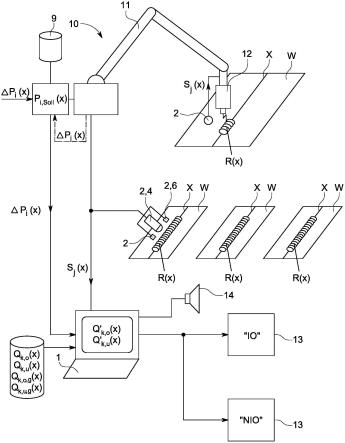
1.本发明涉及一种用于评估加工操作的质量的方法,其中沿着加工轨迹以特定加工参数加工工件,沿着所述加工轨迹用至少一个传感器测量所述加工操作的加工结果并且记录至少一个传感器信号,并且从至少一个传感器信号确定至少一个质量参数,并且将所述至少一个质量参数与质量参数阈值进行比较以用于评估沿着所述加工轨迹的所述加工操作的加工结果的质量。
2.此外,本发明涉及一种用于评估沿着加工轨迹以特定加工参数进行的工件的加工操作的质量的装置。
背景技术:3.加工操作特别包括接合过程,例如焊接或钎焊过程,其中工件接合在一起或者工件被涂层,但是也包括表面处理过程,例如等离子体加工操作,其中工件用等离子体加工以便使它们为后续加工操作做好准备。例如,工件的表面可以在涂漆之前用等离子体处理,以便从表面去除残留物和/或改善漆层的粘附性。
4.众所周知的是,监测或评估加工操作的质量以便能够剔除有缺陷的工件或相应地调整加工参数以便改善质量。为此目的,在加工操作之后评价加工轨迹并且从其评估加工操作的质量。在最简单的情况下,质量评估可以由专业人员以视觉评估的形式进行。然而,典型地,用相应的传感器自动测量沿着加工轨迹的加工操作的加工结果并且从传感器信号确定至少一个质量参数。为了评估质量,将至少一个质量参数与质量参数阈值进行比较。例如,作为焊接过程的加工轨迹的焊缝可以在焊接过程之后用相机优选地利用照明进行测量,并且由此用相应的图像处理算法确定焊缝的焊缝宽度和焊缝高度,并且由此推导出质量参数。根据加工任务或焊接任务,可以使用不同的质量参数来限定焊缝的质量。例如,在可见焊缝的情况下,除了焊缝的机械特性之外,焊缝尽可能窄且规则可能也是重要的,而在不可见焊缝的情况下,连接的强度和因此足够的焊透深度可能更重要。适合于相应的加工操作的至少一个质量参数相应地被限定并且然后与特定的质量参数阈值(例如上阈值和下阈值)进行比较,以便能够自动地评估质量。通常通过评估以io(
″
有序
″
)加工轨迹最佳加工的工件来确定质量参数。在焊接过程中,例如,可以将焊接咬边的大小、所谓的a尺寸、焊缝高度、焊缝端部处的端部弧坑等用作质量参数。
5.ep 3 566 806 a1描述了一种作为加工操作的焊接过程,其中为了实现特定的质量标准,将基于测试工件上的测试焊接确定的最佳焊接参数自动用于焊接过程。用于相应焊接任务的最佳焊接参数的确定通过由测试焊接的相应最佳焊接参数计算的质量函数的最佳值来进行。
6.ep 1 642 366 b1和wo 00/35622 a1描述了用于监测焊接过程的质量的方法,其中将关于所产生的焊缝的信息与预定值进行比较,并且在偏差的情况下相应地调整焊接参数,或者在大偏差的情况下发出警告。在该情况下,将加工参数调节到预定的目标值。
7.在de 10 2019 200 482 a1中描述了一种加工操作,其中以预定的加工参数来加
工工件,并且在加工结果有偏差的情况下相应地调整加工参数,以便始终实现尽可能保持不变的加工结果。
8.从us 2009/0173726a1已知一种焊接系统,其具有对焊接过程的监测,目的是保持不变的条件和保持不变的加工结果质量。在加工工件期间使质量评估与加工参数的有意进行的改变适配未被讨论并且甚至是不期望的。
9.在加工操作、特别是焊接过程的已知质量评估系统中,检查特定的标准是否处于预定界限内。例如,将所产生的焊缝与先前限定的
″
理想焊缝
″
进行比较并且由此评估所产生的焊缝的质量。然而,如果在加工操作期间有意地手动或自动改变加工参数,则在质量评估期间不进行质量标准的自动调整,而是必须手动地执行,这是耗时的。这会导致将加工操作的质量评估为不充分,原因是在加工操作期间加工参数的有意进行的改变未被自动地考虑。也可以正面地评估加工操作的质量,但是结果不符合质量标准。例如,在焊接过程中,由于工件公差,可能需要调整特定的焊接参数。例如,由于工件或夹紧装置的公差出现的较大间隙宽度会需要调整焊丝进给和其他焊接参数。如果没有自动通知质量评估系统关于焊接参数的目标值的改变,则可能导致焊接质量的错误评估。
技术实现要素:10.本发明的目的是提供一种上述的用于评估加工操作的质量的方法和装置,通过所述方法和装置不会出现在加工操作期间加工参数的有意进行的改变方面的所述缺点,并且能够实现关于加工操作和被加工工件的质量的可再现的说明。自动质量评估系统也应当能够在有意地手动或自动进行加工参数的改变的情况下使用并且能够作出关于加工操作或被加工工件的质量的可靠说明。
11.根据本发明的目的在方法方面通过以下方式实现,即,在加工操作的质量评估中,在沿着加工轨迹加工工件期间自动地考虑加工参数从目标值的进行的改变,其方式是,代替质量参数阈值,确定与加工参数的改变适配的质量参数阈值,并且将至少一个质量参数与适配的质量参数阈值进行比较以用于评估沿着加工轨迹的加工操作的加工结果的质量。因此根据本发明的方法提供在加工操作期间传送到质量评估系统的加工参数的实际值,由此在评估加工操作的质量时通过使质量参数阈值相应地适配加工参数的改变自动地考虑加工参数的目标值的有意进行的改变。结果,可以更可靠地评估被加工工件的质量,并且例如,可以防止评估为质量差的工件或评估为品质不良的工件的不合理废弃,尽管它们不符合质量标准。重要的是,仅考虑加工参数的有意的或故意的改变,而不考虑由干扰引起的改变。由于自适应的加工操作,加工参数的目标值的手动进行的改变或加工参数的目标值的自动进行的改变被视为有意改变。加工参数的目标值可以是整体参数,例如待设定的平均焊接电流或平均焊丝进给,即使这些加工参数在加工期间偏离这些设定值。加工参数从目标值的有意进行的改变可以标准地或仅在出现的情况下传送到进行质量评估的位置。通过考虑加工参数从目标值的改变并且使质量参数阈值适配加工参数的改变,可以提高质量评估的可靠性。改变的加工参数对质量参数的影响可以根据加工的类型而明显不同。加工参数的改变和用于评价加工操作或加工结果的质量的质量参数的改变之间的关系可以基于测试加工操作来确定并且存储在表或函数关系中。由于在质量评估期间的自动考虑,可能的是,即使在加工参数由于工件的一般公差而改变的情况下也可以使用质量评估系统并且
提供可靠的结果。
12.可以在沿着加工轨迹加工工件期间通过比较传送的加工参数的实际值和传送的加工参数的目标值从目标值确定加工参数的进行的改变。在该情况下,目标值表示在进行改变之前的值,实际值是在进行改变之后的值。在这种所谓的
″
在线方法
″
中,加工参数的改变几乎实时地被确定和传输,使得可以随时利用实际数据进行沿着加工轨迹的加工操作的质量监测。加工参数的改变还包括例如在更换加工装置的磨损部件时可能出现的系统相关的改变。例如,在更换焊炬的接触管之后,焊接电压将降低。如果在评估加工操作的质量时也考虑加工参数的这些有意的改变和质量参数阈值的相关改变,则获得关于加工操作或在加工操作期间加工的工件的质量的更可靠说明。
13.替代地或附加地,也可以在沿着加工轨迹加工工件期间记录加工参数从目标值和/或传送的加工参数的实际值和/或传送的加工参数的目标值的进行的改变,并且以后可以在沿着加工轨迹的加工操作的质量评估中用于自动考虑。在这种所谓的
″
离线方法
″
中,加工参数的改变和质量参数相关阈值被记录和存储以供以后使用,使得它们可以在执行加工操作的质量监测时被考虑。
14.根据本发明的另一特征,从用于特定加工参数的存储质量参数阈值确定与加工参数的改变适配的质量参数阈值。如果针对多数不同的加工状况和多数不同的加工参数存储评估加工结果可以借助的所得质量参数的阈值,则可以根据相应的实际加工参数从这些存储值确定质量参数阈值。上和下质量参数阈值可以限定为质量参数阈值,或者也可以限定具有特定最大质量参数波动范围的质量参数平均值。存储的质量参数阈值可以存储在与加工参数相同的存储器或相同的数据库中,或者存储在其他存储器或数据库中。
15.例如,可以从测试加工操作或加工测试,例如用于特定加工参数和特定故障的测试焊接过程或焊接测试确定存储的质量参数阈值。
16.优选地通过特定加工参数的存储质量参数阈值的内插来确定与加工参数的改变适配的质量参数阈值。通过这样的内插方法可以快速地并且在没有大的计算耗费的情况下确定用于多数不同的加工参数的相应质量参数阈值。
17.优选地,在从用于测量加工结果的至少一个传感器信号确定至少一个质量参数时,考虑至少一个加工参数的改变。例如,在将焊缝的焊缝宽度确定为焊接过程的质量参数时,可以考虑对焊缝宽度具有明显影响的焊丝的进给速度的改变。
18.在评估加工操作的质量时,可以考虑附加的环境参数,例如工件温度、环境温度、空气湿度等。通过包括也可以取决于加工轨迹的这样的环境参数,进一步改善了质量评估的结果。
19.可以借助于工件非破坏性测量方法、例如利用作为至少一个传感器的光学传感器、尤其是激光扫描器、相机等、x射线传感器和/或温度传感器来测量沿着加工轨迹的加工结果,并且可以记录至少一个传感器信号。借助于非破坏性测量方法和优选非接触式传感器记录加工结果具有的优点是可以特别快速地并且沿着整个加工轨迹进行加工结果的测量并且在该过程中不改变被加工工件。在特定影响因素的情况下可能有利的是紧接加工工件之后沿着加工轨迹进行加工结果的测量。例如,工件的材料中的温度分布可以紧接执行加工之后提供关于在加工轨迹内和周围的加工结果的材料结构的信息。使用特定的质量参数,也可能有利的是,仅在加工工件之后的某个时间沿着加工轨迹测量加工结果,原因是在
该时间之后才可以评估加工操作的质量。
20.替选地或附加地,也可以借助于破坏工件的工件破坏性测量方法、例如通过沿着加工轨迹在加工结果的各点处制造通过工件的切口并且尤其通过使用至少一个传感器拍摄切口的表面的图像来测量沿着加工轨迹的加工结果,并且可以记录至少一个传感器信号。例如,可以沿着加工轨迹以加工结果的特定间隔制造显微切片并且由此推导出特定的质量参数。自然更复杂的这样的测量方法也提供沿着加工轨迹的加工结果的内部结构的重要认识,其利用非接触式测量方法无法检测或者仅
″
不良地
″
检测。沿着加工轨迹的加工结果的记录显微切片又可以利用各种方法来分析,尤其是借助于相机和相关的图像处理方法。使用特定的化学品可以改善加工结果的显微切片的显微结构的识别。在加工操作之后对显微切片的宏观检查也可以提供特征性质量参数。显微切片被分析并且以特定传感器信号以及随后沿着加工轨迹的加工结果的特征性质量参数的形式被确定和存储。除了产生显微切片之外,也可想到在工件上进行拉伸测试、弯曲测试等。
21.根据本发明的另一特征,在工件的加工期间用至少一个传感器测量沿着加工轨迹的加工结果,加工轨迹的测量的速度优选地对应于加工速度。在该实施例变型中,加工操作的质量评估或工件的加工轨迹的测量紧接工件的加工之后或在工件的加工之后的相对较短的时间段内进行。在该情况下,有利的是质量评估系统与加工系统同步地相对于工件移动。例如,测量加工轨迹的相机可以安装在也承载加工工具的相同机器人臂上,并且可以在加工工件之后分析加工轨迹。在该情况下,沿着加工轨迹的加工结果的测量以与工件的加工相同的速度进行。当然,质量评估系统和加工系统也可以静止并且工件可以在加工期间移动,或者不仅质量评估系统和加工系统而且工件可以彼此相对移动。
22.也可以在完成工件的加工之后用至少一个传感器测量沿着加工轨迹的加工结果,沿着加工轨迹的加工结果的测量的速度优选大于加工操作的加工速度。如果沿着加工轨迹的加工结果的测量独立于工件的加工进行,则测量的速度也可以选择成比加工速度明显更高。例如,在加工工件之后沿着加工轨迹的加工结果的光学扫描可以比加工工件本身快得多地进行。此外,也可以用不同的传感器执行沿着加工轨迹的加工结果的若干次测量,并且然后从不同的传感器信号确定质量参数。此外,因此可以用单个测量站评估多个加工站的工件。
23.如果至少一个质量参数超过质量参数阈值或适配的质量参数阈值,则可以输出警告和/或可以存储超过。例如,警告可以声学地、光学地或者也可以以机械形式通过振动机构来进行。以该方式,可以相应地指出已超过质量参数。警告也可以通过相应的通信通道转发到更高级位置。
24.可以根据至少一个质量参数超过质量参数阈值或适配的质量参数阈值的程度来改变警告。例如,声学警告的音量或光学警告的发光强度或闪烁频率可以适配质量偏差的大小,并且通过警告通知人员质量偏差的大小。
25.在焊缝作为加工轨迹的情况下,优选地考虑焊接过程的加工参数:焊接电流、焊接电压、焊丝的输送速度、焊炬相对于工件的迎角、焊炬相对于工件的相对位置和/或焊接速度。这样的焊接过程也包括钎焊过程,其中与焊接相反,不进行工件的基本材料的熔化或进行工件的基本材料的较少的熔化。
26.类似地,根据本发明的目的通过用于评估加工操作的质量的上述装置来实现,所
述装置设置用于执行上述方法。关于由此可以实现的优点,参考以上方法的描述。用于质量评估的装置的特征在于与加工装置的相应连接,通过所述连接将加工期间加工参数的进行的改变传送给用于质量监测的装置,使得质量参数的阈值可以自动适配加工参数的改变。
附图说明
27.参考附图进一步解释本发明。在图中:
28.图1示出了示意性加工操作,其中沿着加工轨迹加工具有特定加工参数的工件;
29.图2a至2d示意性地示出了用沿着加工轨迹测量加工结果的各种传感器评估加工操作的质量的方法;
30.图3示出了根据本发明的用于评估工件上的加工操作的质量的方法的示意图;以及
31.图4是在加工操作期间加工参数的有意改变以及在加工操作的质量评估中对其考虑的示例。
具体实施方式
32.图1示出了示意性加工操作,其中沿着加工轨迹x加工具有特定加工参数pi(x)的工件w以形成加工结果r(x)。加工装置10包括加工机器人11,所述加工机器人承载用于加工工件w的相应加工头12并且沿着加工轨迹x引导以形成加工结果r(x)。为了加工工件w,从例如存储在数据库或存储器9中的多个可能的加工参数pi(x)选择加工参数的特定目标值p
i,soll
(x),用所述特定目标值加工工件w以便实现期望的加工结果。对加工装置10的手动干预或者在自适应加工操作中的自动机械干预(通过点划线表示)可以导致在加工操作期间加工参数的目标值p
i,soll
(x)的改变以及由此加工参数的期望的或必要的改变δpi(x)。在通过沿着加工轨迹x对被加工工件w进行适当检查对加工操作的加工结果r(x)进行后续的质量监测的情况下,加工参数从加工参数的目标值p
i,soll
(x)的这种改变δpi(x)在已知的方法中通常不自动地考虑,由此可能出现对工件w的质量的错误评估。由于常规的质量控制系统在有意地改变加工参数δpi(x)时失灵的事实,由于改变的加工结果r
′
(x)不对应于预期加工结果r(x),因此通常必须进行以有意改变的加工参数δpi(x)加工的工件w的复杂手动检查。
33.例如,加工装置10可以是用于在工件w上执行接合过程的焊接装置。在该情况下,将焊炬紧固到焊接机器人,通过所述焊接机器人将两个或更多个工件w彼此接合,或者可以将层施加到工件w。在该情况下,加工结果r(x)是待接合的两个或更多个工件w之间的焊缝或工件w的表面上的焊道。此外,加工装置10还可以由用于处理工件w表面具有等离子体喷枪的装置、喷涂装置以及更多形成。取决于加工操作,沿着加工轨迹x的加工结果r(x)不同,并且沿着加工轨迹x的加工操作和相应的加工结果r(x)的质量的评估也不同。
34.图2a至2d示意性地示出了用各种传感器2评估加工操作的质量的方法,所述传感器用于基于作为加工操作的焊接过程测量沿着加工轨迹x的加工操作的相应的加工结果r(x)。
35.图2a示出在加工工件w期间或紧接加工工件w之后进行的加工操作的质量评估(所谓的
″
在线
″
质量评估)。相应地,用于测量加工操作的加工结果r(x)的传感器2沿着工件w的
加工轨迹x布置在加工头12处或之后,使得可以紧接加工操作之后沿着加工轨迹x测量加工结果r(x)。例如,加工头12可以是焊炬8,通过所述焊炬将可消耗的焊丝7进给到工件w以用于执行接合过程或堆焊过程。电弧lb在焊丝7的端部和工件w之间燃烧,从而熔化焊丝7和工件w。用于测量沿着工件w的加工轨迹x的加工结果r(x)的可能传感器2例如是光学传感器3、相机4、x射线传感器5或温度传感器6,其测量沿着加工轨迹x的加工结果r(x)并根据沿着加工轨迹x的点提供相应的传感器信号sj(x)。在
″
在线
″
质量评估中,用传感器2测量沿着加工轨迹x的加工结果的速度优选地对应于加工操作的速度,也就是说加工速度,例如在焊接过程中的焊接速度vs(x)。
36.作为
″
在线
″
质量评估的替代或补充,根据图2b,也可以进行
″
离线
″
质量评估,其中在进行加工操作之后沿着加工轨迹x用相应的传感器2、例如光学传感器3、相机4或x射线传感器5等测量工件w或加工结果r(x),并且提供相应的传感器信号sj(x)。在
″
离线
″
质量评估的情况下,在完成工件w的加工之后用传感器2测量沿着加工轨迹x的加工结果r(x)的速度可以高于加工速度。然而,与
″
在线
″
质量评估相反,
″
离线
″
质量评估代表了额外的时间支出。
37.在图2c中,绘出了加工操作的质量评估的方法,其中为了分析加工结果r(x)而沿着加工轨迹x破坏工件w,其方式是,在加工结果r(x)的区域中沿着加工轨迹x在加工结果r(x)的多个点处产生工件w的显微切片。这些显微切片可以用相应的传感器2和图像处理方法来测量并且提供传感器信号sj(x),其类似地提供关于在工件w上的加工操作和在沿着加工轨迹x的特定点处的加工结果r(x)的质量的信息。例如,在焊接过程期间,这样的显微切片可以提供焊缝的焊透深度的指示作为加工结果r(x)。
38.如图2d中所示,从加工结果r(x)的各种传感器信号sj(x)确定质量参数qk(x),其表征相应加工任务的加工操作的加工结果r(x)的质量。取决于加工任务,可以存在不同的质量参数qk(x),其量化沿着加工轨迹x的加工结果r(x)的质量。为了评估质量,现在将至少一个质量参数qk(x)与质量参数阈值,例如上质量参数阈值q
k,o
(x)和下质量参数阈值q
k,u
(x)进行比较。如果超过质量参数阈值q
k,o
(x)、q
k,u
(x),则假设不满足质量,这用
″
nio
″
(不合格)标记。如果所有质量参数qk(x)在其质量参数阈值q
k,o
(x)、q
k,u
(x)内,则认为满足加工操作的质量并且将工件w分级为
″
io
″
(合格)。如果在加工操作期间存在加工参数的有意手动或自动进行的改变δpi(x),则加工结果r
′
(x)因此改变。如果现在用传感器2测量该改变的加工结果r
′
(x),并且由此确定质量参数q
′k(x)并将其与原始质量参数阈值q
k,o
(x)、q
k,u
(x)进行比较,则通常会产生错误质量说明。因此,本发明的目的在于在加工操作期间在加工操作和改变的加工结果r
′
(x)的质量的评估中自动地考虑加工参数的有意进行的改变δpi(x)。这将优选地导致适配的和改变的质量参数阈值q
′
k,o
(x)、q
′
k,u
(x)。
39.图3示出了根据本发明的用于评估在工件w上沿着加工轨迹x的加工操作和加工结果r(x)的质量的方法的示意图。用于加工操作的质量评估的装置1接收各种传感器信号sj(x),其在加工操作期间通过安装在加工装置10的加工头12上的传感器2测量沿加工轨迹x的加工结果r(x)(
″
在线
″
质量评估)。替代地或附加地,在加工操作之后通过用相应的传感器2沿着加工轨迹x测量加工结果r(x)而被记录的传感器信号sj(x)提供给用于质量评估的装置1。从至少一个传感器信号sj(x)确定至少一个质量参数qk(x),并且将至少一个质量参数qk(x)与质量参数阈值q
k,o
(x)、q
k,u
(x)进行比较以用于评估加工操作和沿着加工轨迹x的
加工结果r(x)的质量。如果超过质量参数阈值q
k,o
(x)、q
k,u
(x),则假设不满足质量并且将工件分级为
″
nio
″
(不合格),其例如在显示器13上被指示。如果所有质量参数qk(x)在其质量参数阈值q
k,o
(x)、q
k,u
(x)内,则认为满足加工操作和加工结果r(x)的质量并且将工件w分级为
″
io
″
(合格),其例如在显示器13上被指示。另外,如果超过质量参数阈值q
k,o
(x)、q
k,u
(x),也可以输出警告,例如扬声器14上的声学警告。
40.根据本发明,在评估加工操作和沿加工轨迹x的加工结果r(x)的质量时,在工件w的加工轨迹
×
的加工期间自动地考虑加工参数从加工参数的目标值p
i,soll
(x)的进行的改变δpi(x),其通过加工装置10与用于加工操作的质量评估的装置1的连接示出。这例如可以通过如下方式进行,基于改变的状况,也限定适配的质量参数阈值q
′
k,o
(x),q
′
k,u
(x),其针对加工参数的改变δpi(x)被存储或者通过相应的计算规则限定。加工操作和改变的加工结果r
′
(x)的质量的自动评估因此自动地基于适配的质量参数阈值q
′
k,o
(x),q
′
k,u
(x),因此可以提高质量监测的可靠性。此外,这使质量评估适合于自适应加工系统。结果,即使由于通常出现的公差而根据加工参数的改变δpi(x)以改变的加工参数加工并且可以提供其他加工结果r
′
(x)的工件w作为理想工件w也可以通过质量评估系统确定为
″
io
″
(合格),而不需要复杂的手动检查。适配的质量参数阈值q
′
k,o
(x)、q
′
k,u
(x)可以由从用于特定加工参数pi(x)的测试加工操作确定的存储质量参数阈值q
k,o,g
(x)、q
k,u,g
(x)例如通过存储质量参数阈值q
k,o,g
(x)、q
k,u,g
(x)的内插确定。
41.图4示出了在加工操作期间加工参数的有意改变δpi(x)以及在使用焊接过程的加工操作的质量评估中对其考虑的示例。在图的左侧部分中,工件w在截面图中在加工之前在上方示出并且在加工之后或在焊接过程之后在下方示出。这涉及在两个搭接布置的工件w上形成搭接焊缝。工件w通常无间隙地上下叠置并且焊接过程以预设的焊接参数进行。在质量监测中,例如,焊缝n的宽度b(x)和高度h(x)被确定为沿着加工轨迹x的质量参数,并且与焊缝n的宽度bo(x)、bu(x)和高度ho(x)、hu(x)的阈值进行比较。如果满足条件bu(x)《b《bo(x)和hu(x)《h《ho(x),则加工操作的质量被评估为正面并且工件被分类为
″
io"。
42.在实践中通常出现公差,公差例如可能导致工件w之间的间隙d,如在图4的右侧部分中所示。在焊接过程期间,例如手动地或自动地(在自适应焊接过程中)作用这些改变的条件,例如方式在于,增加焊丝的传送速度vd(x)和焊接电流i(x)并降低焊接速度vs(x)。这导致焊缝n具有比在没有间隙d的情况下加工工件w(图4的左侧部分)时更大的宽度b
′
和更大的高度h
′
。如果在没有自动考虑改变的条件和加工参数的有意进行的改变的情况下进行质量评估,则焊缝n的宽度b
′
和高度h
′
将被评估为不允许并且加工操作的质量被负面地评估,并且工件例如被标记为废品(
″
nio
″
:不合格)或者被送去进行手动检查或再加工。
43.在根据本发明的用于质量评估的方法中,现在考虑加工参数的进行的改变δpi(x),其方式在于使加工参数的有意进行的改变δpi(x)(这里,例如,传送速度vd(x)和焊接电流i(x)的增加以及焊接速度vs(x)的降低)对于质量评估是已知的并且在质量评估中对其进行考虑。例如,基于加工参数的改变δpi(x)适配的质量参数的阈值q
′
k,o
(x)、q
′
k,u
(x)被限定用于评估加工操作的质量。在所示的示例中,焊缝n的宽度b
′o(x)、b
′u(x)的上和下阈值以及焊缝n的高度h
′o(x)、h
′u(x)的上和下阈值将适配改变的焊接参数。结果,在图4的右侧部分中的改变的加工结果r
′
(x)或改变的焊缝n
′
在质量方面也被正确地评价为正面,原因是满足条件b
′u(x)《b
′
《b
′o(x)和h
′u(x)《h
′
《h
′o(x)。由于自动考虑加工参数的有意进行
的改变δpi(x),因此在质量监测中,工件w在该情况下也可以正确地分类为
″
io
″
并且可以省略工件w的手动检查。
44.在加工参数的改变δpi(x)的情况下质量参数的适配阈值q
′
k,o
(x)、q
′
k,u
(x)与正常加工参数pi(x)的质量参数q
k,o
(x)、q
k,u
(x)的原始阈值一样在表中或根据特定规则存档和存储。位于质量参数q
k,o
(x)、q
k,u
(x)的存储值和阈值之间的加工参数pi(x)可以通过内插法确定。质量评估系统可以访问该数据,而与它们可用或存储的位置无关。代替质量参数q
k,o
(x)、q
k,u
(x)的上阈值和下阈值,也可以使用质量参数平均值q
k,m
(x)和该平均值周围的最大质量参数波动范围δqk来评估加工结果r(x)的质量。