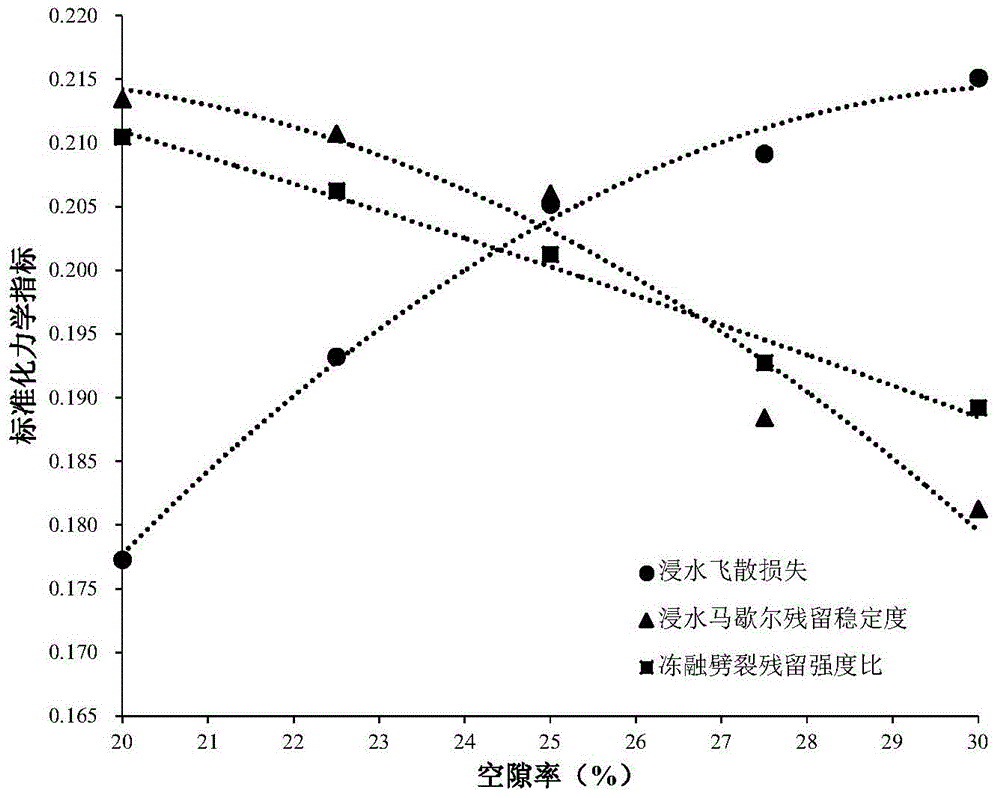
本发明属于道路工程
技术领域:
,具体涉及一种基于声力协同的聚氨酯高弹多孔混合料材料组成设计方法。
背景技术:
:聚氨酯高弹多孔混合料是由聚氨酯胶粘剂、橡胶颗粒和石料以一定比例组成的绿色功能型路面材料。该技术兼具胎路同质弹性减振和多孔吸声降噪两种特征,降噪功能相比常规多孔沥青路面、橡胶沥青路面等低噪音路面有大幅提升(降噪水平能提升约2db~7db),与隔音屏障相当,可大幅提升驾乘人员出行体验和沿线居民的生活品质。同时高分子聚氨酯胶粘剂的应用,相比常规沥青结合料,能更好的提高混合料的力学性能和长期耐久性。然而,聚氨酯高弹多孔混合料的降噪功能和力学行为存在矛盾、平衡和协同关系,如增加空隙率和橡胶颗粒掺量,会使降噪性能提升力学性能下降,反之则会使降噪性能下降力学性能提升。现有关于聚氨酯高弹多孔混合料组成设计的方法,通常针对特定路段重点提升混合料降噪性能,但未综合考虑级配、橡胶颗粒掺量等参数与聚氨酯高弹多孔混合料降噪、力学指标间的协同关系,缺乏系统科学的设计理论,难以构建出混合料组成设计和功能特性的联系,制约着聚氨酯高弹多孔混合料组成优化及综合性能提升。因此,目前行业内亟需提供一种基于声力协同的聚氨酯高弹多孔混合料材料组成设计方法。技术实现要素:针对以上问题,本发明基于高弹多孔混合料力学性能和降噪功能的矛盾、平衡、协同关系,提供一种基于声力协同的聚氨酯高弹多孔混合料材料组成设计方法,能够科学、系统、方便的开展聚氨酯高弹多孔混合料组成设计,并降低材料组成设计阶段的盲目性和工作量,为设计岀力学性能和降噪功能优异的聚氨酯高弹多孔路面结构奠定了基础。为实现上述目的,本发明的技术方案为:一种基于声力协同的聚氨酯高弹多孔混合料材料组成设计方法,其中聚氨酯高弹多孔混合料由聚氨酯胶粘剂、橡胶颗粒和矿料组成,该方法包括如下步骤:步骤一:选取影响声力学性能的材料组成参数,并制备聚氨酯高弹多孔混合料试件(1)矿料级配:目标空隙率20%-30%,设计n1组不同矿料级配;采用固定的聚氨酯胶粘剂用量,与不同矿料级配制备成混合料,测定各矿料级配对应的空隙率(vc);级配种类空隙率(%)级配1vc1级配2vc2级配3vc3………级配n1vcn1(2)橡胶颗粒掺量:n2组不同的橡胶颗粒掺量(n);(3)混合料制备:根据不同级配和橡胶颗粒掺量,制备聚氨酯高弹多孔混合料,其中,橡胶颗粒掺量等体积替换矿料级配中的细集料;步骤二:聚氨酯高弹多孔混合料声力学协同分析(1)采用固定的聚氨酯胶粘剂用量,将橡胶颗粒掺量等体积替换矿料级配中的细矿料,制备混合料试件,采用浸水飞散试验、浸水马歇尔试验和冻融劈裂试验,分别测试不同空隙率vc+固定橡胶颗粒掺量和不同橡胶颗粒掺量n+固定级配下聚氨酯高弹多孔混合料的浸水飞散损失r、浸水马歇尔残留稳定度ms和冻融劈裂残留强度比tsr,分别对各力学指标测试结果进行标准化去量纲处理,计算公式如下式所示,得到ri’、msi’、tsri’;然后采用二次函数拟合橡胶颗粒掺量n、空隙率vc和标准化处理后的三个力学指标的函数关系,如下式所示:则聚氨酯高弹多孔混合料力学综合评价指标f分别与橡胶颗粒掺量n、空隙率vc的函数关系如下式所示:(2)采用固定的聚氨酯胶粘剂用量,将橡胶颗粒掺量等体积替换矿料级配中的细矿料,制备混合料试件,采用驻波管法、轮胎下落噪声试验,分别测试不同空隙率vc、固定橡胶颗粒掺量和不同橡胶颗粒掺量n、固定级配下聚氨酯高弹多孔混合料的吸声系数a和噪声声级s,并根据噪声声级,基于下式计算降噪声级l,l=15-s分别对各声学指标测试结果进行标准化去量纲处理,得到ai’、li’;然后采用二次函数拟合橡胶颗粒掺量n、空隙率vc和标准化处理后的两个声学指标的函数关系,如下式所示:则聚氨酯高弹多孔混合料声学综合评价指标v分别与橡胶颗粒掺量n、空隙率vc的函数关系如下式所示:(3)根据(1)、(2)中的不同空隙率及橡胶颗粒掺量条件下获得的力学指标f及声学指标v,并基于声力学协同理念,结合实际工程对路面力学、声学性能的需求,提出聚氨酯高弹多孔混合料力学综合评价指标和声学综合评价的权重,并提出声-力学协同指标m,公式如下:其中,ω1、ω2分别为力学综合评价指标和声学综合评价指标对应权重值,其中ω1+ω2=1,且ω1、ω2<1,在满足规范要求的力学性能前提下,通过分析声-力学协同指标m的最大值,确定混合料矿料级配/空隙率及橡胶颗粒掺量;步骤三:高弹多孔混合料聚氨酯用量确定以步骤二中确定的矿料级配、橡胶颗粒掺量,和不同的聚氨酯胶粘剂用量m制备混合料,通过浸水飞散试验拐点确定聚氨酯胶粘剂最小用量,析漏试验拐点确定最大用量,聚氨酯胶粘剂最小用量与最大用量的平均值即为最佳的聚氨酯用量。所述固定的橡胶颗粒掺量为30%;固定的聚氨酯胶粘剂用量为5%,所述固定级配所对应的孔隙率为20%。所述矿料采用玄武岩集料,采用废旧轮胎制备的橡胶颗粒按相应橡胶颗粒掺量等体积由小至大替换粒径1.18mm~9.5mm细集料。所述不同矿料级配为五组矿料级配;所述橡胶颗粒掺量n为20%,25%,30%,35%,40%五组掺量。所述确定混合料矿料级配/空隙率的方法为:根据分析声-力学协同指标m的最大值得到的空隙率值,与步骤一中测定的n1组矿料级配中的某一组级配的空隙率值vc相同,则选定该组矿料级配;或者根据分析声-力学协同指标m的最大值得到的空隙率值与步骤一中测定的n1组矿料级配中的某一组级配的空隙率值vc最接近,则在该组矿料级配上调整得到新的矿料级配,以新的矿料级配、固定的聚氨酯用量、根据分析声-力学协同指标m的最大值得到的橡胶颗粒掺量组合制备混合料,再次测定新的矿料级配的空隙率,直到该测定的新的矿料级配的空隙率与根据分析声-力学协同指标m的最大值得到的空隙率值相同;则选定该新的矿料级配。所述不同的聚氨酯胶粘剂用量m以5%为中值,按0.5%的相邻间隔变化。所述不同的聚氨酯胶粘剂用量m分别为4%,4.5%,5%,5.5%,6%。聚氨酯胶粘剂采用单组份聚氨酯或双组份聚氨酯胶粘剂。详细方法步骤如下:步骤一:选取影响声力学性能的材料组成参数,并制备聚氨酯高弹多孔混合料试件(1)矿料级配:不同级配的混合料空隙率不同,即采用空隙率指标能较好的表征混合料的级配特点,而聚氨酯高弹多孔混合料的级配对其力学、声学性能均有较为显著的影响,选取n1种聚氨酯高弹多孔混合料级配(纯石料级配),并测试其空隙率,如下表所示:表1不同级配聚氨酯高弹多孔混合料的空隙率级配种类空隙率(%)级配1vc1级配2vc2级配3vc3………级配n1vcn1(2)橡胶颗粒掺量:聚氨酯高弹多孔混合料中橡胶颗粒的含量越高,其声学性能越优异,而力学性能则会发生衰减,选取n2组不同的橡胶颗粒掺量,如下表所示:表2聚氨酯高弹多孔混合料橡胶颗粒掺量橡胶颗粒掺量(%)n1n2n3…nn2(3)混合料制备:根据不同级配和橡胶颗粒掺量,制备聚氨酯高弹多孔混合料,其中,石料采用玄武岩集料,粒径在1.18mm~9.5mm范围内的集料采用废旧轮胎制备的橡胶颗粒,聚氨酯胶粘剂采用单组份聚氨酯或双组份聚氨酯胶粘剂。步骤二:聚氨酯高弹多孔混合料声力学协同分析(1)采用浸水飞散试验、浸水马歇尔试验和冻融劈裂试验,分别测试不同空隙率vc+固定橡胶颗粒掺量和不同橡胶颗粒掺量n+固定级配下聚氨酯高弹多孔混合料的浸水飞散损失(r)、浸水马歇尔残留稳定度(ms)和冻融劈裂残留强度比(tsr),分别对各力学指标测试结果进行标准化去量纲处理(计算公式如下式所示),得到ri’、msi’、tsri’。然后采用二次函数拟合橡胶颗粒掺量(n)、空隙率(vc)和标准化处理后的三个力学指标的函数关系,如下式所示。则聚氨酯高弹多孔混合料力学综合评价指标(f)和橡胶颗粒掺量(n)、空隙率(vc)的函数关系如下式所示。(2)采用驻波管法、轮胎下落噪声试验,分别测试不同空隙率vc+固定橡胶颗粒掺量和不同橡胶颗粒掺量n+固定级配下混合料的吸声系数(a)和噪声声级(s),并根据噪声声级,基于下式计算降噪声级(l)。l=15-s分别对各声学指标测试结果进行标准化去量纲处理,得到ai’、li’;然后采用二次函数拟合橡胶颗粒掺量(n)、空隙率(vc)和标准化处理后的两个声学指标的函数关系,如下式所示。则聚氨酯高弹多孔混合料声学综合评价指标(v)和橡胶颗粒掺量(n)的函数关系如下式所示。(3)根据(1)、(2)中的不同空隙率及橡胶颗粒掺量条件下获得的力学指标f及声学指标v,并基于声力学协同理念,结合实际工程对路面力学、声学性能的要求,提出聚氨酯高弹多孔混合料力学综合评价指标和声学综合评价的权重,提出声-力学协同指标m,公式如下:其中,ω1、ω2分别为力学综合评价指标和声学综合评价指标对应权重值,并根据实际道路应用场景,结合其力学性能和降噪功能需求,综合判定聚氨酯高弹多孔混合料力学综合评价指标与声学综合评价指标的权重值,其中ω1+ω2=1,且ω1、ω2<1。在满足规范要求的力学性能前提下,通过分析声-力学协同指标m的最大值,优选混合料级配/空隙率及橡胶颗粒掺量。步骤三:高弹多孔混合料聚氨酯用量确定以步骤二中确定的矿料级配、橡胶颗粒掺量,和5%的用胶量为中间值,按0.5%的相邻间隔变化制备多组混合料,通过浸水飞散试验的浸水飞散损失拐点确定聚氨酯胶粘剂最小用量,析漏试验的析漏损失拐点确定最大用量,聚氨酯胶粘剂最小用量与最大用量的平均值即为最佳的聚氨酯用量。本发明提供一种基于声力协同的聚氨酯高弹多孔混合料材料组成设计方法,可协同考虑混合料的力学性能和降噪功能,使二者实现平衡最优的路用效果,显著提高路面工程品质,且该方法易操作,能够降低聚氨酯混合料组成设计阶段的盲目性和工作量。附图说明图1空隙率-标准化力学指标曲线图2橡胶颗粒掺量-标准化力学指标曲线图3空隙率-标准化声学指标曲线图4橡胶颗粒掺量-标准化声学指标曲线图5用胶量-浸水飞散损失率曲线(实施例1)图6用胶量-析漏损失率曲线(实施例1)图7用胶量-浸水飞散损失率曲线(实施例2)图8用胶量-析漏损失率曲线(实施例2)具体实施方式以下实施例用于说明本发明,但不用来限制本发明的范围。本发明提供了一种基于声力协同的聚氨酯高弹多孔混合料材料组成设计方法,并不仅仅限于方案阐述中所描述的方法。故凡依据本专利所述的模型及原理所做的等效变化或修饰,均应包括与本专利申请范围内。实施例1:根据本发明提出的材料组成设计方法,开展聚氨酯超弹多孔混合料组成设计。1、矿料级配为了保证高弹多孔路面优异的降噪功能和排水性能,其目标空隙率范围要求在20%-30%,本实施例选取目标空隙率为25%,设计5组不同级配,结果如下表所示。表3各级配筛孔通过率结果筛孔尺寸(mm)1613.29.54.752.361.18级配1100977526170级配2100957225110级配310095701880级配410094671580级配510093691570级配范围(%)10090~10055~7515~267~200粗集料采用玄武岩碎石,细集料选用石灰岩,选择2,6-tdi型聚氨酯胶黏剂,初步采用聚氨酯胶粘剂的用量为5%,制备完成混合料试件后放置于恒温恒湿箱中养生,试样养生环境条件为温度30℃、湿度70%,养生时间为48h。养生完成后测试混合料的空隙率,结果如下表所示。表4各级配混合料空隙率测试结果级配类型级配1级配2级配3级配4级配5空隙率(%)2022.52527.5302、橡胶颗粒掺量为了确保其聚氨酯高弹多孔混合料其声学性能越优异,且保证力学性能衰减适宜,则选取5组不同的橡胶颗粒掺量,在步骤2确定矿料级配的基础上,橡胶颗粒掺量选取20%±1%、25%±1%、30%±1%、35%±1%、40%±1%五个水平,基于等体积替换法替换不同粒径的集料,将橡胶颗粒、石料拌和后加入聚氨酯胶粘剂制备混合料成型试件。3、混合料制备粗集料采用玄武岩碎石,细集料选用石灰岩,橡胶颗粒选用废旧轮胎橡胶,由轮胎胎侧在常温下加工粉碎而成,其成分为70%的丁苯橡胶和30%的天然橡胶,选择2,6-tdi型聚氨酯胶黏剂,初步采用聚氨酯胶粘剂的用量为5%,上述橡胶颗粒掺量制备完成混合料试件后放置于恒温恒湿箱中养生,试样养生环境条件为温度30℃、湿度70%,养生时间为48h。养生完成后测试下述性能指标。4、不同橡胶颗粒掺量和空隙率下混合料的力学性能测试针对步骤2、步骤3中制备的不同级配(橡胶颗粒掺量固定为30%)及不同橡胶颗粒掺量(固定为级配1)、初步采用聚氨酯胶粘剂的用量5%的混合料试件,分别测试其氨酯高弹多孔混合料的浸水飞散损失(r)、浸水马歇尔残留稳定度(ms)和冻融劈裂残留强度比(tsr),结果如表5、表6所示。表5不同级配(空隙率)下混合料的力学性能试验结果表6不同橡胶颗粒掺量下混合料的力学性能试验结果根据上述数据,对不同级配及橡胶颗粒掺量的聚氨酯高弹多孔混合料的浸水飞散损失(r)、浸水马歇尔残留稳定度(ms)和冻融劈裂残留强度比(tsr)测试结果进行标准化去量纲处理,得到r’、ms’、tsr’,如表7、表8所示;表7不同级配(空隙率)下混合料的力学性能试验结果标准化值表8不同橡胶颗粒掺量下混合料的力学性能试验结果标准化值根据表7、表8数据,分别绘制空隙率-标准化力学指标曲线和橡胶颗粒掺量-标准化力学指标曲线,如图1、图2所示。同时,采用二次函数分别拟合上述表7、表8数据,得到橡胶颗粒掺量(n)、空隙率(vc)和标准化处理后力学指标的函数关系,如下表所示。表9橡胶颗粒掺量(n)、空隙率(vc)和标准化处理后力学指标的函数关系标准化力学指标函数关系相关系数浸水飞散损失(r’)r’=-0.0003vc2+0.0196vc-0.0869r2=0.993浸水马歇尔残留稳定度(ms’)ms’=-0.0002vc2+0.009vc+0.1341r2=0.9608冻融劈裂残留强度比(tsr’)tsr’=-2e-05vc2-0.001vc+0.2411r2=0.9842浸水飞散损失(r’)r’=-0.0001n2-0.0031n+0.3951r2=0.9955浸水马歇尔残留稳定度(ms’)ms’=-0.0001n2+0.0102n+0.0177r2=0.9978冻融劈裂残留强度比(tsr’)tsr’=-2e-05n2+0.0031n+0.129r2=0.9884则聚氨酯高弹多孔混合料力学综合评价指标(f)和橡胶颗粒掺量(n)的函数关系如下式所示。5、不同橡胶颗粒掺量和空隙率下混合料的声学性能测试针对步骤2、步骤3中制备的不同级配(橡胶颗粒掺量固定为30%)及不同橡胶颗粒掺量(固定为级配1)的混合料试件,分别测试其氨酯高弹多孔混合料的吸声系数(a)和噪声声级(s),并根据噪声声级计算降噪声级(l),结果如表10、表11所示。表10不同级配(空隙率)下混合料的声学性能试验结果表11不同橡胶颗粒掺量下混合料的声学性能试验结果根据上述数据,对不同级配及橡胶颗粒掺量的聚氨酯高弹多孔混合料的吸声系数(a)和降噪声级(l)测试结果进行标准化去量纲处理,得到a’、l’,如表12、表13所示;表12不同级配(空隙率)下混合料的声学性能试验结果标准化值表13不同橡胶颗粒掺量下混合料的声学性能试验结果标准化值根据表12、表13数据,分别绘制空隙率-标准化声学指标曲线和橡胶颗粒掺量-标准化声学指标曲线,如图3、图4所示。同时,采用二次函数分别拟合上述表12、表13数据,得到橡胶颗粒掺量(n)、空隙率(vc)和标准化处理后声学指标的函数关系,如下表所示。表14橡胶颗粒掺量(n)、空隙率(vc)和标准化处理后声学指标的函数关系标准化力学指标函数关系相关系数吸声系数(a’)a’=-0.0006vc2+0.0307vc-0.4056r2=0.9479降噪声级(l’,db)l’=-0.0004vc2+0.0233vc-0.1571r2=0.9848吸声系数(a’)a’=-0.0001n2+0.0016n-0.0851r2=0.9293降噪声级(l’,db)l’=-0.00014n2+0.0127n-0.224r2=0.9189则聚氨酯高弹多孔混合料声学综合评价指标(v)和橡胶颗粒掺量(n)的函数关系如下式所示。6、聚氨酯高弹多孔混合料声力学协同分析以北京市某城市路段为对象,结合该路段具体荷载作用工况及周边环境降噪需求,综合判定聚氨酯高弹多孔混合料力学综合评价指标和声学综合评价指标的权重均为0.5。根据不同空隙率及橡胶颗粒掺量条件下获得的力学指标f及声学指标v,并基于声力学协同理念,提出声-力学协同指标m,公式如下:由上式可以看出,当橡胶颗粒掺量为27%、空隙率为27%时,聚氨酯高弹多孔路面的声力学协同效果达到最优。7、以上步中确定的最优空隙率及橡胶颗粒掺量,结合技术人员经验,在级配4(空隙率为27.5%)的基础上,通过调高2.36mm筛孔的通过率,来增加级配中细集料的比例(如下表所示),进而使空隙率降低至27%,并得到最优级配。表15最优级配的筛孔通过率筛孔尺寸(mm)1613.29.54.752.361.18级配410094671590以5%的用胶量为中间值,按0.5%的用胶量间隔制备5组不同用胶量的马歇尔试件;按0.5%的用胶量间隔设计5组不同用胶量的析漏试验所用混合料;通过浸水飞散试验和析漏试验测试聚氨酯高弹多孔混合料的浸水飞散损失和析漏损失,结果分别如图5、图6所示。析漏损失率-用胶量曲线交点处的用胶量为4.68%,浸水飞散损失率-用胶量曲线交点处的用胶量为4.71%。因此根据四舍五入的原则,保留最佳用胶量小数点后一位,得到最佳用胶量为4.7%。8、路用性能验证按上述得到的聚氨酯混合料组成制备试件,开展渗水系数试验、车辙试验、低温小梁弯曲试验,分别评价聚氨酯混合料的渗水性能、高温稳定性、低温抗裂性。试验结果见下表。表16路用性能验证试验结果路用性能试验试验结果指标要求渗水系数试验(ml/min)6800≥5000动稳定度ds(次/mm)22500≥5000弯曲劲度模量(mpa)114——最大弯曲应变37500≥3000通过试验结果可知,聚氨酯高弹多孔混合料具有良好的高低温性能、水稳定性能和抗剥落性能,满足现行规范对路用性能的要求。实施例21、采用类似实施例1的聚氨酯高弹多孔混合料材料组成设计方法,区别仅在于:所述聚氨酯高弹多孔混合料力学综合评价指标和声学综合评价指标的权重,为以上海市某城市路段为对象,结合该路段具体荷载作用工况及周边环境降噪需求,综合判定聚氨酯高弹多孔混合料力学综合评价指标和声学综合评价指标分别为0.2和0.8。根据不同空隙率及橡胶颗粒掺量条件下获得的力学指标f及声学指标v,并基于声力学协同理念,提出声-力学协同指标m,公式如下:由上式可以看出,当橡胶颗粒掺量为29%、空隙率为27%时,聚氨酯高弹多孔路面的声力学协同效果达到最优。2、以上步中确定的最优空隙率及橡胶颗粒掺量,结合技术人员经验,在级配4(空隙率为27.5%)的基础上,通过调高2.36mm筛孔的通过率,来增加级配中细集料的比例(如下表所示),进而使空隙率降低至27%,并得到最优级配。表15最优级配的筛孔通过率筛孔尺寸(mm)1613.29.54.752.361.18级配410094671590以5%的用胶量为中间值,按0.5%的用胶量间隔制备5组不同用胶量的马歇尔试件;按0.5%的用胶量间隔设计5组不同用胶量的析漏试验所用混合料;通过浸水飞散试验和析漏试验测试聚氨酯高弹多孔混合料的浸水飞散损失和析漏损失,结果分别如图7、图8所示。析漏损失率-用胶量曲线交点处的用胶量为4.64%,浸水飞散损失率-用胶量曲线交点处的用胶量为4.89%。因此根据四舍五入的原则,保留最佳用胶量小数点后一位,得到最佳用胶量为4.8%。8、路用性能验证按上述得到的聚氨酯混合料组成制备试件,开展渗水系数试验、车辙试验、低温小梁弯曲试验,分别评价聚氨酯混合料的渗水性能、高温稳定性、低温抗裂性。试验结果见下表。表16路用性能验证试验结果通过试验结果可知,聚氨酯高弹多孔混合料具有良好的高低温性能、水稳定性能和抗剥落性能,满足现行规范对路用性能的要求。当前第1页12