉1和道夫5的以u/min为单位的相关转速n被分配给所述速度。实线曲线示出喂入罗拉1的速度曲线,喂入罗拉的速度或转速随条筒更换的时间点tk之前的准备而降低。时间点tk是条筒更换的开始,并且因此同时也是喂入罗拉1的速度降低的时间点。如果要填充到当前条筒内的纤维条的剩余量(以米为单位)低于阈值,则开始条筒更换。为此,降低喂入罗拉1的速度或转速。随着相对于降低喂入罗拉1的速度的时间差
△
ts,降低道夫5的速度(虚线)。如果两个辊1、5达到各自的条筒更换速度或相关转速,则在与圈条盘同步之后进行实际的条筒更换。在条筒更换结束之前,喂入罗拉1的转速或圆周速度以准备时间在此又升高,随后道夫5的转速或圆周速度以时间延迟
△
te上升。在该图示中,喂入罗拉1和道夫5在纵坐标上的转速n和速度v成比例。由于在梳理机100内部在各个辊之间的过渡位置处的滞后以及纤维到纤维薄网的精细开松,道夫5以高于喂入罗拉1的圆周速度运行。在这种情况下假定喂入罗拉1和道夫5的圆周速度相同地加速或减速。
30.图4同样在横坐标上示出时间t并且在在纵坐标上示出纤维条相对于额定值(以0绘制)的重量变化
△
m。与道夫5随着时间点tk时的条筒更换的速度降低相对应,纤维条的重量增加并且再次下降,直到被拉平至额定值。随着道夫5的速度的提高,纤维条的重量首先下降至低于额定值,直到被再次拉平。图4示出了喂入罗拉1与道夫的速度差之间的时间延
迟
△
ts、
△
te太小或没有时的条子曲线。如果时间延迟
△
ts、
△
te过大,则信号行为发生变化并且在纤维条中首先产生薄段然后产生厚段。测量曲线上的箭头表示喂入罗拉1的速度降低与道夫5的速度降低之间的时间延迟
△
ts、
△
te的优化方向。随着每次条筒更换,图4中示出的与额定值的偏差可以变小。
31.图5再次在横坐标上示出时间t,并且在左边的纵坐标上示出喂入罗拉1和道夫5的以m/min为单位的速度v。这些辊的以u/min为单位的转速与它们的速度成比例。喂入罗拉1的曲线再次以实线表示,并且道夫5的曲线以虚线表示。在右边的纵坐标上给出在出条装置的传感器s2处的以ktex为单位的纤维条的绝对重量ms2。在分布图上几乎看不出纤维条的重量随道夫速度降低而提高。控制装置20由分布图中可看出的波动的条子重量ms2计算出条子重量的标准差ss2并且由此得出平均值ms2。随着每次条筒更换,确定新的标准差ss2与新的平均值ms2,其中,控制装置存储平均值ms2并且借助存储的平均值ms2由三个平均值ms2插值计算出一条曲线,对于这些运行条件(梳理机的生产率、纤维质量)来说,该曲线的最小值是在开始和结束条筒更换时在喂入罗拉1和道夫5的速度降低方面优化的时间延迟。两个平均值ms2就足以使控制装置识别在喂入罗拉1和道夫5的速度降低之间的时间延迟的方向。因为这是一个进行中的过程,所以在第二次条筒更换期间就已经进行时间延迟
△
ts和
△
te的优化,因为控制装置由两个存储的平均值ms2已经可以导出使条子重量与额定值偏差尽可能小的第一次优化。有利地,在第一次条筒更换时时间延迟
△
ts和
△
te可以是不同的,从而控制装置可以由纤维条的重量与额定值的偏差优化时间延迟。因此,在第一次条筒更换时,可以由条筒更换的开始和结束时的时间延迟
△
ts和
△
te形成两个平均值ms2,从而第二次条筒更换已经具有优化的时间延迟并且条子重量与额定值的偏差已经改善。
32.在图6的实施例中,在横坐标上示出了进行多次条筒更换的时间延迟
△
t。在纵坐标上以百分比形式示出标准差ss2的平均值ms2。在分布图中针对每次条筒更换,在相关联的时间延迟
△
ts/
△
te时示出新的平均值ms2-1至ms2-n。通过插值出一条曲线得出在第六个平均值ms2-6之前不久的最小值,与其相关的时间延迟作为例如0.58s的
△
ts和
△
te被用于下一次的条筒更换。在平均值过于分散时或在处理新批次的纤维时,进行全新的测量,而不考虑已经存储的值。如关于图5的实施例所说明的那样,随着每次条筒更换,可以针对条筒更换的开始由时间延迟
△
ts以及针对条筒更换的结束由时间延迟
△
te形成两个平均值ms2连同与额定值的相关联的偏差,从而已经以优化的时间延迟进行第二次条筒更换。
33.在梳理机100的控制装置20中可以存储进一步的边界条件,即,时间延迟
△
ts和
△
te的优化例如仅在各辊之间的速度差至少为80m/min时和/或仅在条筒更换时条子的供应速度与正常的供应速度比例为至少80%时才进行干预。
34.附图标记列表
35.100梳理机
36.1喂入罗拉
37.2喂入板
38.3a,3b,3c刺辊
39.4锡林
40.5道夫
41.6剥取罗拉
42.7,8挤压辊
43.9纤维网引导元件
44.10集合喇叭口
45.11,12分离罗拉
46.14梳理元件
47.15条筒
48.17回转盖板
49.20控制装置
50.m1喂入罗拉的驱动器
51.m4锡林的驱动器
52.m5道夫的驱动器
53.s1喂入槽的传感器
54.s2出条装置的传感器
55.v辊的速度
56.u辊的转速
57.t时间
58.tk条筒更换的时间点
59.△
ts条筒更换开始时的时间延迟
60.△
te条筒更换结束时的时间延迟
61.ms2出条装置的传感器处的平均值
62.△
m纤维条的重量变化
63.ms2出条装置的传感器处的条子重量
64.ss2出条装置的传感器处的标准差