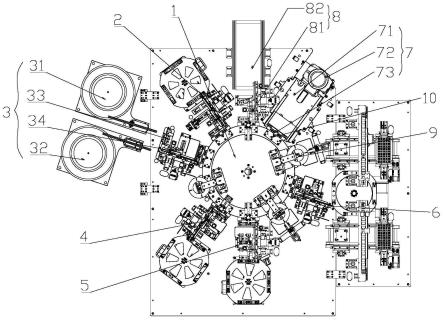
1.本发明涉及电池盖板组装技术领域,尤其涉及一种电池盖板自动组装设备及其使用方法。
背景技术:2.如图20所示,现有的电池盖板包括正极压板101、负极压板102、弱导板103、绝缘板104、基板105、止动架106、铝铆钉107和铜铆钉108;正极压板101、负极压板102、弱导板103、绝缘板104、基板105、止动架106、铝铆钉107和铜铆钉108按照从前往后的顺序依次逐一进行组装。
3.在电池盖板组装过程中需要将上述零件逐一组装在一起,目前的组装方式都是直线式的加工,整个设备占用的长度较大,并且占用空间也较大,需要配合很多工作人员,成大较大,并且现有的生产线需要将上述的零件逐按工序逐一进行组装,工序多、生产麻烦,大大影响了电池盖板的生产组装效率。
技术实现要素:4.本发明所要解决的是现有电池盖板组装设备占用空间大以及效率低的技术问题,提供了一种减小电池盖板设备占用空间以及提升整体电池盖板组装效率的电池盖板自动组装设备。
5.为本发明之目的,采用以下技术方案予以实现:
6.一种电池盖板自动组装设备,包括机架、设置在机架上的旋转盘装置、设置在机架上且周向依次排列设置在旋转盘装置外圈的正负极压板供料组装装置、弱导板和绝缘板供料组装装置、基板供料组装装置、止动架供料组装装置、铆钉供料组装装置、铆接装置和下料装置;所述旋转盘装置的外侧周向上设置有若干工位载具;所述正负极压板供料组装装置用于将正极压板和负极压板组装至工位载具上;所述弱导板和绝缘板供料组装装置用于将弱导板供料组装至工位载具的正极压板上,将绝缘板供料组装至工位载具的负极压板上;所述基板供料组装装置用于将基板组装至工位载具的弱导板和绝缘板上;所述止动架供料组装装置用于将止动架组装至所述工位载具的基板上;所述铆钉供料组装装置用于将铜铆钉和铝铆钉供料组装至工位载具的止动架上;所述铆接装置用于铜铆钉和铝铆钉铆接在止动架上;所述下料装置用于将铆接完成后的电池盖板成品转移下料。该设备通过转盘式的结构能够大大节省占用空间,并且能够进一步提升电池盖板组装效率。
7.作为优选,所述旋转盘装置包括旋转盘驱动机构、定盘和旋转盘;所述定盘固定连接在旋转盘驱动机构上,所述旋转盘转动连接在旋转盘驱动机构上,多个所述工位载具周向间隔排列设置在旋转盘的外圈上;每个工位载具均包括载具支撑板、第一侧向夹紧组、第二侧向夹紧组和纵向夹紧组;所述载具支撑板固定连接在旋转盘上,载具支撑板上分别设置有正极阶梯槽和负极阶梯槽;所述正极阶梯槽的底部设置有第一铆接孔;负极阶梯槽的底部设置有第二铆接孔;所述纵向夹紧组升降连接在载具支撑板上,且纵向夹紧组实现纵
向压紧电池盖板;所述第一侧向夹紧组和第二侧向夹紧组分别位于转动连接在载具支撑板的两侧,第一侧向夹紧组和第二侧向夹紧组相配合用于将电池盖板的两侧;且夹紧纵向夹紧组下压时,纵向夹紧组驱动第一侧向夹紧组和第二侧向夹紧组向两侧转动打开;
8.所述纵向夹紧组包括多根载具升降导杆、载具夹紧升降板、载具夹紧连接板和载具压板;多根所述载具升降导杆纵向设置在载具支撑板上;所述载具夹紧升降板升降连接在载具升降导杆上;所述载具夹紧连接板固定连接在载具夹紧升降板上;载具支撑板上位于载具夹紧连接板下方设置有用于载具夹紧连接板穿过的压紧通孔;载具夹紧连接板的下部设置有铰接凹口;所述载具压板的一端转动连接在铰接凹口内,且载具压板的中部转动连接在压紧通孔处;载具压板的另一端用于压紧电池盖板;载具压板与载具夹紧升降板之间设置有夹紧弹簧;所述载具夹紧升降板的底部设置有多个升降弹簧;载具支撑板上设置有相对应且用于限位所述升降弹簧的弹簧限位杆;所述载具夹紧升降板的两侧分别设置有导向柱;
9.所述第一侧向夹紧组和第二侧向夹紧组对称设置且结构相同;第一侧向夹紧组包括侧向夹板、侧向限位板和转动导向板;所述侧向夹板通过侧向转轴转动连接在载具支撑板一侧;所述转动导向板固定连接在侧向夹板上,且转动导向板限位在载具夹紧升降板与侧向夹板之间,转动导向板上设置有导向通道;所述导向柱位于导向通道内,且导向柱沿着导向通道下移时,使转动导向板向外侧转动打开;所述侧向夹板的夹紧部底面设置有用于夹紧基板的基板夹紧凹口;侧向夹板的夹紧部内侧设置用于限位止动架的侧向限位口;所述侧向限位板设置在侧向夹板的顶部,且侧向限位板延伸至侧向限位口内。该旋转盘装置便于节省占用空间,并且能够进一步对电池盖板上的组件进行限位固定,提升组装精确性。
10.作为优选,所述定盘的外圈周向设置有多个用于下压纵向夹紧组的纵向压紧驱动组件和多个用于检测工位载具上零件的检测组件,且机架上对应检测组件处还设置有用于将半成品取出的排料组件。通过检测工位载具能够进一步提升组装的合格率。
11.作为优选,所述正负极压板供料组装装置包括正负极压板供料机构、正负极压板二次定位检测机构和正负极压板转移机构;所述正负极压板供料机构用于将正极压板和负极压板进行供料;所述正负极压板二次定位检测机构用于将正负极压板进行二次定位;所述正负极压板转移机构用于将正负极压板从正负极压板供料机构转移至正负极压板二次定位检测机构,并将正负极压板二次定位检测机构上的正负极压板转移至工位载具上。通过正负极压板供料组装装置能够将正极压板和负极压板同时进行输送组装,无需分开进行,大大提升了正负极压板供料组装效率;
12.所述正负极压板供料机构包括正负极压板供料驱动电机组件、正负极压板供料旋转盘、正极压板顶料组件和负极板顶料组件;所述正负极压板供料驱动电机组件设置在机架上,所述正负极压板供料旋转盘转动连接在正负极压板供料驱动电机组件上,正负极压板供料旋转盘的外圈上间隔排列设置有多个正负极压板盛放工位,每个正负极压板盛放工位上设置有正负极压板盛放架;所述正负极压板盛放架的一侧设置有正极压板盛放槽;所述正极压板盛放槽内纵向设置有正极压板盛放定位杆;正极压板盛放槽的底部设置有至少一个第一顶料通孔;正负极压板盛放架的另一侧设置有负极压板盛放槽;所述负极压板盛放槽内纵向设置有负极压板盛放定位杆;所述负极压板盛放槽的底部设置有至少一个第二顶料通孔;所述正极压板顶料组件位于出料端的正负极压板盛放架的正极压板盛放槽下
方;所述负极板顶料组件位于出料端的正负极压板盛放架的负极压板盛放槽下方;正极压板顶料组件包括顶料支架、顶料滑台、顶料连接板和至少一根顶料杆;所述顶料支架固定设置在正负极压板供料驱动电机组件上,所述顶料滑台纵向设置在顶料支架上;所述顶料连接板固定连接在顶料滑台的滑块上,所述顶料杆设置在顶料连接板的顶部,且顶料杆与第一顶料通孔对齐;
13.所述正负极压板二次定位检测机构包括二次定位支架、正极压板检测组件、负极压板检测组件、正极压板翻转组件和负极压板翻转组件;所述二次定位支架设置在机架上,二次定位支架的两侧分别设置有正极压板阶梯孔和负极压板阶梯孔;二次定位支架上位于正极压板阶梯孔的外侧设置有第一翻转移动空间,且第一翻转移动空间与正极压板阶梯孔相连通;二次定位支架上位于负极压板阶梯孔的外侧设置有第二翻转移动空间,且第二翻转移动空间与负极压板阶梯孔相连通;
14.所述正极压板检测组件和负极压板检测组件分别安装在二次定位支架上,且正极压板检测组件位于正极压板阶梯孔下方,负极压板检测组件位于负极压板阶梯孔下方,正极压板检测组件包括压板检测支架、压板检测摄像头和压板检测光源;所述压板检测支架设置在二次定位支架的下部,所述压板检测摄像头设置在二次定位支架上,所述压板检测光源位于压板检测摄像头上方;所述正极压板翻转组件和负极压板翻转组件分别对称设置在二次定位支架的两侧,正极压板翻转组件包括压板翻转升降气缸、压板翻转升降板、压板翻转气缸和压板夹爪气缸;所述压板翻转升降气缸纵向设置在二次定位支架的一侧,所述压板翻转升降板连接在压板翻转升降气缸的移动部上,所述压板翻转气缸设置在压板翻转升降板上,所述压板夹爪气缸连接在压板翻转气缸的旋转部上,且压板夹爪气缸位于第一翻转移动空间内;
15.所述正负极压板转移机构包括压板转移支架、压板转移电机、电机转轴连接板、压板转移导向板、压板转移活动板、压板转移连接板、第一压板吸板和第二压板吸板;所述压板转移支架设置在机架上,压板转移支架上设置有用于感应压板位置的感应器;所述压板转移导向板设置在上,压板转移导向板上设置有u型导向槽;所述压板转移电机设置在压板转移支架上,所述电机转轴连接板的一端与压板转移电机的转轴上连接,电机转轴连接板的另一端后侧设置有压板导向轮;所述压板导向轮配合设置在u型导向槽内,电机转轴连接板的另一端前侧与所述压板转移活动板固定连接,压板转移支架上设置有至少一条压板水平滑轨;压板转移活动板的后部设置有至少一条压板升降滑轨;所述压板升降滑轨通过压板滑轨连接板与压板水平滑轨连接;压板转移连接板设置在压板转移活动板的底部,所述的第一压板吸板和第二压板吸板分别设置在压板转移连接板的两侧,第一压板吸板和第二压板吸板上均设置有至少一个正极压板吸头和至少一个负极压板吸头。通过上述结构进一步提升了正负极压板组装的精确性和组装效率。
16.作为优选,所述弱导板和绝缘板供料组装装置包括弱导板供料震动盘、绝缘板供料震动盘、弱导板和绝缘板二次定位架以及弱导板和绝缘板转移组件;所述弱导板和绝缘板二次定位架设置在弱导板供料震动盘和绝缘板供料震动盘的出料端处,所述弱导板和绝缘板转移组件用于将弱导板和绝缘板转移至弱导板和绝缘板二次定位架上,并将弱导板和绝缘板二次定位架定位后的弱导板和绝缘板转移至工位载具上。通过弱导板和绝缘板供料组装装置提升了弱导板和绝缘板的供料组装效率。
17.作为优选,所述基板供料组装装置包括基板供料机构、基板二次定位架和基板转移机构;所述基板供料机构用于将基板进行供料;所述基板二次定位架用于将基板进行二次定位;所述基板转移机构用于将基板从基板供料机构转移至基板二次定位架,并将基板二次定位架上的基板转移至工位载具上;所述基板供料机构包括基板供料驱动电机组件、基板供料旋转盘、基板顶料组件;所述基板供料驱动电机组件设置在机架上,所述基板供料旋转盘转动连接在基板供料驱动电机组件上,基板供料旋转盘的外圈上间隔排列设置有多个基板盛放工位,每个基板盛放工位上设置有基板盛放板;基板盛放板上设置有多根基板顶板导杆;所述基板盛放板上设置有多个基板顶料通孔;所述基板顶料组件包括基板顶料支架、基板顶料滑台、基板顶料连接板和多根基板顶料杆;所述基板顶料支架固定设置在基板供料驱动电机组件上,所述基板顶料滑台纵向设置在基板顶料支架上;所述基板顶料连接板固定连接在基板顶料滑台的滑块上,多根所述基板顶料杆设置在顶料连接板的顶部,且基板顶料杆与基板顶料通孔一一对应;基板二次定位架设置在机架上,基板二次定位架的顶部设置有与基板形状相匹配的基板二次定位槽;基板二次定位架的下部设置有用于检测基板正反的传感器,且机架上位于基板二次定位架内侧设置有基板排料盒;所述基板转移机构与正负极压板转移机构结构相同;所述止动架供料组装装置和基板供料组装装置的结构相同。通过基板供料组装装置进一步提升了基板供料组装效率和供料组装精确度;
18.作为优选,所述铆钉供料组装装置包括第一铆钉供料机构、第二铆钉供料机构、铆钉供料衔接机构、铆钉二次定位检测机构和铆钉转移机构;所述铆钉供料衔接机构位于第一铆钉供料机构和第二铆钉供料机构之间;所述第一铆钉供料机构和第二铆钉供料机构分别用于将铜铆钉和铝铆钉供料至铆钉供料衔接机构;所述铆钉转移机构用于将铜铆钉和铝铆钉转移至铆钉二次定位检测机构上,铆钉二次定位检测机构用于将铜铆钉和铝铆钉进行二次定位检测,二次定位检测后,铆钉转移机构用于将定位后的铜铆钉和铝铆钉转移至旋转盘装置上;
19.所述第一铆钉供料机构和第二铆钉供料机构结构相同且对齐设置;第一铆钉供料机构包括铆钉供料支架、铆钉供料驱动组件、铆钉供料支撑板、第一铆钉顶料组件、第二铆钉顶料组件、供料盘夹紧组件、供料空盘盛放组件和铆钉转移组件;所述铆钉供料支架设置在机架上,铆钉供料支架的进料端纵向设置有第一供料盘限位杆组;铆钉供料支架的出料端纵向设置有第二供料盘限位杆组;所述铆钉供料驱动组件设置在铆钉供料支架上;所述铆钉供料支撑板通过铆钉供料滑轨滑动连接在铆钉供料支架上,铆钉供料支撑板与铆钉供料驱动组件的驱动部连接,并带动铆钉供料支撑板在铆钉供料支架上移动;铆钉供料支撑板上设置有供料顶升通孔;所述第一铆钉顶料组件设置在铆钉供料支架的进料端,且第一供料盘限位杆组位于下方,所述第二铆钉顶料组件设置在铆钉供料支架的出料端,且位于第二供料盘限位杆组下方;所述供料盘夹紧组件设置在铆钉供料支架的进料端的两侧,供料盘夹紧组件用于将倒数第二以上的供料盘夹紧固定;所述供料空盘盛放组件设置在铆钉供料支架的出料端的两侧;供料空盘盛放组件用于将空的供料盘进行堆叠;
20.所述铆钉供料驱动组件包括铆钉供料驱动电机、铆钉供料主动转轴、铆钉供料从动转轴和铆钉供料传输带;所述铆钉供料驱动电机设置在铆钉供料支架上,所述铆钉供料主动转轴转动连接在铆钉供料支架的进料端,且铆钉供料主动转轴与铆钉供料驱动电机连接,铆钉供料主动转轴上设置有铆钉供料主动轮;所述铆钉供料从动转轴转动连接在铆钉
供料支架的出料端,铆钉供料从动转轴上设置有铆钉供料从动轮;所述铆钉供料传输带张紧连接在铆钉供料主动轮和铆钉供料从动轮上,所述铆钉供料支撑板与铆钉供料传输带固定连接;
21.所述第一供料盘限位杆组与第二供料盘限位杆组结构相同,第一供料盘限位杆组包括四根料盘限位杆;四根所述料盘限位杆呈矩形排列在铆钉供料支架的两侧,且每根料盘限位杆的下部均设置有用于铆钉供料支撑板滑动的料盘输送口;
22.所述第一铆钉顶料组件和第二铆钉顶料组件结构相同;所述第一铆钉顶料组件包括铆钉顶料支撑板、铆钉顶料气缸和铆钉顶料升降板;所述铆钉顶料支撑板设置在铆钉供料支架上;所述铆钉顶料气缸纵向设置在铆钉顶料支撑板上,所述铆钉顶料升降板连接在铆钉顶料气缸的顶部,且铆钉顶料升降板通过多根顶料升降导杆升降移动连接在铆钉顶料支撑板上;所述铆钉顶料升降板与供料顶升通孔对齐设置;
23.所述供料盘夹紧组件包括第一供料盘夹紧气缸模块和第二供料盘夹紧气缸模块;所述第一供料盘夹紧气缸模块包括供料盘夹紧支撑板、供料盘夹紧气缸和l型夹紧块;所述供料盘夹紧气缸通过供料盘夹紧支撑板水平设置在铆钉供料支架进料端的一侧;l型夹紧块设置在供料盘夹紧气缸的移动部;且l型夹紧块的横板位于铆钉供料支撑板上方;所述第二供料盘夹紧气缸模块和第一供料盘夹紧气缸模块对称设置且结构相同;
24.所述供料空盘盛放组件包括第一供料空盘盛放模块和第二供料空盘盛放模块;所述第一供料空盘盛放模块包括供料空盘盛放支架和供料空盘盛放转动板;所述供料空盘盛放支架设置在铆钉供料支架出料端的一侧;供料空盘盛放转动板通过转动扭簧转动连接在供料空盘盛放支架上,供料空盘盛放转动板呈向上倾斜状,且供料空盘盛放转动板通过转动扭簧的作用力能够使铆钉供料支撑板上的供料空盘向上通过供料空盘盛放转动板后,无法再向下回至铆钉供料支撑板上;所述第二供料空盘盛放模块和第一供料空盘盛放模块对称设置且结构相同;
25.所述铆钉转移组件包括铆钉转移龙门架、铆钉转移滑台、铆钉转移连接板、铆钉转移升降气缸和铆钉转移吸板;所述铆钉转移龙门架设置在机架上,且位于铆钉供料支架上方;所述铆钉转移滑台水平设置在铆钉转移龙门架的上部;所述铆钉转移连接板连接在铆钉转移滑台的滑板上;所述铆钉转移升降气缸设置在铆钉转移连接板上;所述铆钉转移吸板设置在铆钉转移升降气缸的底部,铆钉转移吸板上设置有铆钉吸头;
26.所述铆钉供料衔接机构包括衔接旋转驱动组件、衔接固定盘和衔接旋转盘;所述衔接旋转驱动组件设置在机架上,所述衔接固定盘设置在衔接旋转驱动组件的固定部上;所述衔接旋转盘设置在衔接旋转驱动组件的旋转部上;衔接旋转盘的外圈周向间隔排列设置有多个铆钉载具工位;每个所述铆钉载具工位上设置有铆钉载具台;所述铆钉载具台的顶部两侧分别设置有第一铆钉盛放部和第二铆钉盛放部;所述第一铆钉盛放部和第二铆钉盛放部结构相同,第一铆钉盛放部包括铆钉盛放槽;所述铆钉盛放槽的底面设置有铆钉阶梯孔;
27.所述铆钉二次定位检测机构包括铆钉二次定位架、铆钉二次定位旋转气缸、铆钉二次定位板;所述铆钉二次定位架设置在机架上,所述铆钉二次定位旋转气缸水平设置在铆钉二次定位架上,所述铆钉二次定位板固定连接在铆钉二次定位旋转气缸的旋转部上,且铆钉二次定位架的两侧分别设置有用于铆钉二次定位板旋转限位的旋转限位板;铆钉二
次定位板的两侧分别设置有所述的第一铆钉盛放部和第二铆钉盛放部。通过上述结构无需将铜铆钉和铝铆钉分开进行加工,直接一次性将铜铆钉和铝铆钉组装至电池盖板上,进一步提升了铆钉供料组装效率。
28.作为优选,所述铆接装置包括铆接支架、铆接驱动电机和铆接冲压机构;所述铆接驱动电机和铆接冲压机构分别设置在铆接支架,且所述铆接驱动电机驱动铆接冲压机构进行铆接加工;所述下料装置包括下料转移机构和下料输送带机构;所述下料输送带机构的进料端衔接在下料转移机构的下方。通过上述结构进一步提升铆接效率和下料效率。
29.一种电池盖板自动组装设备的使用方法,应用上述的电池盖板自动组装设备,包括以下步骤:
30.s1、正负极压板供料组装:通过正负极压板供料组装装置将正极压板和负极压板一并供料组装至旋转盘装置的工位载具上,并通过旋转盘装置将装有正极压板和负极压板的工位载具旋转至弱导板和绝缘板供料组装装置处;
31.s2、弱导板和绝缘板供料组装:弱导板和绝缘板供料组装装置用于将弱导板供料组装至工位载具的正极压板上;将绝缘板供料组装至工位载具的负极压板上;弱导板和绝缘板组装后通过旋转盘装置将该工位载具旋转至检测工位通过检测组件进行弱导板和绝缘板组装检测,检测无误后再旋转至基板供料组装装置处;
32.s3、基板供料组装装置:基板供料组装装置用于将基板供料组装至工位载具的弱导板和绝缘板上;并通过旋转盘装置将装有基板的工位载具旋转至止动架供料组装装置处;
33.s4、止动架供料组装装置:止动架供料组装装置用于将止动架供料组装工位载具的基板上,并通过旋转盘装置将该工位载具旋转至检测工位通过检测组件进行止动架检测,检测无误后再旋转至铆钉供料组装装置处;
34.s5、铆钉供料组装装置:铆钉供料组装装置用于将铝铆钉和铜铆钉一并供料组装至工位载具的止动架上,并通过旋转盘装置将该工位载具旋转至检测工位通过检测组件进行铆钉组装检测,检测无误后再旋转至铆接装置处;
35.s6、铆接装置:铆接装置用于将铝铆钉和铜铆钉一并进行冲压组装;从而使铝铆钉和铜铆钉将正负极压板、弱导板、绝缘板、基板和止动架组装在一起,形成最终电池盖板的成品;通过旋转盘装置将装有成品的工位载具旋转至下料装置等待下料;
36.s7、下料装置:电池盖板铆接完成后,通过下料装置将成品转移下料。
附图说明
37.图1是本发明的电池盖板自动组装设备的结构示意图。
38.图2是本发明中旋转盘装置的结构示意图。
39.图3是本发明中工位载具的结构示意图。
40.图4是本发明中工位载具的放大示意图。
41.图5是本发明中排料组件和检测组件的结构示意图。
42.图6是本发明中检测组件的结构示意图。
43.图7是本发明中排料组件的结构示意图。
44.图8是本发明中正负极压板供料组装装置的结构示意图。
45.图9是本发明中正负极压板供料机构的结构示意图。
46.图10是本发明中正负极压板供料机构的放大图。
47.图11是本发明中正负极压板二次定位检测机构的结构示意图。
48.图12是本发明中正负极压板转移机构的结构示意图。
49.图13是本发明中基板供料组装装置的结构示意图。
50.图14是本发明中基板供料机构的结构示意图。
51.图15是本发明中基板二次定位架和基板转移机构的结构示意图。
52.图16是本发明中铆钉供料组装装置的结构示意图。
53.图17是本发明中第一铆钉供料机构的结构示意图。
54.图18是本发明中铆钉转移组件的结构示意图。
55.图19是本发明中铆钉供料衔接机构的结构示意图。
56.图20是本发明中铆钉二次定位检测机构和铆钉转移机构的结构示意图。
57.图21是现有的电池盖板正面的结构爆炸图。
58.图22是现有的电池盖板背面的结构爆炸图。
具体实施方式
59.为使本发明的上述目的、特征和优点能够更为明显易懂,下面结合附图对本发明的具体实施例做详细的说明。
60.如图1所示,一种电池盖板自动组装设备,包括机架、设置在机架上的旋转盘装置1、设置在机架上且周向依次排列设置在旋转盘装置1外圈的正负极压板供料组装装置2、弱导板和绝缘板供料组装装置3、基板供料组装装置4、止动架供料组装装置5、铆钉供料组装装置6、铆接装置7和下料装置8;旋转盘装置1的外侧周向上设置有十个工位载具10;正负极压板供料组装装置2对应第一工位;正负极压板供料组装装置2用于将正极压板和负极压板组装至工位载具10上。弱导板和绝缘板供料组装装置3对应第二工位,弱导板和绝缘板供料组装装置3用于将弱导板供料组装至工位载具10的正极压板上,将绝缘板供料组装至工位载具10的负极压板上。第三工位为检测工位,用于检测弱导板和绝缘板是否组装完好。基板供料组装装置4对应第四工位,基板供料组装装置4用于将基板组装至工位载具10的弱导板和绝缘板上。止动架供料组装装置5对应第五工位,止动架供料组装装置5用于将止动架组装至工位载具10的基板上。第六工位为检测工位,用于检测止动架和基板是否组装完好,并将组装失败的半成品排料取出。铆钉供料组装装置6对应第七工位,铆钉供料组装装置6用于将铜铆钉和铝铆钉供料组装至工位载具10的止动架上;第八工位为检测工位,用于检测铜铆钉和铝铆钉是否精确安装至止动架上,并将组装失败的半成品排料取出。铆接装置7对应第九工位,铆接装置7用于铜铆钉和铝铆钉铆接在止动架上;下料装置8对应第十工位,下料装置8用于将铆接完成后的电池盖板成品转移下料。该设备通过转盘式的结构能够大大节省占用空间,并且能够进一步提升电池盖板组装效率。
61.如图20和图21所示,现有的电池盖板包括正极压板101、负极压板102、弱导板103、绝缘板104、基板105、止动架106、铝铆钉107和铜铆钉108。正极压板101上设置有第一组装铆接孔1011,正极压板101的背面上且位于第一组装铆接孔1011外圈设置有正极铆接槽1012;负极压板102上设置有第二组装铆接孔1021,负极压板102的背面上且位于第二组装
铆接孔1021外圈设置有负极铆接槽1022。
62.弱导板103上设置有用于安装正极压板101的正极压板安装槽1031,弱导板103上设置有第三组装铆接孔1032;弱导板103上设置有两个第一基板定位凸块1033;绝缘板104上设置有用于安装负极压板102的负极压板安装槽1041,绝缘板104上设置有第四组装铆接孔1042;绝缘板104上设置有两个第二基板定位凸块1043。
63.基板105的两侧均设置有第五组装铆接孔1051;基板105的一侧设置有与两个第一基板定位凸块1033相匹配的弱导板定位孔1052;基板105的另一侧设置有与两个第二基板定位凸块1043相匹配的绝缘板定位孔1053;基板105的的中间设置有止动架定位凸块1054。
64.止动架106的两侧均设置有第六组装铆接孔1061;止动架106的中部设置有与止动架定位凸块1054相配合的基板配合凹槽1062。
65.组装时,将正极压板101和负极压板102分别放置在工位载具10上,将弱导板103盖在正极压板101上,使正极压板101组装在正极压板安装槽1031内,将绝缘板104盖在负极压板102上,使负极压板102组装在负极压板安装槽1041内,将基板105盖在弱导板103和绝缘板104上,并使两个弱导板定位孔1052插入至两个第一基板定位凸块1033上,使两个绝缘板定位孔1053插入至两个第二基板定位凸块1043上;将止动架106组装在基板105上,并使止动架定位凸块1054插入至基板配合凹槽1062内,最后将铝铆钉107插入正极侧,将铜铆钉108插入至负极侧,使整体铆接在一起。
66.如图2和图4所示,旋转盘装置1包括旋转盘驱动机构11、定盘12和旋转盘13;定盘12固定连接在旋转盘驱动机构11上,旋转盘13转动连接在旋转盘驱动机构11上,十个工位载具10周向间隔排列设置在旋转盘13的外圈上;每个工位载具10均包括载具支撑板14、第一侧向夹紧组15、第二侧向夹紧组16和纵向夹紧组17;载具支撑板14固定连接在旋转盘13上,载具支撑板14的外侧分别设置有正极阶梯槽141和负极阶梯槽142;正极阶梯槽141用于放置正极压板,负极阶梯槽142用于放置负极压板。正极阶梯槽141的底部设置有第一铆接孔143,通过第一铆接孔143用于铝铆钉的组装放入。负极阶梯槽142的底部设置有第二铆接孔144;通过第二铆接孔144用于铜铆钉的组装放入。纵向夹紧组17升降连接在载具支撑板14上,且纵向夹紧组17实现纵向压紧电池盖板;第一侧向夹紧组15和第二侧向夹紧组16分别位于转动连接在载具支撑板14的两侧,第一侧向夹紧组15和第二侧向夹紧组16相配合用于将电池盖板的两侧;且夹紧纵向夹紧组17下压时,纵向夹紧组17驱动第一侧向夹紧组15和第二侧向夹紧组16向两侧转动打开。
67.如图3所示,纵向夹紧组17包括两根载具升降导杆171、载具夹紧升降板172、载具夹紧连接板173和载具压板174;两根载具升降导杆171纵向设置在载具支撑板14上;载具夹紧升降板172升降连接在载具升降导杆171上;能够使载具夹紧升降板172进行顺畅的上下移动。载具夹紧连接板173固定连接在载具夹紧升降板172上;载具夹紧连接板173整体呈l型;载具支撑板14上位于载具夹紧连接板173下方设置有用于载具夹紧连接板173穿过的压紧通孔140,便于载具夹紧连接板173下降过程中得到足够的下降空间。载具夹紧连接板173的下部设置有铰接凹口1731;载具压板174的内端转动连接在铰接凹口1731内,且载具压板174的中部转动连接在压紧通孔140处;便于更好的控制载具压板174的压紧转动角度。载具压板174的外端用于压紧电池盖板上的基板或止动架。载具压板174与载具夹紧升降板172之间设置有夹紧弹簧;通过夹紧弹簧便于能够给载具压板174提供压力,从而使外力压向载
具夹紧升降板172使,通过夹紧弹簧的作用力压向载具压板174的内端,进而使载具压板174的外端能够向上抬起,进而能够使载具支撑板14上的基板或止动架处于解锁状态,当没有外力下压时,通过夹紧弹簧压的弹力向上牵引载具压板174的内端,能够使载具压板174的外端压向载具支撑板14上的基板或止动架处于锁紧状态。载具夹紧升降板172的底部设置有两个个升降弹簧1721;载具支撑板14上设置有相对应且用于限位升降弹簧1721的弹簧限位杆145;通过升降弹簧1721能够更好的支撑载具夹紧升降板172,在没有外界的压力时,能够支撑载具夹紧升降板172,防止载具夹紧升降板172下降,从而更好的使载具压板174将基板或止动架压紧。载具夹紧升降板172的两侧分别设置有导向柱1723;通过两侧导向柱1723用于分别带动第一侧向夹紧组15和第二侧向夹紧组16转动,从而能够使载具夹紧升降板172下降时,使第一侧向夹紧组15和第二侧向夹紧组16向两侧转动,实现打开,便于将基板105或止动架106放入。
68.如图3和图4所示,第一侧向夹紧组15和第二侧向夹紧组16对称设置且结构相同;第一侧向夹紧组15包括侧向夹板151、侧向限位板152和转动导向板146;侧向夹板151通过侧向转轴153转动连接在载具支撑板14一侧;转动导向板146固定连接在侧向夹板151上,且转动导向板146限位在载具夹紧升降板172与侧向夹板151之间,转动导向板146上设置有倾斜的导向通道147;导向柱1723位于导向通道147内,且导向柱1723沿着导向通道147下移时,使转动导向板146向外侧转动打开。侧向夹板151的夹紧部1511底面设置有用于夹紧基板的基板夹紧凹口1512;基板夹紧凹口1512呈u型状,便于更好的与基板105的侧部相匹配,从而夹紧时便于将基板105夹紧在基板夹紧凹口1512内,防止旋转输送过程中造成基板105移动。侧向夹板151的夹紧部1511内侧设置用于限位止动架的侧向限位口154;侧向限位口154的宽度与止动架106的宽度相匹配,便于更好的将止动架106进行限位夹紧,防止旋转输送过程中造成止动架106移动。侧向限位板152设置在侧向夹板151的顶部,且侧向限位板152延伸至侧向限位口154内。侧向限位板152用于夹紧止动架106两侧的塑料件竖板顶部,并且还能起到纠正塑料件的变形以及优化铆接的作用。
69.如图2至图7所示,定盘12的外圈周向设置有三个用于下压纵向夹紧组17的纵向压紧驱动组件18和三个用于检测工位载具10上零件的检测组件19,三个纵向压紧驱动组件18分别位于第四工位、第五工位和第十工位,位于第四工位处能够便于基板的放入,位于第五工位处能够便于止动架的放入,位于第十工位处便于将成品取出输送下料;三个检测组件19分别位于第三工位、第六工位和第八工位,位于第三工位能够对弱导板和绝缘板进行组装检测,位于第六工位能够对止动架和基板进行组装检测;位于第八工位用于对铜铆钉和铝铆钉进行检测。如图5所示,检测组件19包括检测支架191、检测摄像器192、检测光源板193和检测下压气缸194;检测支架191设置在定盘12的外圈上,检测摄像器192和检测光源板193分别设置在检测支架191的上部,检测摄像器192位于检测光源板193上方,且检测摄像器192中心与检测光源板193的中心对齐设置,检测下压气缸194通过检测下压气缸支撑板195设置在检测支架191上,且位于检测光源板193下方,检测下压气缸194用于下压纵向夹紧组17。机架上对应第六工位和第八工位的检测组件19的外侧还设置有用于将不合格半成品取出的排料组件9。该旋转盘装置1便于节省占用空间,并且能够进一步对电池盖板上的组件进行限位固定,提升组装精确性。
70.如图7所示,排料组件9包括排料顶料模块和排料取出模块;排料顶料模块包括排
料顶料气缸91、排料顶料板92和两根排料顶料杆93;排料顶料气缸91设置在机架上,排料顶料板92设置在排料顶料气缸91的顶部,两根排料顶料杆93分别设置在排料顶料板92的两侧,且与第一铆接孔143和第二铆接孔144对齐设置,通过排料顶料气缸91向上顶起,从而带动两根排料顶料杆93顶向不合格产品,将不合格产品顶出。
71.排料取出模块包括排料取出支架94、排料取出水平移动气缸95、排料取出升降气缸96和排料取出转动板97;排料取出支架94设置在机架上,且位于排料顶料模块外侧,排料取出水平移动气缸95设置在排料取出支架94上,排料取出升降气缸96通过排料取出升降架961设置在排料取出水平移动部951,排料取出水平移动部951上设置有u型支撑座952;排料取出升降移动部960上设置有贯穿排料取出升降移动部960的配合轴962;排料取出转动板97的一端设置有排料取出u型开口971,且排料取出转动板97上位于排料取出u型开口971的两侧设置有u型配合开口972;排料取出升降移动部960位于排料取出u型开口971内;配合轴962的两端配合设置在两侧的u型配合开口972内;排料取出转动板97的中部转动连接在u型支撑座952上,排料取出转动板97的另一端固定连接有l型取出板973;l型取出板973的转折处中部974设置有与载具压板174相配合的压板配合开口975,通过压板配合开口975防止与载具压板174发生干涉碰撞。将不合格产品顶出后,通过排料取出升降气缸96带动配合轴962下降,从而使配合轴962压向u型配合开口972,使排料取出转动板97的一端下压,进而使排料取出转动板97的另一端向上转动,能够使l型取出板973扣入至不合格产品的内侧,最后通过排料取出水平移动气缸95向外拉动将不合格产品取出,落入至废料盒内。通过检测工位载具10上的零件能够进一步提升电池盖板组装的合格率。
72.工作时,通过检测摄像器192对电池盖板进行检测,检测为不合格时,通过检测下压气缸194下压纵向夹紧组17使载具压板174的压紧端向上抬起,并使第一侧向夹紧组15和第二侧向夹紧组16向两侧打开,从而使电池盖板处于解锁打开状,通过排料顶料模块将电池盖板顶起,最后通过排料取出模块将顶起的电池盖板向外拉入废料盒内。
73.如图8所示,正负极压板供料组装装置2包括正负极压板供料机构21、正负极压板二次定位检测机构22和正负极压板转移机构23;正负极压板供料机构21用于将正极压板101和负极压板102进行供料;正负极压板二次定位检测机构22用于将正负极压板进行二次定位;正负极压板转移机构23用于将正负极压板从正负极压板供料机构21转移至正负极压板二次定位检测机构22,并将正负极压板二次定位检测机构22上的正负极压板转移至工位载具10上。通过正负极压板供料组装装置2能够将正极压板和负极压板同时进行输送组装,无需分开进行,大大提升了正负极压板供料组装效率。
74.如图8至图12所示,正负极压板供料机构21包括正负极压板供料驱动电机组件211、正负极压板供料旋转盘212、正极压板顶料组件213和负极板顶料组件214;正负极压板供料驱动电机组件211设置在机架上,正负极压板供料旋转盘212转动连接在正负极压板供料驱动电机组件211上,正负极压板供料旋转盘212的外圈上间隔排列设置有四个正负极压板盛放工位,每个正负极压板盛放工位上设置有正负极压板盛放架215;正负极压板盛放架215呈u型状,正负极压板盛放架215的一侧纵向设置有正极压板盛放槽2151;正极压板盛放槽2151用于正极压板叠放,正极压板盛放槽2151内纵向设置有正极压板盛放定位杆2152;正极压板盛放定位杆2152正好可以穿过正极压板的铆接孔,从而能够将正极压板进行定位罗列。正极压板盛放槽2151的底部设置有两个第一顶料通孔2153;两个第一顶料通孔2153
分别位于正极压板盛放定位杆2152的两侧,从而在顶起时能够保证两侧平整,使正极压板水平顶出。正负极压板盛放架215的另一侧设置有负极压板盛放槽2154;负极压板盛放槽2153内纵向设置有负极压板盛放定位杆2155;负极压板盛放槽2153的底部设置有两个第二顶料通孔2156;负极压板与正极压板大小不同,但叠放罗列方式相同。
75.如图9所示,正极压板顶料组件213位于出料端的正负极压板盛放架215的正极压板盛放槽2151下方;负极板顶料组件214位于出料端的正负极压板盛放架215的负极压板盛放槽2154下方;正极压板顶料组件213包括顶料支架2131、顶料滑台2132、顶料连接板2133和两根顶料杆2134;顶料支架2131固定设置在正负极压板供料驱动电机组件211上,顶料滑台2132纵向设置在顶料支架2131上;顶料连接板2133固定连接在顶料滑台2132的滑块上,顶料杆2134设置在顶料连接板2133的顶部,且顶料杆2134与第一顶料通孔2153对齐,通过两根顶料杆2134从两个第一顶料通孔2153穿过,从而将正极压板向上顶起,能够使最上面一块正极压板与正负极压板盛放架215顶部平齐,从而便于后续正负极压板转移机构23进行吸取转移组装。
76.如图11所示,正负极压板二次定位检测机构22包括二次定位支架221、正极压板检测组件222、负极压板检测组件223、正极压板翻转组件224和负极压板翻转组件225;二次定位支架221设置在机架上,二次定位支架221的两侧分别设置有正极压板阶梯孔2211和负极压板阶梯孔2212;正极压板阶梯孔2211用于放置正极压板,负极压板阶梯孔2212用于放置负极压板。二次定位支架221上位于正极压板阶梯孔2211的外侧设置有第一翻转移动空间2213,且第一翻转移动空间2213与正极压板阶梯孔2211相连通;第一翻转移动空间2213呈l型,通过第一翻转移动空间2213便于给正极压板翻转组件224提供升降移动的空间。二次定位支架221上位于负极压板阶梯孔2212的外侧设置有第二翻转移动空间2214,且第二翻转移动空间2214与负极压板阶梯孔2212相连通;第二翻转移动空间2214呈l型,通过第二翻转移动空间2214便于给负极压板翻转组件225提供升降移动的空间。
77.如图11所示,正极压板检测组件222和负极压板检测组件223分别安装在二次定位支架221上,且正极压板检测组件222位于正极压板阶梯孔2211下方,负极压板检测组件223位于负极压板阶梯孔2212下方,正极压板检测组件222和负极压板检测组件223结构相同,分别用于检测正极压板和负极压板是否装反。正极压板检测组件222包括压板检测支架2221、压板检测摄像头2222和压板检测光源2223;压板检测支架2221设置在二次定位支架221的下部,压板检测摄像头2222设置在二次定位支架221上,通过压板检测摄像头2222来检测正极压板101底部是否有正极铆接槽1012来判断是否装反。压板检测光源2223位于压板检测摄像头2222上方,且对齐设置,通过压板检测摄像头2222来检测正负极压板是否装反,若装反了通过正极压板翻转组件224和负极压板翻转组件225进行翻转操作。
78.如图11所示,正极压板翻转组件224和负极压板翻转组件225分别对称设置在二次定位支架221的两侧,正极压板翻转组件224和负极压板翻转组件225结构相同且对称设置。正极压板翻转组件224包括压板翻转升降气缸2241、压板翻转升降板2242、压板翻转气缸2243和压板夹爪气缸2244;压板翻转升降气缸2241纵向设置在二次定位支架221的一侧,压板翻转升降板2242连接在压板翻转升降气缸2241的移动部上,压板翻转气缸2243设置在压板翻转升降板2242上,压板夹爪气缸2244连接在压板翻转气缸2243的旋转部上,且压板夹爪气缸2244位于第一翻转移动空间2213内,通过压板翻转升降气缸2241能够带动压板夹爪
气缸2244在第一翻转移动空间2213内升降移动。动作时,通过压板夹爪气缸2244将正极压板101夹住,压板翻转升降气缸2241带动正极压板101向上移动至能够使压板夹爪气缸2244有翻转的空间,通过压板翻转气缸2243进行180度翻转,将正极压板翻转至正确状态后再放回至原来位置,松开压板夹爪气缸2244。通过二次定位能够进一步保证正负极压板组装的精确度,确保产品生产过程中的合格率。
79.如图12所示,正负极压板转移机构23包括压板转移支架231、压板转移电机232、电机转轴连接板2321、压板转移导向板233、压板转移活动板234、压板转移连接板235、第一压板吸板236和第二压板吸板237;压板转移支架231设置在机架上,压板转移支架231上设置有用于感应压板位置的压板感应器2310;通过压板感应器2310能够探测正负极压板供料机构21上的正负极压板盛放架215是否旋转到位,处于等待吸取转移的位置。压板转移导向板233设置在压板转移支架231上,压板转移导向板233上设置有开口向下的u型导向槽2331;压板转移电机232设置在压板转移支架231上,电机转轴连接板2321的一端与压板转移电机232的转轴上连接,电机转轴连接板2321的另一端设置有导向通孔2320;所述导向通孔2320内配合设置有压板导向轮2322;压板导向轮2322的一端活动配合在u型导向槽2331内,通过导向通孔2320能够给压板导向轮2322提供活动空间,从而便于电机转轴连接板2321在转动时能够带动压板导向轮2322在u型导向槽2331内移动。压板导向轮2322的另一端与所述压板转移活动板234固定连接,压板转移活动板234随着压板导向轮2322的移动,进行u型轨迹的移动。压板转移支架231上设置有两条压板水平滑轨2311;压板转移活动板234的后部设置有两条压板升降滑轨2342;通过滑轨提升移动流畅度。压板升降滑轨2342通过压板滑轨连接板2343与压板水平滑轨2311连接;压板转移连接板235设置在压板转移活动板234的底部,第一压板吸板236和第二压板吸板237分别设置在压板转移连接板235的两侧,第一压板吸板236和第二压板吸板237上均设置有两个正极压板吸头2361和两个负极压板吸头2362。通过第一压板吸板236上两侧的正极压板吸头2361和负极压板吸头2362能够一次性将正极压板和负极压板同时进行吸取,并且同时进行转移组装,提升转移效率和组装效率。通过上述结构进一步提升了正负极压板组装的精确性和组装效率。
80.工作时,将一组正极压板101和一组负极压板102分别叠放在正负极压板盛放架215的正极压板盛放槽2151和负极压板盛放槽2153内,通过正负极压板供料驱动电机组件211带动正负极压板供料旋转盘212将正负极压板转移至正负极压板二次定位检测机构22处,通过正极压板顶料组件213上的两个顶料滑台2132带动各自的顶料杆2134向上顶起,将正极压板101和负极压板102向上顶出,使位于顶部的正极压板101和负极压板102与正负极压板盛放架215平齐,通过正负极压板转移机构23上的第一压板吸板236将顶部的正极压板101和负极压板102吸取转移至压板二次定位检测机构22中的正极压板阶梯孔2211和负极压板阶梯孔2212上,此时压板夹爪气缸2244的两个夹爪处于竖直状态,不会干涉到正负极压板转移机构23转移正极压板101。通过正极压板检测组件222和负极压板检测组件223分别对正极压板101和负极压板102进行检测,查看是否装反情况,若正极压板101出现装反情况,通过正极压板翻转组件224上的压板夹爪气缸2244的两个夹爪收拢,将正极压板101的上下两侧夹住后,通过压板翻转升降气缸2241向上移动至能够使压板夹爪气缸2244有翻转的空间,将正极压板101进行180度翻转,将正极压板翻转至正确状态后放回至正极压板阶梯孔2211上,负极也是通过相同操作,将正极压板101和负极压板102检测无误后,通过正负
极压板转移机构23上的第二压板吸板237将正极压板101和负极压板102吸取转移组装至工位载具10上。
81.如图1所示,弱导板和绝缘板供料组装装置3包括弱导板供料震动盘31、绝缘板供料震动盘32、弱导板和绝缘板二次定位架33以及弱导板和绝缘板转移组件34;弱导板和绝缘板二次定位架33设置在弱导板供料震动盘31和绝缘板供料震动盘32的出料端处,弱导板和绝缘板转移组件34用于将弱导板103和绝缘板104转移至弱导板和绝缘板二次定位架33上,并将弱导板和绝缘板二次定位架33定位后的弱导板和绝缘板转移至工位载具10上,使弱导板103盖在正极压板101上,绝缘板104盖在负极压板102上。通过弱导板和绝缘板供料组装装置3提升了弱导板和绝缘板的供料组装效率。
82.如图13所示,基板供料组装装置4包括基板供料机构41、基板二次定位架42和基板转移机构43;基板供料机构41用于将基板进行供料;基板二次定位架44用于将基板进行二次定位;基板转移机构43用于将基板从基板供料机构41转移至基板二次定位架42,并将基板二次定位架44上的基板转移至工位载具10上。
83.如图13和图14所示,基板供料机构41包括基板供料驱动电机组件411、基板供料旋转盘412、基板顶料组件413;基板供料驱动电机组件411设置在机架上,基板供料旋转盘412转动连接在基板供料驱动电机组件411上,基板供料旋转盘412的外圈上间隔排列设置有四个基板盛放工位,每个基板盛放工位上设置有基板盛放板414;基板盛放板414上设置有三根基板顶板导杆415;分别位于左、中、右侧,并与基板105上的孔位对应,能够更好的将基板105平稳的放在基板盛放板414上。基板盛放板414上设置有四个基板顶料通孔416,通过基板顶料通孔416便于顶起基板时,能够保证基板105平稳上升,不会出现左右不齐的情况,保证基板105的平整度。
84.基板顶料组件413包括基板顶料支架4131、基板顶料滑台4132、基板顶料连接板4133和四根基板顶料杆4134;基板顶料支架4131固定设置在基板供料驱动电机组件411上,基板顶料滑台4132纵向设置在基板顶料支架4131上;基板顶料连接板4133固定连接在基板顶料滑台4132的滑块上,多根基板顶料杆4134设置在基板顶料连接板4133的顶部,且基板顶料杆4134与基板顶料通孔416一一对应;通过基板顶料杆4134穿过基板顶料通孔416将一组基板105向上顶起,使位于顶部的基板105与基板顶板导杆415的顶部平齐,便于基板转移机构43进行吸取转移,提升转移吸取的牢固度,以及转移的流畅度。
85.如图15所示,基板二次定位架42设置在机架上,基板二次定位架42的顶部设置有与基板形状相匹配的基板二次定位槽421;基板二次定位架42的下部设置有用于检测基板正反的基板传感器,通过基板传感器便于对旋转过来的基板进行检测,能够保证基板转到指定位置时,并与基板转移机构43对齐,从而便于基板转移机构43进行吸取转移。机架上位于基板二次定位架42外侧设置有基板排料盒;基板转移机构43与正负极压板转移机构23结构相同,且基板转移机构43的下部设置有用于感应基板位置的基板感应器430。止动架供料组装装置5和基板供料组装装置4的结构相同。通过基板供料组装装置4进一步提升了基板供料组装效率和供料组装精确度。
86.工作时,将一组基板105插入至三根基板顶板导杆415上,使一组基板105整齐规整的叠放在基板盛放板414上,将该组基板105通过基板供料驱动电机组件411带动基板供料旋转盘412旋转至基板顶料组件413上方,通过基板顶料组件413上的基板顶料滑台4132带
动四根基板顶料杆4134向上顶升,从而穿过基板顶料通孔416将基板盛放板414上的一组基板105顶起,使位于顶部的基板105与基板顶板导杆415的顶部平齐,通过基板转移机构43将位于顶部的基板105吸取转移至基板二次定位架42上的基板二次定位槽421上,通过基板二次定位架42上的基板检测器对基板105进行检测,检测为不合格时,通过基板转移机构43将不合格的基板105吸取转移至基板排料盒内,检测为合格时,通过基板转移机构43将合格的基板105转移组装至工位载具10上的弱导板和绝缘板上。
87.如图16至图20所示,铆钉供料组装装置6包括第一铆钉供料机构61、第二铆钉供料机构62、铆钉供料衔接机构63、铆钉二次定位检测机构64和铆钉转移机构65;铆钉供料衔接机构63位于第一铆钉供料机构61和第二铆钉供料机构62之间;第一铆钉供料机构61和第二铆钉供料机构62分别用于将铜铆钉108和铝铆钉107供料至铆钉供料衔接机构63;铆钉转移机构65用于将铜铆钉108和铝铆钉107转移至铆钉二次定位检测机构64上,铆钉二次定位检测机构64用于将铜铆钉108和铝铆钉107进行二次定位检测,二次定位检测后,铆钉转移机构65用于将定位后的铜铆钉108和铝铆钉107转移至旋转盘装置1上。
88.如图17所示,第一铆钉供料机构61和第二铆钉供料机构62结构相同且对齐设置;第一铆钉供料机构61包括铆钉供料支架611、铆钉供料驱动组件612、铆钉供料支撑板613、第一铆钉顶料组件614、第二铆钉顶料组件615、供料盘夹紧组件616、供料空盘盛放组件617和铆钉转移组件618;铆钉供料支架611设置在机架上,铆钉供料支架611的进料端纵向设置有第一供料盘限位杆组6111;铆钉供料支架611的出料端纵向设置有第二供料盘限位杆组6112;铆钉供料驱动组件612设置在铆钉供料支架611上;铆钉供料支撑板613通过铆钉供料滑轨610滑动连接在铆钉供料支架611上,铆钉供料支撑板613与铆钉供料驱动组件612的驱动部连接,并带动铆钉供料支撑板613在铆钉供料支架611上移动;铆钉供料支撑板613上设置有供料顶升通孔6131;第一铆钉顶料组件614设置在铆钉供料支架611的进料端,且位于第一供料盘限位杆组6111下方,第二铆钉顶料组件615设置在铆钉供料支架611的出料端,且位于第二供料盘限位杆组6112下方;供料盘夹紧组件616设置在铆钉供料支架611的进料端的两侧,供料盘夹紧组件616用于将倒数第二以上的供料盘夹紧固定;供料空盘盛放组件617设置在铆钉供料支架611的出料端的两侧;供料空盘盛放组件617用于将空的供料盘进行堆叠;铆钉转移组件618用于将铆钉供料盘上的铆钉吸取转移。
89.铆钉供料驱动组件612用于驱动铆钉供料支撑板613水平移动,第一铆钉顶料组件614用于将第一供料盘限位杆组6111内的铆钉供料盘顶起,第二铆钉顶料组件615用于将第二供料盘限位杆组6112内的铆钉供料盘顶起,供料盘夹紧组件616用于将第一供料盘限位杆组6111内的二层以上的铆钉供料盘夹紧;供料空盘盛放组件617用于存放空的铆钉供料盘;铆钉转移组件618用于将铆钉供料盘上的铆钉吸取转移。
90.铆钉供料驱动组件612包括铆钉供料驱动电机6121、铆钉供料主动转轴6122、铆钉供料从动转轴6123和铆钉供料传输带6124;铆钉供料驱动电机6121设置在铆钉供料支架611上,铆钉供料主动转轴6122转动连接在铆钉供料支架611的进料端,且铆钉供料主动转轴6122与铆钉供料驱动电机6121连接,铆钉供料主动转轴6122上设置有铆钉供料主动轮6125;铆钉供料从动转轴6123转动连接在铆钉供料支架611的出料端,铆钉供料从动转轴6123上设置有铆钉供料从动轮6126;铆钉供料传输带6124张紧连接在铆钉供料主动轮6125和铆钉供料从动轮6126上,铆钉供料支撑板613与铆钉供料传输带6124固定连接;通过铆钉
供料驱动电机6121驱动铆钉供料主动转轴6122旋转,从而通过铆钉供料主动转轴6122带动铆钉供料主动轮6125旋转,通过铆钉供料传输带6124驱动铆钉供料从动轮6126上的铆钉供料从动转轴6123旋转,进而实现通过铆钉供料传输带6124的传动,最终通过铆钉供料传输带6124的旋转带动铆钉供料支撑板613进行水平移动定位。
91.第一供料盘限位杆组6111与第二供料盘限位杆组6112结构相同,第一供料盘限位杆组6111包括四根料盘限位杆6113;四根料盘限位杆6113呈矩形排列在铆钉供料支架611的两侧,这样能够更好的配合矩形的铆钉供料盘,将铆钉供料盘进行限位。每根料盘限位杆6113的下部均设置有用于铆钉供料支撑板613滑动的料盘输送口6114,通过料盘输送口6114便于最底下一层的铆钉供料盘进行移动至中间,从而便于将铆钉供料盘上的铆钉逐一吸取转移。
92.第一铆钉顶料组件614和第二铆钉顶料组件615结构相同;第一铆钉顶料组件614包括铆钉顶料支撑板6141、铆钉顶料气缸6142和铆钉顶料升降板6143;铆钉顶料支撑板6141设置在铆钉供料支架611上;铆钉顶料气缸6142纵向设置在铆钉顶料支撑板6141上,铆钉顶料升降板6143连接在铆钉顶料气缸6142的顶部,且铆钉顶料升降板6143通过多根顶料升降导杆6144升降移动连接在铆钉顶料支撑板6141上;铆钉顶料升降板6143与供料顶升通孔6131对齐设置;通过铆钉顶料气缸6142带动铆钉顶料升降板6143上升穿过供料顶升通孔6131,使铆钉顶料升降板6143与第一供料盘限位杆组6111的顶部,将一组装满铆钉的铆钉供料盘放置在铆钉顶料升降板6143上,使铆钉顶料升降板6143下降,最终使最底下一盘的铆钉供料盘盛放在铆钉供料支撑板613上。
93.供料盘夹紧组件616包括第一供料盘夹紧气缸模块和第二供料盘夹紧气缸模块;第一供料盘夹紧气缸模块包括供料盘夹紧支撑板6161、供料盘夹紧气缸6162和l型夹紧块6163;供料盘夹紧气缸6162通过供料盘夹紧支撑板6161水平设置在铆钉供料支架611进料端的一侧;l型夹紧块6163设置在供料盘夹紧气缸6162的移动部;且l型夹紧块6163的横板6164位于铆钉供料支撑板613上方;第二供料盘夹紧气缸模块和第一供料盘夹紧气缸模块对称设置且结构相同;通过供料盘夹紧气缸6162带动l型夹紧块6163水平向内侧夹紧,当最底下一盘的铆钉供料盘盛放在铆钉供料支撑板613上后,使l型夹紧块6163的横板6164插入至最底下一盘与倒数第二盘之间空隙内,从而将倒数第二盘以上的铆钉供料盘进行限位防止下降,并对倒数第二盘以上的铆钉供料盘进行支撑,这样能够便于使最底下一盘的铆钉供料盘随着铆钉供料支撑板613进行移动,使倒数第二盘以上的铆钉供料盘进行固定。
94.供料空盘盛放组件617包括第一供料空盘盛放模块6171和第二供料空盘盛放模块6172;第一供料空盘盛放模块6171包括供料空盘盛放支架6173和供料空盘盛放转动板6174;供料空盘盛放支架6173设置在铆钉供料支架611出料端的一侧;供料空盘盛放转动板6174通过转动扭簧转动连接在供料空盘盛放支架6173上,供料空盘盛放转动板6174呈向上倾斜状,便于空的铆钉供料盘向上顶起时将两侧的供料空盘盛放转动板6174打开,使空的铆钉供料盘向上通过,供料空盘盛放转动板6174通过转动扭簧的作用力能够使铆钉供料支撑板613上的供料空盘向上通过供料空盘盛放转动板6174后,无法再向下回至铆钉供料支撑板613上;第二供料空盘盛放模块6172和第一供料空盘盛放模块6171对称设置且结构相同;将铆钉供料支撑板613上的铆钉供料盘上的铆钉都转移后,将铆钉供料支撑板613移动至第二供料盘限位杆组6112处,通过第二铆钉顶料组件615将铆钉供料支撑板613上空的铆
钉供料盘顶起,使铆钉供料盘穿过供料空盘盛放转动板6174后,第二铆钉顶料组件615下降,使空的铆钉供料盘盛放在两侧的供料空盘盛放转动板6174上无法回至铆钉供料支撑板613上,往后的每一盘都以相同的方式,先向上顶起,再使最底下一盘空的铆钉供料盘支撑在两侧的供料空盘盛放转动板6174上,等堆叠一组空的铆钉供料盘后便于一次性取出。
95.如图18所示,铆钉转移组件618包括铆钉转移龙门架6181、铆钉转移滑台6182、铆钉转移连接板6183、铆钉转移升降气缸6184和铆钉转移吸板6185;铆钉转移龙门架6181设置在机架上,且位于铆钉供料支架611上方;铆钉转移滑台6182水平设置在铆钉转移龙门架6181的上部;铆钉转移连接板6183连接在铆钉转移滑台6182的滑板上;铆钉转移升降气缸6184设置在铆钉转移连接板6183上;铆钉转移吸板6185设置在铆钉转移升降气缸6184的底部,铆钉转移吸板6185上设置有铆钉吸头6186;通过铆钉转移滑台6182带动铆钉转移升降气缸6184移动至铆钉供料盘上方,通过铆钉转移升降气缸6184带动铆钉转移吸板6185将铆钉供料盘上的铆钉逐个吸取转移至铆钉供料衔接机构63上。
96.如图19所示,铆钉供料衔接机构63包括衔接旋转驱动组件631、衔接固定盘632和衔接旋转盘633;衔接旋转驱动组件631设置在机架上,衔接固定盘632设置在衔接旋转驱动组件631的固定部上;衔接旋转盘633设置在衔接旋转驱动组件631的旋转部上;衔接旋转盘633的外圈周向间隔排列设置有多个铆钉载具工位;每个铆钉载具工位上设置有铆钉载具台634;铆钉载具台634的顶部两侧分别设置有第一铆钉盛放部和第二铆钉盛放部;第一铆钉盛放部和第二铆钉盛放部结构相同,第一铆钉盛放部包括铆钉盛放槽635;铆钉盛放槽635的底面设置有铆钉阶梯孔636;通过铆钉供料衔接机构63便于将铜铆钉108和铝铆钉107同时分别盛放在第一铆钉盛放部和第二铆钉盛放部上,便于后续一次性将铜铆钉108和铝铆钉107同时组装至止动架106上。
97.如图20所示,铆钉二次定位检测机构64包括铆钉二次定位架641、铆钉二次定位旋转气缸642、铆钉二次定位板643;铆钉二次定位架641设置在机架上,铆钉二次定位旋转气缸642水平设置在铆钉二次定位架641上,铆钉二次定位板643固定连接在铆钉二次定位旋转气缸642的旋转部上,由于铆钉供料衔接机构63与铆钉二次定位架641的位置之间存在一定的角度,所以需要通过铆钉二次定位旋转气缸642带动铆钉二次定位板643进行转动调节。且铆钉二次定位架641的两侧分别设置有用于铆钉二次定位板643旋转限位的旋转限位板644;通过旋转限位板644能够防止铆钉二次定位板643转动过度。铆钉二次定位板643的两侧分别设置有的第一铆钉盛放部和第二铆钉盛放部;并使铜铆钉108和铝铆钉107分别在第一铆钉盛放部和第二铆钉盛放部进行检测,检测是否组装合格,组装不合格通过铆钉转移机构65直接将不合格的铆钉转移至铆钉废料盒内,组装合格通过铆钉转移机构65转移至工位载具10上的止动架106上。铆钉转移机构65的结构与正负极压板转移机构23结构相同。通过上述结构无需将铜铆钉108和铝铆钉107分开进行加工,直接一次性将铜铆钉108和铝铆钉107组装至止动架上,进一步提升了铆钉供料组装效率。
98.工作时,通过第一铆钉供料机构61上的铆钉顶料气缸6142带动铆钉顶料升降板6143上升至第一供料盘限位杆组6111的顶部,将一组装满铝铆钉107的铆钉供料盘放置在铆钉顶料升降板6143上,通过铆钉顶料升降板6143下降至低于铆钉供料支撑板613,从而使该组装满铝铆钉107的铆钉供料盘放置在铆钉供料支撑板613上,通过供料盘夹紧组件616上两侧的供料盘夹紧气缸6162带动l型夹紧块6163水平向内侧夹紧,插入至最底下一盘与
倒数第二盘之间空隙内,从而将倒数第二盘以上的铆钉供料盘进行限位防止下降,并对倒数第二盘以上的铆钉供料盘进行支撑,通过铆钉供料驱动组件612上的铆钉供料传输带6124带动铆钉供料支撑板613上的一盘装满铝铆钉107的铆钉供料盘移动至铆钉转移组件618下方,通过铆钉供料驱动组件612和铆钉转移组件618相配合,将铆钉供料盘的铝铆钉107逐一转移组装至铆钉供料衔接机构63的第一铆钉盛放部上,转移完成后将空的铆钉供料盘移动至第二供料盘限位杆组6112处,通过第二铆钉顶料组件615将铆钉供料支撑板613上空的铆钉供料盘顶起,使铆钉供料盘穿过供料空盘盛放转动板6174后,第二铆钉顶料组件615下降,使空的铆钉供料盘盛放在两侧的供料空盘盛放转动板6174上无法回至铆钉供料支撑板613上,从而进行下一盘铝铆钉107转移组装;将一组装满铜铆钉108以与铝铆钉107相同的方式在第二铆钉供料机构62上进行供料,并将铜铆钉108组装至铆钉供料衔接机构63上的第二铆钉盛放部上,将装有铜铆钉108和铝铆钉107的铆钉载具工位转移至铆钉二次定位检测机构64处,通过铆钉转移机构65直接一次性将铜铆钉108和铝铆钉107转移至二次定位检测机构64上,并进行检测,检测合格后,直接一次性将铜铆钉108和铝铆钉107转移组装至止动架106上。
99.如图1所示,铆接装置7包括铆接支架71、铆接驱动电机72和铆接冲压机构73;铆接驱动电机72和铆接冲压机构73分别设置在铆接支架71,且铆接驱动电机72驱动铆接冲压机构73进行铆接加工;下料装置8包括下料转移机构81和下料输送带机构82;下料输送带机构82的进料端衔接在下料转移机构81的下方。通过上述结构进一步提升铆接效率和下料效率。
100.一种电池盖板自动组装设备的使用方法,应用上述的电池盖板自动组装设备,包括以下步骤:
101.s1、正负极压板供料组装:通过正负极压板供料组装装置2将正极压板和负极压板一并供料组装至旋转盘装置1的工位载具10上,并通过旋转盘装置1将装有正极压板101和负极压板102的工位载具10旋转至弱导板和绝缘板供料组装装置3处;
102.s2、弱导板和绝缘板供料组装:弱导板和绝缘板供料组装装置3用于将弱导板103供料组装至工位载具10的正极压板101上;将绝缘板104供料组装至工位载具10的负极压板102上;弱导板和绝缘板组装后通过旋转盘装置1将该工位载具10旋转至检测工位通过检测组件19进行弱导板和绝缘板组装检测,检测无误后再旋转至基板供料组装装置4处;
103.s3、基板供料组装装置:基板供料组装装置4用于将基板105供料组装至工位载具10的弱导板103和绝缘板104上;并通过旋转盘装置1将装有基板的工位载具10旋转至止动架供料组装装置5处;
104.s4、止动架供料组装装置:止动架供料组装装置5用于将止动架106供料组装工位载具10的基板105上,并通过旋转盘装置1将该工位载具10旋转至检测工位通过检测组件19进行止动架106检测,检测无误后再旋转至铆钉供料组装装置6处;
105.s5、铆钉供料组装装置:铆钉供料组装装置6用于将铝铆钉107和铜铆钉108一并供料组装至工位载具10的止动架106上,并通过旋转盘装置1将该工位载具10旋转至检测工位通过检测组件19进行铆钉组装检测,检测无误后再旋转至铆接装置7处;
106.s6、铆接装置:铆接装置7用于将铝铆钉107和铜铆钉108一并进行冲压组装;从而使铝铆钉107和铜铆钉108将正负极压板、弱导板103、绝缘板104、基板105和止动架106组装
在一起,形成最终电池盖板的成品;通过旋转盘装置1将装有成品的工位载具10旋转至下料装置8等待下料;
107.s7、下料装置:电池盖板铆接完成后,通过下料装置8将成品转移下料。
108.综上所述,本发明的优点是该设备通过转盘式的结构能够大大节省占用空间,并且能够进一步提升电池盖板组装效率。
109.虽然本公开披露如上,但本公开的保护范围并非仅限于此。本领域技术人员,在不脱离本公开的精神和范围的前提下,可进行各种变更与修改,这些变更与修改均将落入本发明的保护范围。