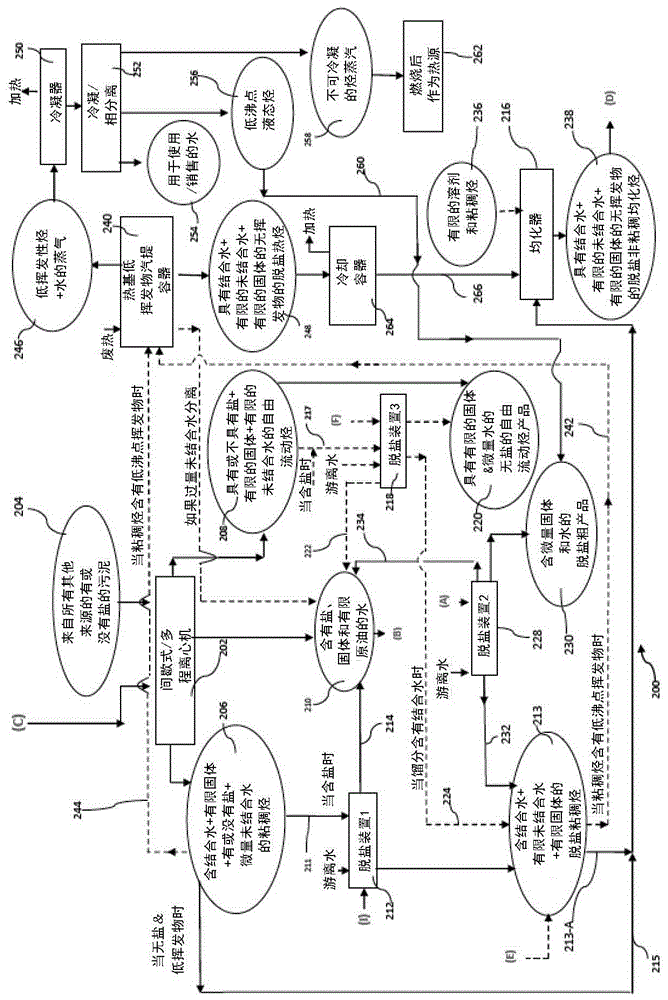
本发明涉及石油/粗污泥、乳状液和废油的处理方法。更具体地说,本发明涉及一种从包含烃、结合水、非结合水、溶解和不溶解固体的石油/粗污泥、乳状液和废油中除去结合水和非结合水的方法,以将其变成不同纯度的可售流体,特别地,该方法不局限于石油工业。
背景技术:石油原油从油井中出来,总是具有水、溶解和不溶解的固体和部分含有结合水和非结合水的含硫化合物。该石油原油之后在石油企业的集团收集中心(下文称GCC)处理,其中,首先,石油原油脱硫,然后除去非结合水以及不溶解的固体。然而,GCC不能除去结合水和溶解固体,除非在使用破乳剂的情况下。据推测,因为原油脱盐导致了额外形成具有结合水的乳状液,因此具有结合水的原油被运送至油井。在将原油送至炼油厂之前,特别要求GCC从原油中除去硫及大部分不溶解固体,并除去全部的水,以降低原油含油污水含量至低于5000ppm。除去水的方法主要包括使原油沉降在沉降池中,其中形成了顶层、中间层和底层。顶层包含纯原油,它们将被运送至炼油厂进行进一步的处理。中间层包括含水乳状液,其将被运送其至槽,在那里对其加热,经受高电压振荡电场,并任选使用破乳剂,其中的目的是以最短的时间除去最多的水。底层通常包含具有不溶解固体的含油污水,其被称为废油。作为一种污染物,通常通过管线将废油运送至废弃的油井中存储。在炼油厂,原油的生产、运输、储存和炼制大多数会制造污泥。污泥通常是一种油、水和固体紧密保持黏性的乳状液,其中固体含量可以宽泛地变化。每当油和水混合并搅拌时,就形成了污泥。在炼油厂,污泥也形成在脱盐设备中,其中用清水清洗原油以除去碱,其已经浸入海水。此外,污泥产生在氢化裂解装置、原油储罐、废油和API分离装置等中。通常情况下,每吨原油产生1.6kg污泥。按照1992年美国环保局的报告,通过大型炼油厂,每年每个大炼油厂不可避免地产生大约30,000吨油泥废流。超过80%的污泥属于环保局危险废物号F037和F038。在印度,每年产生超过2.62亿吨(lactonnes)污泥。当通过传送泵剧烈搅拌/剪切原油中的水时,污泥也会形成。由于污泥比轻油重,它很容易沉淀在船舶荷载的底部,当在炼油厂泵出原油时,需要从船舶中除去。除此之外,还具有槽污泥,其是固体层,随着时间积聚在船舶底部,并每5年左右除去一次。通常,60-M槽排出10亿吨(1,000MT)材料。该材料的约85%至90%形成重烃,像石蜡、沥青、微晶蜡等。通常,使用高压水喷射除去这种材料。污泥也产生在后期炼油操作中。当重质液体燃料如LSHS或高炉燃油通过低速DG组件用于发电时,形成了0.5wt%~1wt%的污泥。这些DG组件既可以基于陆地也可以基于海洋。污泥也产生于废油再生工厂中。污泥的形成是全世界的一个大问题。例如,德士古(2001年被雪佛龙收购),在1964年至1990年的钻井作业后,将七百亿升有毒石油污泥池遗弃在厄瓜多尔亚马逊雨林,而没有任何的补救措施。这种污泥本身来自钻井作业,而不是来自生产。雪佛龙拥有处理污泥的专利技术,如美国专利号4,689,155中公开的。然而,污泥仍然被倒入当地人赖以饮用、洗澡和钓鱼的小溪和河流中。人们已经挖掘了超过900个露天的、未覆盖的废坑,这些废坑仍然渗漏毒素到地下。这种污泥含有像苯和多环芳烃的化学品。更糟糕的是,这种倾倒是有意为之的,为了简单行事并节约成本(每桶油节省大约3美元)。该公司节省了13.2亿美元,但它导致了30,000厄瓜多尔人受苦,他们中的1400人死亡。到2080年,这可能会导致10,000以上的死亡人数。以厄瓜多尔热带雨林的东部地区为例,这里曾经供养30,000人,但土地本身已经成为有毒的,且水系统也被污染。几乎任何一种来自这个地区的食物都是不安全的食品,无论是人工养殖、驯化的、野外捕获的或是在水中的食物。当地经济和社区已经崩溃。十八年前,当地人提起集体诉讼。损害赔偿被评估为273亿美元,当地人赢得了诉讼,雪佛龙公司被要求支付180亿美元。雪佛龙没有为这一环境灾难承担责任并进行偿付,而是拒绝支付,并展开前所未有的公关和游说活动,以避免不得不收拾残局。以PDVSA为例,委内瑞拉国营石油公司。1999年8月,它在环境责任上被处以15亿美元。除其他事项外,其被要求清理含有来自油井的受污染的污泥的15,000个油坑。仅凭这一点就花费了公司十亿美元。迫于来自法庭的压力,传统上忽视环境的该公司目前已经开始清理行动并承诺将环保作为其最高目标。以俄罗斯为例,其每年产生超过300万吨的石油污泥,超过33%的污泥来自油井。俄罗斯石油和天然气工业是该国工业废物积累的第三大贡献者。俄罗斯拥有7,000个废弃的油井。它拥有416,000公里的输油管线,输油管线经常因腐蚀而损坏。每年俄罗斯面临50,000至60,000起管线相关事故,导致1500万吨石油在自动阻流机制得到激活之前泄漏。约30%流入河流和湖泊,即每年400至500万吨。1994年,仅在科米,一次管线相关事故,就泄漏了10万吨石油。1993年在塔岗(Tyagan)的秋明地区,一次管线相关事故导致了42万吨石油泄漏。俄罗斯拥有容纳百万吨污泥的泻湖。西西伯利亚拥有超过300万吨污水。鞑靼斯坦拥有超过250万吨污水。巴什科尔托斯坦拥有700个泻湖,具有200万吨污泥。由于土地便宜,在泻湖中污泥的存储根据位置每吨花费20至40美元。它们燃烧了大部分污泥,造成广泛的空气污染。俄罗斯拥有总产能为30,000万吨的27个炼油厂。在萨拉托夫炼油厂,泻湖覆盖超过150公顷。其地下水中的油含量为每升7.2克。仅美国公司目前在俄罗斯提供污泥处理服务,价值每年超过9,000万美元。俄罗斯支付28至360美元以处理一吨污泥,而这取决于该地区离城市多远和使用的技术和设备的种类。俄罗斯用外国零部件定制的常规污泥处理系统的成本在500万美元以上。这些大多数是基于沉降槽、离心机和滗析器的破乳装置。在驳船和泵中使用从其中脱脂的油。他们还利用生物修复和焚烧炉。合并使用破乳与生物修复,他们每吨支付160至200美元。对于像超声处理的创新技术,他们每吨支付300美元。由于污泥很难处理掉,直到最近,炼油厂都将污泥倾倒在槽、水池和泻湖中。大多数在发展中和欠发达国家的炼油厂即使到今日仍然如此。通常,这种泻湖占地面积为4公顷,并且含有12至16万吨污泥。其中多个泻湖自1896年就含有污泥。在这种老泻湖中的污泥被称为“风化泥”,随着时间的增加,它们往往会均质化。在发达国家如美国,禁止在水池或泻湖中再存储污泥,除非它们衬有非渗透性材料。即使这样也是被强烈反对的。那是因为对周围的土壤和地下水有不利影响。挥发物的蒸发也会产生过于强烈的气味和空气污染。1980年,美国国会颁布了《综合环境反应、赔偿与责任法案》。这产生了一种化工及石油营业税,由此筹集的资金进入称为超级基金的大型信托。那笔资金用于支付所有危险废物处理和漏油点的清理,像石油污泥泻湖。1995年行业税过期。但是超级基金计划继续进行。现在,资金是从一般税收收入拨款资助它。美国环保局负责该基金与各个州的合作。最近,污泥池和泻湖的清理已经成为一种利润丰厚的商业业务。炼油厂热衷于从污泥中回收油。即便这是不可能的,他们也热衷于提取它的能量。当即便那样也不可能时,他们试图以最低成本将其转化为无害物质。在本领域可以看到使用多种技术清理污泥的各种尝试。现有技术中可以见到破乳剂/化合物的使用,以用于破碎污泥。例如,NormanKevin,ElkPoint的中国专利文献CN101786776,公开了一种深度处理工艺,其中将含油污泥引入调节池,然后通入热水,随后搅拌,提高含油污泥的流动性。进一步在旋流脱盐设备中处理污泥并送入到调质罐中,在那里加入预定量的破乳剂,然后在合适的温度下破乳。此外,BaxaJ的名称为“Oildehydrationanddesalting-byaddingdistillationslopsandde-emulsifyingvacuumdistillation”的捷克斯洛伐克专利文件CS8702260-A也公开了破乳剂的使用。史密斯和勒芙莱斯公司(M/s.Smith&LovelessInc.)用化学品和曝气处理炼油污泥。来自荷兰的莱恩技术石化公司(M/s.LenntechPetrochemicalCompany)使用化学品、溶剂萃取、膜、过滤、浮选、絮凝、反渗透等回收油。乌克兰美国合资企业油回收公司(M/s.ReverseOil)自1996年以来使用大量化学品清除“Ukrtatnafta”污泥池,仅仅是为了尽量减少对环境的不利影响。然而,使用化学品或破乳剂破碎污泥并不总是100%对分离起作用。此外,破乳剂的使用不宜在炼油厂内继续使用,除非回收的油主要不含水。另外,现有技术中也可见到用溶剂加热污泥的技术,优选使用共沸溶剂混合物。例如,BereznikovAnatoli的德国专利文献DE19936474提供了含油污泥的分离,是通过用溶剂加热并回收溶剂产生的,使用溶剂(例如甲苯)形成了一种具有水性组分的多相共沸混合物。稳步混合混合物得到浆料,然后将其加热至其沸点。冷凝饱和蒸汽,除去水性组分和固体残余物,持续这样以通过控制温度上升完成水分离。此外,RichterGedeonVegyeszet的西班牙专利文献ES2047129T3公开了采用共沸蒸馏的脱水工艺,更具体地,它涉及一种使用连续共沸蒸馏使物质或混合物(主要是冷凝反应的混合物)剧烈脱水的工艺(例如,直接酯化、直接乙缩醛形成、直接缩酮形成)。此外,DynamitNobelAg的美国专利文献US3669847A公开了一种用于从工业工艺废水中分离蒸汽挥发性有机溶剂的工艺。其中通过将工艺废水与蒸汽充分混合,从工艺废水中除去蒸汽挥发性有机溶剂,以形成共沸蒸汽混合物,从所得的蒸汽和水混合物中回收共沸蒸汽混合物,并冷凝所述共沸蒸汽混合物。像M/s.CEVA国际公司和M/s.E&I技术公司等公司通过离心污泥回收油。与M/S.石油废物服务公司(Petro-WasteServicesInc.)(PWS)的协作中,CEVA提供了2种尺寸的设备。一种每天处理200吨污泥,而另外一种每天处理475吨污泥。其中一些是移动设备。通常,当不可能分解污泥的时候,炼油厂就焚烧污泥。由于含水量高,经常用补充液体燃料支持燃烧。M/s.W.N.Best公司制造了焚烧系统,用于每小时处理0.38至26.5吨石油污泥。许多现代炼油厂将其污泥倾倒在焦化厂,在那里回收部分燃料。因此,他们不产生污泥。通过不生成污泥预防污染被认为是最有益的。他们创造了所谓的石油焦。然而,焦炉厂产生高硫含量。然而,生物修复是主要趋势。这里污泥与土壤均匀混合,使得其总烃含量限制在约3wt%。然后土壤中天然存在的细菌经过几年的时间将烃降解为二氧化碳和水。为了加速这一过程,人们增加了空气,湿气和养分的供给到土壤中。为了增加养分,提供氮和磷基肥料。一定密度和品种的细菌也有帮助。有了所有这些,人们试图在一年内实现土壤中烃的显著减少。这个过程也被称为“土地农业”,由于人们把污泥掺入土地,以期通过细菌作用的缓慢过程实现污泥最终处理。生物堆积法是在这一领域中的进一步改进,在其中,均质污泥和土壤混合物连同木屑一起置于天然粘土防渗基层上,以增强渗透性。将多孔管连接至风机或真空泵,以曝气堆积层。为了均匀加入水和养分,纳入渗滤液收集系统。在全球范围内,M/s.Biogenie公司,M/s.EnvirosoilServices有限公司和M/s.WillacyOilServices有限公司都活跃在这一领域。Envirosoil的LTTD工艺用工厂中的污泥处理土壤,一旦土壤中烃含量降至低于15ppm的可接受水平,则将土壤转移到土地上。Willacy在中东和土耳其非常活跃。在印度,M/s.TataEnergyResearchInstitute(TERI)公司用了七年时间发展“Oilzapper”。那是一种从5种细菌中培养的有效菌群,分离,并固定在粉状玉米芯上。它可以在一年之内有效降解基于油的烃。这种技术诀窍已被转移至海得拉巴的M/S.施拉姆生物科技有限公司和孟买的M/S.巴拉特石油公司有限公司。Oilzapper在过去两年内已经在印度成功降解了超过10,000吨石油污泥。在全球范围内,每吨污泥的生物修复成本在73至641美元。然而,即使是生物修复技术也具有一定的局限性。首先,生物修复过程导致了全部有价值烃的损失,这是人们非常不期望的。第二,生物修复过程费用高,并且了在垃圾处理过程上消耗大量时间。此外,由于生物修复处理后得到的产品是无用的,修复后得到的产品不能变废为宝。另一个致命的污染物是废油,其通常是含有固体和盐的含油污水。在将废油运送至炼油厂之前,这种水在集团收集中心(GGC)进行处理。废油也产生于炼油厂,其中为了脱盐,在原油中加入淡水,并使用与GCC相同的设备除去废油,从而增加了不必要的成本。此外,除了污染废油的产生,在这个过程中损失了大量的烃。这种作为污染物的水通常返回进行存储,其中除了增加运输成本,用于通过管线排出海水中的腐蚀性水之外,存储的腐蚀性水可能泄露。废油对环境也有很大的影响,它会污染海水,从而影响海洋生物。此外,虽然废油是油和水的一种宝贵资源,但是其是一种经常被忽视的主要资源。例如,俄罗斯具有超过4,16,000公里的管线,其经常因腐蚀而受损,造成50-60,000例管线有关的事故,从而导致数百万吨石油在自动阻流机制得到激活之前泄漏。大约30%的油进入河流和湖泊,从而产生了废油。1993年,在塔岗(Tyagan)的秋明地区,单根管线相关事故导致了42万吨石油的泄漏。1994年,仅在科米,单管线泄漏,就泄漏了10万吨石油。废油甚至来自于油污设备的清理,包括石油运输船的清理。即使在除了石油行业以外的行业,油用作冷却剂或用于润滑的行业也产生了废油。常规离心技术用于废油的处理。例如,MeikenBernard的题为“Recoveryofwater,gasoline,heavyoils,andsolidsfromslopoilsoroilemulsions”的德国专利文献DE4205885,公开了用于废油/乳状液离心的两相滗析器的使用,其中在由加热器、塔和泵形成的加热电路中加热废油至105℃至135℃。然后从塔的顶部抽出气体和蒸汽,并且从该塔的底部,取出加热的废油液,冷却,并在两相滗析器中分离为离心的清洁油相和固相。此外,俄罗斯的专利文献RU2217476教导了含油矿泥提炼和从其中提取烃用于炼制液体和膏状油性矿泥的工艺,特别是海底沉淀物,抗油-水乳剂,含有少量机械杂质的中间层。该方法包括用石油稀释油性矿泥,加热,并在三相沉降式离心机中分离石油,水和机械杂质的浓缩物。在蒸馏塔中将残留的水与轻油馏分与石油分离。另外,中国纳特石油公司的中国专利文献CN100582031,公开了一种处理和使用油场含油污泥浆的工艺。该发明涉及油泥的处理和使用方法,其中经由次级提升泵的卧式离心机用于脱水。脱水后的水在离心机操作后进入接下来的污水处理系统的液体管线。然而,离心机技术并非没有限制。通常有两种类型的离心机串联使用,即滗析器和碟片式离心机。碟片式离心机具有较高G的优势,但当废油中含有较多量的固体时,它是低效的。滗析器增强密度差,但却在处理重质原油/超重质原油污染的水情况下失效,这些污染的水的油密度等于水密度。离心机增强了浮力,但缩短了停留时间,因为只有当粒径更大且阻力较小时,离心机才是有效的。此外,油颗粒的表面电荷会防止油颗粒聚集和聚结在一起。此外,该离心机可以处理超细颗粒,除非分布密度很大。然而,当分布密度落在一个特定水平以下时,平均自由路径增加了很多,使得液滴聚结难以在允许的停留时间内发生。主要的事实是,只有当存在聚集的时候,该离心机才可分离。因此,当废油含有细油滴时或其中含有固体和结合水的高度粘稠油滴时,离心机技术实质上难以按预期那样工作。可选择地,现有技术中也可看到对于污泥处理使用了过滤技术。例如,Amsted实业公司的加拿大专利文献CA1202223,公开了一种包含重力分离器的深床型过滤器。搅动该床,并去除包裹在滤床中的油。其中,在水中的油是异常黏性的,或具有蜡状,柏油状或粘稠度的,例如,在过滤之前通过加入少量的溶剂化物液体到油-水混合物中增强了滤床的活性。此外,BeavonDK的GB1340931教导了一种用于也含有油性颗粒固体的油-水混合物的处理方法,通过将其通过颗粒过滤介质对其处理,以除去颗粒固体,其中所得滤液是水或水和油的混合物。接下来是在与油-水混合物相同的方向上通过传递脱油介质穿过该床,周期性地从粒状过滤介质使油成为溶剂化物,而不影响过滤介质的完整性,接着回洗过滤器以除去现存的无油固体。然后可以通过重力沉降来分离得到的油-水滤液。然而,当存在大量亚微米大小的超细液滴时,过滤技术基本上不能产生不含油的水,而且没有任何机会完全分离出可售数量油。此外,考虑到过滤介质的孔径大小,过滤技术非常耗时。此外,过滤介质的再生是一个高度乏味和耗时的任务。任选地,凝结剂或絮凝剂也可以用于克服上述离心机和/或过滤器的缺点。然而,这些凝结剂/絮凝剂破坏或污染油的品质。此外,凝结剂/絮凝剂的加入是缓慢的过程且耗时。如果通过水保持油滴,除非使用乳化剂,否则过滤器和离心机都不工作。例如,通过过滤或离心不能从牛奶中除去全部脂肪,因为脂肪由蛋白质保持,在这种情况下蛋白质是乳化剂。现有技术中可看到使用气浮技术来除去乳化油颗粒。例如,ChristineAngelldou等人题为“Theremovalofemulsifiedoilparticlesfromwaterbyfloatation”的研究论文,Ind.Eng.Chem.ProcessDes.Dev.,1977年,16(4),第436-441页,讨论了通过空气浮选技术使用气泡来回收油颗粒,其中已经研究了悬浮在低浓度的水中的乳化油颗粒的浮选。使用了两种油,其中油浓度高达200毫克/升。为了实现分离,在浮选池中使用各种阳离子表面活性剂,其与外部全循环分批操作。结果发现,随着添加表面活性剂达到限制值,水中浮选率升高了。海盐的存在降低了浮选率。然而,空气浮选技术并非没有限制。首先,空气浮选仅在油浓度高达200ppm是可行的,它无法超越所述ppm级。其次,这些技术利用表面活性剂,其高度污染油和结合水的品质。此外,在空气浮选技术中清除固体和结合水是不可能的。因此,考虑到通常作为未经处理垃圾发现巨大体积的污泥,需要用于石油污泥处理的工艺流程,其有利于从污泥中回收可用油和可用水。此外,除了破乳剂的使用(其可在少数情况下使用),目前需要一种从石油污泥中除去结合水的工艺流程。此外,考虑到通常作为通过乳化剂分散到水中或结合到水中的巨大体积的废油,需要用于废油处理的这样的工艺流程,其有利于从废油中回收可用水。此外,需要这样一种工艺流程,除了从其回收可用油之外,还通过具有成本效益的方式将废油转化为可用水。发明目的本发明的目的是从包含有烃、结合水、非结合水、固体和溶解盐的石油/原油污泥和乳状液中除去结合水和非结合水,变成不同纯度的可售流体。本发明的另一个目的是提供一种用于污泥处理的方法,该方法成本低廉并有利于尽可能完全地回收纯油和水,而不破坏其原始组分/特性。本发明的再一目的是提供一种废油处理的方法,通过有效且经济上可行的工艺从废油中回收可用水。本发明的另一个目的是,除了减少废油污染的问题,还通过有效且经济上可行的方法从废油中回收可用烃。发明概述在本发明的优选实施方式中,公开了一种用于污泥混合物处理的方法,其中污泥混合物包括烃,其中具有结合水,非结合水,溶解和未溶解固体。如果污泥混合物分成各种组分,用于污泥混合物处理的方法包括:第一步,在第一离心机中离心污泥混合物。作为间歇式离心机的第一离心机形成粘稠烃层,废油层和自由流动烃层。在下一步中,粘稠烃层在第一脱盐设备中脱盐,任选地,随后是在热基低挥发物汽提容器中进行处理,从其中除去低沸点液态烃的蒸汽。在下一步中,低沸点液体烃的蒸汽在第一冷凝器中冷凝,用于获得低沸点的液态烃与水以备使用。任选地,来自集团收集中心的粗烃在第二脱盐设备中脱盐,用于获得脱盐粗产品,从而除去含烃层的结合水,其随后与来自第一离心机的粘稠烃层混合。在接下来的步骤中,自由流动烃层在第三脱盐设备中脱盐,用于从中除去全部盐。在下一步中,通过加入第一预定量的溶剂在匀浆器中处理粘稠烃层,用于从中形成挥发性游离非粘稠均化流。在下一步骤中,进行非粘稠均化流的BTX和灰分测试,然后在搅拌器兼均化器中对其处理,从而根据BTX和灰分测试的结果在其中添加第二预定量的溶剂。在下一步中,在第二离心机中离心非粘稠均化流,用于从其中分离出结合水占主导的烃流,非结合水占主导或不含水的烃流和废油。任选地,在热绝缘沉降槽中处理非粘稠均化流,用于从中除去无水溶剂以及烃。在下一步中,在第一加热容器中加热非结合水占主导或不含水的烃流,从而任选地添加预定量的游离水。第一加热容器在第一预定温度范围内运行,从而形成第一残留相和第一蒸气相。在下一步中,在第二加热容器中在第二温度范围加热结合水占主导的烃流,从而任选添加第三预定量的额外溶剂。第二加热容器形成了第二残留相和第二蒸汽相。在下一步中,在热离心机中于第二预定温度范围离心第一残留相,用于获得无挥发物的脱盐产品烃,其范围在96wt%-100wt%以及具有至少低于20NTU浑浊度的非结合水。在下一个步骤中,在第一加热容器中处理第二残留相。在下一个步骤中,通过第二冷凝器冷凝第一蒸汽相和第二蒸汽相以获得至少100%的溶剂,结合水的范围约99wt%-100wt%,游离水的范围约94%-99wt%。在所述过程中重复利用溶剂。第一离心机降低了需要进一步处理的污泥混合物与结合水的总量,节省了进一步处理的成本和时间。自由流动烃层约为41wt%,通常具有3,864ppm的水和具有10,635kcal/kg热值的0.88wt%的灰分。粘稠烃层具有至少42.21wt%的水,通常具有热值5,210kcal/kg的8.61wt%的灰分。通过延长污泥停留时间,第一离心机增强了存在于污泥中的组分之间的分离,从而逐渐改变批量离心机的每分钟转数,使得可以采集粘稠烃层后面的废油。第一脱盐设备,第二脱盐设备和第三脱盐设备保留来自不同工艺流的烃的质量,从而提高其商业价值。第一脱盐设备,第二脱盐设备和第三脱盐设备防止在集团收集中心进行的相同工艺流程的不必要重复,这些工艺用于从在原油脱盐之后再次进入炼油厂的原油中除去结合和非结合水。第一脱盐设备,第二脱盐设备和第三脱盐设备防止水侵入到炼油厂中的各种产品的烃流中,从而防止污泥在所述工艺流程下游及来自炼油厂之后的工艺的容器中的积累。第一脱盐设备,第二脱盐设备和第三脱盐设备允许集团收集中心调度无盐原油,而无需担心含结合水原油的任何处置或处理。第一脱盐设备,第二脱盐设备和第三脱盐设备防止运输过程中管线和罐车的腐蚀。基于加热的汽提容器从粘稠烃层中分离低挥发物,用于防止其在所述工艺的下游除去结合水和溶剂期间与溶剂共蒸馏。从粘稠烃层中除去结合水也允许由此除去重金属,灰分和盐分,其有效地提高了它的商业价值。BTX和灰分测试有助于确定在所述过程中添加的溶剂量。就粘度而言,溶剂降低粘度,以用于从非粘稠均化流的最上层中除去结合水。溶剂有助于污泥的均质化,其反过来有助于采样,并进一步有助于准确确定水和灰分的含量。仅将溶剂添加在所述工艺的烃的粘稠部分中,大大降低了溶剂的总体使用。溶剂选自由苯、甲苯、二甲苯和类似的水共沸物构成的组中。溶剂有助于从最上层中除去结合水,且对所述最上层的产品烃流产生尽可能少的热损伤。溶剂流和第二离心机在环境温度下交替地从粘稠烃层中除去大量的结合水。溶剂降低了结合水的沸点。为了除去全部结合水,溶剂的加入量范围约为污泥中的水存在量的1.8至100倍。溶剂与烃的剩余重量比的最小范围在2.00至6.00,用于在最低温度下完全除去结合水。得到的结合水是高品质的可用水,其需要最小处理,以用作饮用水。第一加热容器的第一预定温度在约90℃至105℃的范围内。第二加热容器是多效蒸发器,优选具有热蒸汽再压缩功能,以避免产品烃流热裂解。第二加热容器包括消泡器和适于避免冷凝器中烃夹杂的夹带物分离器。第一加热容器包括消泡器和适于避免冷凝器中烃夹带的夹带物分离器。第二加热容器保持受控的速率,以最佳比率加热溶剂残留物与水,用于从烃中完全除去结合水。第一和第二加热容器设置有余热,用于节省在所述工艺中的能源成本。热离心机是一种热沉降槽,以确保充分减少烃的粘度,从而允许存在于其中的游离水在一段时间内沉降。热离心机具有在约80℃至94℃范围内的温度。热沉降槽可以在高压下操作,使得可以提高操作温度以进一步减少烃的粘度,其有利于快速除去游离水,而不会导致水的沸腾。在本发明的可替换的实施方式中,公开了一种用于预处理废油的方法,其中废油含有水、固体、盐和大于10,000PPM的烃含量,具有或不具有结合水。用于预处理废油的方法包括:起始步骤,在第一沉降槽中供给废油用于相分离,从而形成基本上不含有非结合水的具有或不具有盐的烃层、水占主导的烃层和烃含量小于10,000PPM的废油层。在下一个步骤中,在第二沉降槽中通过在其中添加预定量的明矾处理水主导层。第二沉降槽形成了基本上不含有非结合水的烃层、凝胶状的含油层和烃含量小于10,000ppm的含明矾废油。任选地,在第三离心机中通过添加预定量的溶剂离心凝胶状的含油层。第三离心机形成了溶剂层,其包含明矾以及涂覆有烃的固体。在所述工艺中,将含有明矾的溶剂层添加至第一加热容器中。第三离心机有助于从废油中快速分离溶剂以及烃层和凝胶状的含油层。在本发明的另一替代实施方式中,公开了一种废油处理的方法,其中废油含有水、固体、盐和小于10,000PPM的有限烃含量,具有或不具有结合水。该方法包括:初始步骤,通过连接薄的顶层中存在的大部分油,将废油通过第四离心机离心以获得低浑浊度的废油。在下一步骤中,通过在高速剪切混合器中添加溶剂处理上述废油,以形成混合物,然后在第五离心机中对其离心,用于由此获得水占主导的烃层和溶剂占主导烃层。在下一步骤中,对结合水进行溶剂占主导的烃层的BTX和灰分测试,接着在第三加热容器和第四加热容器中对其进行加热处理。第三容器具有加入其中的预定量溶剂。第四容器具有添加入其中的预定量游离水。第三加热容器和第四加热容器从液相中分离气相。气相中具有全部的剩余溶剂和游离水。液相具有烃,其中具有有限的固体、有限的盐和明矾。在下一步骤中,将液相通过在预定温度下运行的第六离心机离心,用于从水层中分离产品烃层。其中,水层具有有限的盐、有限的固体和明矾。在下一步骤中,通过第一反渗透装置处理水层,用于获得可使用的水和废物流。在下一步骤中,通过第三冷凝器冷凝气相,用于获得可使用的水和溶剂,溶剂可以在高速剪切混合器中重复使用。在下一步骤中,在第五加热容器中加热水占主导的烃层,用于从中分离溶剂蒸汽,然后在第三冷凝器中将其冷凝,以得到重复利用的溶剂和可使用的水。第五加热容器产生液相,液相包括剩余的水、有限烃、盐和固体,具有基本上低的浑浊度。在下一步骤中,在沉降槽中处理液相,接着向其中加入预定量的明矾。沉降槽形成水占主导的明矾层和凝胶状的含油层。在下一步骤中,在过滤装置中过滤水占主导的明矾层。过滤装置将水占主导的明矾层分离成滤液流和残留物流。滤液流中包括水、明矾和盐。残留物流包括湿固体,具有微量的烃、盐和明矾。在第二反渗透装置中处理滤液流,用于从中回收可用水。根据本发明,过滤装置使废油的浑浊度数值降低至低于1NTU。过滤的有效性取决于过滤介质的孔尺寸和存在于废油中的烃的性质。在下一步骤中,残留物流与凝胶状的含油层混合,然后在第一热干燥器中将其干燥,用于获得含有烃、明矾、固体和盐的粘稠液体。在下一步骤中,通过添加预定的溶剂,在搅拌器及脱油装置中搅拌粘稠液体,然后通过第七离心机对其处理,从而在其中添加水。第七离心机提供了水层、滤饼层和溶剂层,其中水层具有明矾、盐和有限的溶剂。滤饼层优选是脱油固体的滤饼,具有溶剂、有限的盐和有限的明矾。在第六加热容器中处理水,用于获得溶剂和水的蒸汽,然后通过第四冷凝器对其处理,用于获得可重复利用的溶剂和可使用或在所述工艺中进一步处理的水。在下一步骤中,在第四加热容器中处理溶剂层,用于回收溶剂。在下一步骤中,在第二热干燥器中处理滤饼层,用于通过冷凝器回收溶剂。第二热干燥器中生产出具有微量明矾和盐的干燥脱盐固体。第三加热容器是多效蒸发器,优选具有热蒸汽再压缩功能以避免产品烃热裂解。第三加热容器具有在约70℃至150℃范围内的温度。第四加热容器具有在约90℃至105℃范围内的温度。第五加热容器具有在约90℃至105℃范围内的温度。第六离心机是热离心机,其具有在约80℃至94℃的温度。第六离心机是热沉降槽,其具有约80℃至94℃的温度。可以在高压下操作热沉降槽,使得操作温度提高至可以进一步降低烃的粘度,这有利于快速除去游离水,而不会导致水的沸腾。第六加热容器是蒸发器。第六加热容器具有约90℃至105℃的温度。BTX和灰分研究有助于确定在所述工艺中溶剂的添加量。溶剂选自由苯、甲苯、二甲苯和其它水的共沸物构成的组中。第一热干燥器具有约为108℃的温度。第二热干燥器具有约为200℃的温度。第一反渗透装置除去明矾、盐和固体,以产生可用品质的水。在第二沉降槽中添加的明矾中和表面电荷,其有利于通过絮凝快速分离烃和凝胶状的含油层的形成。当废油具有低于90NTU的浑浊度时,第三沉降槽中明矾的添加使最小的烃液滴放电并絮凝它们,从而降低浑浊度为90wt%至99wt%的范围。添加明矾本身是缓慢的过程,但可以通过施加热量对其加速,因此,明矾处理的有效性取决于温度和时间。第四离心机是多程离心机,其将废油的浑浊度数值降低到极限值,超过该极限值后,离心机不能产生任何进一步数值的添加,因为那时分散的油滴尺寸变化变窄,而分散的油滴的分布密度也随着平均游离路径的增加下降,残留液滴是带电的,密度差很小。当废油的起始浑浊度数值非常高的时候,放大了离心的上述空白值。当离心机达到其极限值时,通过高剪切混合器添加溶剂。通过带来液滴尺寸的较大改变以及通过增加液滴的分布密度和增加油与水的密度差,添加溶剂提高了离心机的运行范围。离心机再次达到极限值,在该点处,残留溶剂与游离水在约90℃至99℃的温度范围内煮沸出来。在本发明的另一替代实施方式中,公开了一种用于污泥混合物处理方法,该方法包括离心机的方法。仅使用离心机的处理方法包括在离心机中离心含烃、结合水,盐和溶剂的污泥的步骤,以通过提高烃在离心机的停留时间打破烃之间的结合,从而形成三种不同的层,即具有结合水,盐及固体的粘稠烃层,具有有限的盐和固体的自由流动烃层和具有有限的盐和固体的游离水。通过缓慢增加其每分钟的转速,缓慢减少离心机纵轴与水平面间的角度,通过逐渐减小但不使其成为0°,离心机使得粘稠烃层重新定位,从离心机的后侧变为中间侧。污泥混合物具有需要进一步处理的结合水,这节省了进一步处理的成本和时间。离心机供给了大量可销售的产品烃,即自由流动烃。在本发明的另一实施方式中,公开了一种具有离心和溶剂组合效果的处理污泥混合物的方法,其中污泥混合物包含结合水,盐和固体。该处理方法包括初始步骤,将预定量的溶剂添加到污泥混合物,然后对其混合,以降低污泥混合物的粘性。在下一步骤中,在离心机中离心污泥混合物,以获得烃和溶剂的大面积层、含烃和结合水的层以及游离水层。离心机具有延长的停留时间,用于在其中得到更少的污泥与结合水。在大气压强下,于90℃至99℃的温度范围,通过游离水的沸腾处理溶剂和烃的大面积层,用于回收溶剂。污泥混合物具有需要进一步处理的结合水,从而节省了进一步处理的成本和时间。离心机供给了大量可销售的产品烃,即自由流动烃。附图说明图1是工艺流程图,示出了原油在集团收集中心的生产和收集;图2是工艺流程图,示出了从中除去结合水之前,图1的污泥混合物的处理;图3是工艺流程图,示出了图2的污泥混合物的处理,用于从其中除去结合水;图4是工艺流程图,示出了废油的处理,其具有高于10,000PPM的烃含量;图5是工艺流程图,示出了废油的处理,其具有等于或小于10,000PPM的烃含量;图6是图5的持续工艺流程图,示出了废油的处理,其具有等于或小于10,000PPM的烃含量;图7示出了使用高剪切混合器将苯与水在2500PPM速率混合1分钟时的图示;图8示出了使用高剪切混合器将苯与水在5000PPM速率混合1分钟时的图示;图9示出了使用高剪切混合器将甲苯与水在2500PPM速率混合1分钟时的图示;图10示出了示出了使用高剪切混合器将甲苯与水在5000PPM速率混合1分钟时的图示;图11示出了使用高剪切混合器将二甲苯与水在2500PPM速率混合1分钟时的图示;图12示出了使用高剪切混合器将二甲苯与水在5000PPM速率混合1分钟时的图示;图13示出了使用高剪切混合器将椰油与水在2500PPM速率混合1分钟时的图示;图14示出了使用高剪切混合器将椰油与水在5000PPM速率混合1分钟时的图示;图15示出了使用高剪切混合器将椰油与水在2500PPM速率混合3分钟时的图示;图16示出了使用高剪切混合器将椰油与水在2500PPM速率混合5分钟时的图示;图17示出了使用高剪切混合器将印度石油天然气公司(ONGC)油与水在2500PPM速率混合1分钟时的图示;图18示出了使用高剪切混合器将ONGC油与水在5000PPM速率混合1分钟时的图示;图19示出了使用高剪切混合器将ONGC油与水在2500PPM速率混合3分钟时的图示;图20示出了使用高剪切混合器将ONGC油与水在2500PPM速率混合5分钟时的图示;和图21示出了使用高剪切混合器将柴油与水在2500PPM速率混合5分钟时的图示。发明详述使用特定的示范性详细说明对本发明进行说明或更好地理解。然而,本领域的技术人员不使用这些特定的详细说明也能实现本发明。说明书中“一种实施方式”或“一实施方式”意味着:描述的与实施方式相关的特定特征、结构、特性或功能都包括在本发明的至少一个实施方式中。说明书中不同地方出现的短语“在一实施方式中”未必全部指代同一实施方式。说明书中“优选实施方式“意指详细描述的特定特征、结构、特性或功能,为了清楚描述本发明,省略了已知结构和功能。在说明书和权利要求中,术语“污泥”被广泛地定义为烃、结合水和非结合水、溶解和未溶解固体和天然存在的乳化剂的混合物。根据本发明,污泥是一种包含2wt%-95wt%总含水量的污泥。然而,当总含水量在2wt%-61wt%的范围时,在不另外加入乳化剂时,烃中的全部水是结合水。当水含量大于61wt%时,水是结合水和非结合水的组合。污泥是致命的污染物,因为它含有重金属,除掉它成本高昂。它可以通过低挥发物污染土地,水甚至空气。在说明书和权利要求中,术语“废油”被广泛定义为烃、乳状液、未溶解的固体、涂覆未溶解的固体和溶解固体、结合水和非结合水的烃的混合物。根据本发明,废油具有5ppm-5lacppm的烃含量。这些烃不溶于水。通常,当油含量超出10,000ppm时,它会相当迅速地分为三层,具有PPM级水的纯油的可滗析上层,大量的中间含油水层,其中纯油的分离速率较慢,和残留物底层,其含少于10,000PPM的废油。在说明书和权利要求中,术语“结合水”被广泛定义为不释放烃的水,尽管在21893RCF离心分离污泥至少十分钟是结合水。在说明书和权利要求中,术语“非结合水”被广泛定义为除了结合水以外的任何水。在说明书和权利要求中,术语“溶解固体”被广泛定义为溶于来自污泥中的水中的固体。在说明书和权利要求中,术语“未溶解固体”被广泛地定义为重金属,包括与原油一起从油井中出来的放射性金属。参考图1,流程图100示出了石油原油102经历的过程,通过多个油井101回收后接着在集团收集中心104(GCC,下同)对其进行处理,如图所示。石油原油102优选包含硫、结合水、非结合水、盐和固体。然而,如果存在,气体,在运送至GCC104之前,从101A管线上的原油102中除去。GCC104包括脱硫装置106,其经由管线108从原油102中分离出硫,从而形成无硫原油流110,其包含原油与结合水,非结合水,盐和固体。将无硫原油流110供给到基于重力的沉降槽112中。基于重力的沉降槽112将原油分离成三个流,即上原油流114,中原油流116和下原油流118。上原油流114包含原油与盐,有限的固体和微量的水,它们沿着管线A。下原油流118包含水与盐、固体和有限原油,它们沿着管线B。在此应当理解,在这一优选实施方式中,下原油流118是废油流,其具有小于10,000PPM的烃含量。中原油流116包含原油与盐、结合水、非结合水和固体,通过管线119将其供给到热绝缘沉降槽120中。热绝缘沉降槽120在大气压强下,于约95℃或小于95℃的温度下操作。任选通过管线124将破乳剂112添加至热绝缘沉降槽120中。另外,在这一实施方式中,将高电压振荡电场125提供给热绝缘沉降槽120。热绝缘沉淀槽120处理中原油流116,从而在其中形成三层,即顶部原油层126,中部原油层128和底部原油层130。顶部原油层126包含原油与盐,有限的固体和微量的水,它们沿着管线A。底部原油层130包含水与盐、固体和有限原油,它们沿着管线B。在这一实施方式中,底部原油层130是废油,其具有小于10,000PPM的烃含量。在这一优选实施方式中,根据本优选实施方式,中部原油层128优选是污泥,其包含原油与结合水、盐、有限非结合水和有限的固体。因此,在这一优选实施方式中,污泥128沿着管线C。参照图2,示出了从其中除去结合水之前,用于处理污泥128的工艺200。通过管线C将污泥128供给到第一离心机202中。此外,将来自所有其它来源的有盐或无盐的多个污泥204连同污泥128添加到第一离心机202。在这一优选实施方式中,第一离心机202是间歇式离心机或多程离心机。第一离心机202形成了三层,即顶层208,中层206和底层210。底层210优选包含水与盐,固体和有限的原油。中层206优选是粘稠烃层与结合水、有限的固体和微量的有盐或无盐的非结合水。顶层208优选包含自由流动烃,其具有盐或无盐,有限的非结合水和有限的固体。在这一实施方式中,底部原油层210是废油,其具有小于10,000PPM的烃含量。如果中层206含盐,优选通过管线211供给中层206到第一脱盐设备212。将预定量的游离水加入第一脱盐设备212中,以获得上游流体213和下游流体214。在这一实施方式中,下游流体214优选包含水与盐、固体和有限原油,其与底层210混合。上游流体213优选包含脱盐粘稠烃与结合水、有限的非结合水和有限的固体。在这一实施方式中,上游流体213沿着管线213-A。可替代地,如果中层206无盐且是低挥发物时,可以通过管线215直接供给中层206到均化器216。在此应当理解,在供给到均化器216前,管线215可以与管线213混合。如果顶层208含盐,优选通过管线217将顶层208供给到第三脱盐设备218。将预定量游离水添加至第三脱盐设备218中,以获得两个层或三个层。如果它具有一部分其中包含结合水,则第三脱盐设备218产生上层220,底层222和任选地中层224。上层220是自由流动的无盐烃产品,其具有有限的固体和微量的水。底层222包含水与盐,固体和有限的原油,它们沿着管线B。在这一实施方式中,底部原油层222是废油,其具有小于10,000PPM的烃含量。在这一实施方式中,如果形成了中层224,将其添加至上游流体213。将沿着管线A的包含原油与盐、有限的固体和微量水的原油流114供给到第二脱盐设备228中(参照图1)。第二脱盐设备228优选形成了三层,即顶层230,中层232和底层234。底层234包含水与盐,固体和有限的原油,它们沿着管线B。在这一实施方式中,原油底层234是废油,其具有小于10,000PPM的烃含量。顶层230是脱盐粗产品,其具有微量固体和水,其作为产品回到炼油厂。中层232包含具有结合水的脱盐粘稠烃,将其添加至流213,并供给到均化器216。均化器216处理脱盐粘稠烃层与结合水、有限的非结合水和有限固体,从而在烃高粘性的情况下,添加有限的溶剂流236。有利地,均化器216便于在降低污泥的体积后添加溶剂,并且特别用于粘稠烃部分,从而在此过程中显著降低了溶剂的整体使用。还将溶剂添加至均化器216,以有助于在该工艺中进行BTX研究。考虑到黏性,溶剂236也有助于降低黏性,用于除去结合水。在这一优选实施方式中,溶剂236选自苯,甲苯和二甲苯中的一种或多种。均化器216产生了非粘稠均化流238,其沿着示出的管线D。流238优选包含烃,它们无挥发物,是脱盐的和非粘稠的。在非粘稠均化流238中,烃中优选含有结合水,有限的非结合水和有限的固体。任选地,如果流体213中的脱盐粘稠烃包含低沸点挥发物时,可以采用热基低挥发物的汽提容器240。在这种情况下,经由管线214将流体213发送至热基低挥发物汽提容器240,而不是经由管线213-A发送至均化器216。然而,如果粘稠烃层206是无盐的但其中包含低挥发物时,可以通过管线214直接供给粘稠烃层206到热基低挥发物汽提容器240。热基低挥发物汽提容器240在工艺200中进行调节,以防止低挥发物与溶剂一起分离出来,污染溶剂,然后这些烃需要分馏,这将增加不必要的高成本。因此,热基低挥发物汽提容器240在该工艺中被调节以分离低挥发性烃。热基低挥发物汽提容器240具有废热以促进加热。热基低挥发物汽提容器240形成气相246和液相248。气相246优选含有低挥发物,烃和水的蒸汽。液相248优选不含有挥发物,但含有脱盐热烃,其具有结合水,有限的非结合水和有限的固体。将气相246传送至第一冷凝器250,用于从中除去热量,接着通过第一冷凝/相分离器252处理。冷凝器/相分离器252优选形成第一层254,第二层256和第三层258。第一层254包含纯净水,其在工艺中重复利用或包装后进行出售。第二层256包含低沸点液体烃,其通过管线260与脱盐粗产品230混合。第三层258包含烃的非可冷凝蒸汽,如图所示其作为热源经由管线262燃烧。将液相248供给到冷却容器264,其中将热烃冷却到室温,并经由管线266将其添加至均化器216,以随后产生产品流238,其沿着如图所示的管线D。在此应当理解,在来自ONCG泻湖的典型污泥情况下,第一离心机202能够分离污泥,其中人们可以找到一小部分粘稠烃,浮在载有约40-44wt%结合水和13wt%灰分的顶部。能够获得约40wt%的自由流动烃,其含有0.3wt%至0.8wt%的灰分和小于3000ppm的水。出来的水具有远低于20NTU的浑浊度。人们不能将该水回添加至烃中,也不能制造污泥,从而防止复水。参照图3,示出了用于处理产品流238以除去结合水的工艺300。在进行BTX研究302和灰分含量研究304之后,通过管线D将产品流232(参照图2)供给到搅拌器兼均化器306中。进行BTX研究302以检测在产品流328中的水分含量,进行灰分含量研究304以检测在产品流238中的水分含量,进行灰分含量研究304,以检测产品流238中的灰分含量。通过管线310在搅拌器兼均化器306中添加计算量的溶剂308。在此应当理解,加入的溶剂数量影响搅拌器兼均化器308,以在最低温度从烃中取出水。在二甲苯用作溶剂的情况下,优选地,二甲苯与烃/水的重量(以较高者为准)比是5.5。在甲苯用作溶剂的情况下,优选地,甲苯与烃/水的重量的比是10.0。在苯用作溶剂的情况下,优选地,苯和烃/水的重量的比是80.0。在下一步骤中,通过管线311将搅拌器兼均化器306中的物质供给到第二离心机312。任选地,将搅拌器兼均化器306中的物质供给到热绝缘槽312A,分离出含有溶剂和烃的无水顶层312B。无水顶层312B沿着图示的管线J。第二离心机312将物质分为三层,即第一层314,第二层316和第三层318。第一层314是非结合水占主导的烃流,其中优选包含无挥发物的脱盐烃,溶剂,有限的非结合水和固体。第二层316是结合水占主导的流,其中优选包含无挥发物的脱盐烃,具有结合水,溶剂,有限的结合水和固体。第三层318优选包含水与盐,有限的烃和溶剂,沿着管线B。在此应当理解,在热绝缘槽312A中的物质可以经由管线321C与第三层318混合。在这一实施方式中,第三层318是废油,具有小于10,000PPM的烃含量。在此应当理解,在均化器306中人们放入高达61%的结合水的烃进行处理,其中水和烃之间密度差在0.05gm/cc的范围内,并含有尽管以21900RCF离心10分钟也不会从第一离心机202出来的结合水。然而,在添加溶剂308之后,接着在第二离心机312中降低粘度,在随后的处理中全部结合水出来。在此应当理解,相同的烃已经在第一离心机202中经历了类似的离心力作用,其中粘度仍然降低,这里回收的水却还没有出来。回收结合水的这一事实是本发明的发现。经过管线322将第一层314供给到第一加热容器320。在这一优选实施方式中,第一加热容器320在大气压下和约90℃至105℃的温度范围内运行,更优选在90℃至98℃的范围内。将预定量的游离水添加到第一加热容器320,供给废热以在所需温度下加热第一加热容器,产生第一残留相324和第一蒸气相326。在烃中有盐和/或灰分或固体的情况下,然后除了在低于100℃的温度下沸腾全部纯溶剂,以供再利用或销售,游离水可以进行脱盐和脱灰的额外功能。第一蒸气相326优选包含全部残留物溶剂的蒸汽和部分结合水,其被供给到第二冷凝器328,在那里从蒸气中除去热量以形成液相,液相通过管线329移到第二冷凝相分离器330。第二冷凝相分离器330将液相分离成溶剂相324和水相334。在该工艺中优选重复利用。水相334是纯净水,具有低于5NTU的浑浊度,其在工艺中循环使用或包装出售。第一残留相324优选包含烃和具有有限固体的剩余非结合水,将其供给到热离心机/热沉降槽336。热分离机336在大气压下和优选在小于或等于95℃的进气温度下运行,更优选在92℃至93℃的进气温度。热分离机336优选将液体流分成两层,即顶层338和底层340。顶层338优选包含无挥发物脱盐烃产品,其具有微量的水/固体,水含量小于5000ppm。底层340完全包含非结合水,具有固体和微量的烃。如果底层340具有低于5NTU的浑浊度,则底层340经由管线341与水相334混合。或者,如果底层340浊度大于5NTU,则经由管线343将底层340供给到基于明矾的沉降槽342。基于明矾的沉降槽处理水,以将浑浊度降低到低于5NTU,然后经由管线344将其与水相334混合。在此应当理解,在本发明的其他替代性实施方式中,基于明矾的沉降槽342可以是过滤装置或反渗透装置。通过管线348将第二层316供给到第二加热容器346,其在大气压下和在优选在70℃至150℃的温度范围内运行,其中为了加热目的施加废热。然而,在此应当理解,在本发明的替代性实施方式中,第二加热容器346可以是有热蒸气再压缩功能的多效蒸发器。另外,应当理解,在本发明的又一实施方式中,第二加热容器346可以是消泡器和夹带抑制器。如果需要,将预定量的溶剂加入到第二层316。第二加热容器346形成第二蒸气相350和第二残留相352。如上所述,第二蒸气相350包含具有全部结合水和非结合水的溶剂蒸气,按蒸气相326的处理过程,将其供给第二冷凝器328和并通过第二冷凝器328处理。如图所示,将第二残留相352加入第一加热容器320,并经过其进行处理。现在再次参照图1到图3,运行中,第一分离机202有利于在环境温度下将污泥快速分离成增值层,其中进来的污泥的典型热值为约6,044kcal/kg,水含量约40wt%,灰分含量3.68wt%。第一离心机大大降低了污泥的质量,随后处理三次以上,然后在所有可能的不同后续处理中将进来的烃分离成两个馏分,这两个馏分的市场价格不同。特别地,在用浊度小于20NTU的明矾进行后续处理之后,第一离心机202以4500的相对离心力(下文称为RCF)操作十分钟,以产生约41wt%的自由流动烃层220,具有3,864ppm水和0.88wt%灰分,其具有10,635kcal/kg的热值,约32wt%的粘性烃层,其具有42.21wt%水和有5,210kcal/kg热值的8.61wt%灰分,和26wt%废油。运行中,第一离心机202在较长的时间内增强浮力的力,通过逐渐增加转速并且还通过枢轴将离心瓶保持在转子上实现。第一离心机202提供了一个延长的停留时间与增强的浮力,其允许建立分离液体的液滴之间足够大的动能差,然后,在超过阈值时,其提供了破坏将这些液滴保持在一起的键所需的能量。破坏键是必要的,但不是充分的。随后,尽可能完全地通过彼此携带这些不同的材料,然后将它们收集到不同的,单组分的层206,208和210。增强的或增加的停留时间或离心力挤压出更多的水,并在小程度上甚至从粘稠烃213中挤压出油,并通过这样做使得它更加粘稠,从而达到一个限制点,超出该点,尝试任何进一步的处理都是没有意义的。合并逐渐增加RPM和保持离心瓶的枢轴可能具有一些其它的影响。最初,较小的低离心力的RPM限制了粘稠烃的积累,其有助于收集如块状的粘稠烃,而不使它们如饼状一样扁平。另外,低RPM,其中重量的力大于离心力,有助于在瓶内的底部空间收集粘稠烃,从而在顶部留下足够的自由空间。这有助于最初释放弱结合水达到末端,然后再收集这些块状物。粘稠烃优选随着时间增长,因为增加了额外的材料。随后,更多水释放和在顶部收集粘稠块,从而从瓶的底部释放粘稠烃,然后缓慢将他们移向在中央的他们的最终位置。此外,当RPM上升,浮力的力上升,以通过减小它们与水平方向角度逐渐旋出瓶子,有了上述描述,工艺变得更加生动。最终,这些瓶子变得接近水平,但从不完全水平。在结束时,与水平方向间将有一些小的残留角度。最终,离心机202允许粘稠烃随着时间和高离心力变平成厚的圆盘形层。但即使如此,由于这些瓶子是从来没有真正水平,因此这个盘在其最高点与瓶子表面接触有限,其为水的渗透和在其后收集提供了相对容易的开始。在运行中,三个脱盐设备212,218,228有利于原油在除去结合水之前,而且也在将其调度到炼油厂之前的脱盐。根据本发明,这具有特殊重要性。工艺200包括脱盐设备212,218,228的放置,在所提出的工艺中,允许原油不同于其它当前位置的特定位置脱盐。在GCC早期进行了相似的工艺之后,脱盐设备212,218和228防止在炼油厂不必要的,昂贵的,耗时的和消耗资本的重复原油脱水。此外,脱盐设备212,218和228提高了产品的质量,节省了在能源上的费用,通过防止水侵入在炼油厂的原油流。这又减少了或消除了污泥在产品供应链下游的积累。在工艺200公开的位置处的脱盐设备212,218和228有利于减轻结合水在脱盐的同时进入原油的问题,而不具有蒸馏塔的优点。相比于仅仅脱盐,脱盐设备212,218和228防止有结合水的烃与有非结合水的烃和产品烃流的混合。这也允许防止粘稠烃与自由流动烃的混合。第二脱盐设备228具有调度脱盐烃到炼油厂的独特能力,而不用结合水装载它们。运行中,在烃与结合水和低沸点挥发物一起进来的情况下,热基低挥发物汽提容器240便于汽提。在使用溶剂除去结合水之前,甚至在将溶剂加入到工艺200之前,热基低挥发物汽提容器240汽提这些低挥发物,并通过加热分离它们,从而在在工艺200的下游去除溶剂和结合水期间,防止了低沸点挥发物与溶剂一起蒸馏出来,其中根据使用的溶剂,最终温度可以上升到至少高达140℃。汽提容器240还可以防止低挥发物进入溶剂的后续的纯化,否则其将成为一种更加昂贵和复杂的过程。此外,在除去结合水期间,热基低挥发物汽提容器240防止低沸点挥发物与溶剂一起蒸馏出来,随后在均化器306和第二离心机312中使用溶剂,然后在第一加热容器320中,将其曝露于至少高达98℃的温度。热基汽提容器便于低沸点烃的回收,可以将其再循环回到脱盐产品粗品230,除了保存和经济上的优点,其有助于以尽可能原始的形式送回烃。如果低挥发物的一部分由于热裂解变为不可冷凝流258,然后将喷焰燃烧或燃烧那部分,以提供额外的热源。此外,在第二离心机312之前加入溶剂比在第一离心机202之前加入溶剂更重要。这部分原因是因为人在这种情况下最终会消耗更多溶剂,因为它将不必要地和自由流动烃混合。这可能导致额外成本和工艺,用于随后从自由流动烃中除去溶剂。此外,在这种情况下,除去的溶剂将被低沸点烃污染。此外,在这种情况下,人最终会将低值粘稠烃与高值自由流动烃混合。在运行中,在某些情况下,在除去具有低于20NTU的浑浊度值的清水之后,第二离心机312处理含溶剂的污泥。第二离心机312从供给到其中的污泥流中除去全部残留结合水,例如炉油污泥,ONGC粘稠烃等。第二离心机312不从污泥中除去全部结合水,在那里一部分烃由于乳化剂保留有结合水。除了除去结合水,第二分离机也有助于减少烃中的灰分。然而,在此应该理解,由于粘度高导致阻力大,仅仅单独使用第二离心机312而没有溶剂不能除去微量的结合水,尽管用10分钟的长停留时间并在高达21,900的RCF值离心。使用溶剂流308降低粘度是极其重要的,并当随后使用时,使离心机312有效。另一方面,溶剂本身比离心机312更有效,由于部分水被烃紧紧地保持,但是尽管有72小时的停留时间,离心机312仍然未能除去全部结合水。通过单独使用溶剂,甚至当温度加热到稍低于其共沸温度,或通过单独使用离心机,都不能分离结合水。因此,按照本发明,合并使用溶剂流308与第二离心机312以在环境温度下从粘稠污泥中完全并快速地分离结合水是极其重要的。工艺300结合了增加的浮力和额外的污泥的粘度的显著降低,浮力增加是由于重力导致速度增加所致,粘度的降低是通过使用溶剂(例如二甲苯)来实现的,浮力在环境温度下和在较长的时间周期内,是两倍于污泥自身重量,从而影响从粘稠烃中完全分离结合水,通过在同一时间内单独使用甚至4.87倍更强大的离心机,或通过在两倍于环境温度下在72小时内(与10分钟相比),以相似的比例单独使用相同溶剂,都不可能从粘稠烃中完全分离结合水。参照图4,按照本发明的可替代性实施方式,示出了用于预处理废油的工艺400。废油流402具有大于10,000PPM的烃含量。在这一替代性实施方式中,废油供给流402优选包含水,其具有盐,固体和有结合水或无结合水的有限的烃。将废油供给流402发送至第一沉降槽或相分离柱404,其中优选形成三层,即顶层406,中间层408和底层410。顶层406优选包含自由流动烃,有盐或无盐,以及微量的水和固体。中间层408优选包含烃,具有大量水,有盐或无盐和固体。底层410优选包含水,具有盐,固体,有限的烃,其沿着管线-B。在这一替代性实施方式中,底层410是废油,具有小于10,000PPM的烃含量。如果顶层406不包含任何微量的盐,顶层406通过管线411直接存储在产品存储槽412。或者,如果顶层406包含盐,任选地,可以经由管线F将顶层406供给到第三脱盐设备218(参照图2),随后添加预定量的明矾。第二沉降槽414形成第一层416,第二层418和第三层420。在这一实施方式中,第一层416优选包含自由流动烃,具有盐或不具有盐和微量的水和固体,其与顶层406混合。第二层418主要包含有明矾和水,水具有盐,固体,有限的烃。第二层418与底层410混合以沿着图示的线B。第三层420是含烃,明矾,盐,固体和水在其中的凝胶状含油层。第三层沿着线H。在此应当理解,在第二沉降槽414中加入明矾有利于通过凝固快速分离烃和凝胶状含油层的形成。第一沉降槽404有时可能产生馏分422,其可以包含粘稠烃,具有或不具有盐/固体/结合水。如果馏分422包含盐和结合水两者,任选地,经由管线I将馏分422供给到第一脱盐设备212。如果馏分422中包含盐而无任何结合水,通过与线A混合,任选地将馏分422供给到第二脱盐设备228。如果部分422中仅包含结合水,而无任何盐,任选地,馏分422与上游流体213混合。如果馏分422中仅包含固体,而无任何盐和结合水,任选地,可以经由管线423将馏分422发送至第三离心机424。将预定量的溶剂加入到第三离心机424,以将馏分422分离成两层,即顶层426和底层428。第三离心机424降低了在烃颗粒上的阻力和表面电荷,从而减少了平均自由路径,并允许在环境温度下颗粒的聚结。顶层426优选包含烃和具有微量的固体的溶剂,经由管线J将其发送至第一加热容器320。在这一实施方式中,底层428优选包含涂覆有烃的固体,其沿着线K。然而,如果底层422无盐,固体和结合水,底层422可以经由管线429直接存储为产品430。参照图5到6,根据本发明,示出了用于废油处理的沿着线B的工艺500。废油流502优选具有高浊度,和小于10,000PPM的烃含量。在这一实施方式中,废油流502优选包含水,其具有盐,固体和有限的有结合水或无结合水的烃。将废油供给流502供给到第四离心机504以降低浑浊度并获得具有低浑浊度的流506。第四离心机504是多程分离机,只要烃的超细颗粒的分布密度高,因为这样平均自由路径低,其独立地工作。因为,在它们聚结之后,可以除去超细颗粒,为了聚结,在粒子之间必须有相对运动。这仅是由于相对粒子分布。在小颗粒的高密度区这种分布是非常狭窄的。在此应当理解,多程分离机504必须以新鲜废油开始。另外,可以理解,在废油生成和离心机504的操作之间的间隙应该尽可能最小。另外,可以理解,第四离心机504使用高G带来的相对运动直到这样的时间,以致烃颗粒之间的平均自由路径增加到超出它们的最大容量。将具有低浑浊度的流506供给到高速剪切混合器508,其中经由管线510加入预定量溶剂,从而形成混合物512,将其供给到第五离心机514。溶剂的加入,随后通过高速剪切混合器,在约8000至10000RPM的范围内,允许适当大小溶剂颗粒的形成,优选在0.5至0.8微米大小的范围内,其分布密度显著量增加。可以理解,为了溶剂的充分崩解,存在最佳混合时间,约为1分钟。进一步增加混合时间可以导致粒度增加和浑浊度下降。溶剂的正确粒度优选除去几乎相似大小的超细油颗粒。此后,聚结速度增加,按照本发明,这被证明是速率控制步骤,其中聚结的作用在第五分离心机504的工作范围内延伸。此后,由于分布密度高,分离机503开始工作,并持续直到分布密度下降到早先水平。这有效地允许油颗粒完全出去。此外,溶剂的加入有利于聚结,通过具有增强的清扫效果增强了离心机504的效率,离心机504的限制因素细液滴的分布密度是由溶剂的液滴达到的,而不是油滴。在高速剪切混合器508中加入溶剂提高了废油内的分布密度,使得第五离心机514有效地允许溶剂促进聚结,从而移动烃颗粒以从底部移动,并用清扫影响分离。在高速剪切混合器508中加入大量溶剂,允许用溶剂液滴替换烃液滴,用于用其中的溶剂替换油。第五离心机514优选形成两层,即顶层516和底层518。顶层516是溶剂占主导的烃层,优选包含溶剂,有结合水或无结合水的烃,有限的游离水,有限的盐和有限的固体。底层518是水占主导的烃层,优选包含水,有限的溶剂,有限的烃,盐,浑浊度值很高的固体。对将层516进行BTX研究520以了解水和灰分含量,用于确定溶剂需要与否。如果顶层516含烃,其中具有结合水,则经由管线524将顶层516加入到第三加热容器522。或者,如果顶层516包含烃,其中没有结合水,则通过管线528将顶层516加入到第四加热容器526,。在本发明的其它实施方式中,第三加热容器522可以是多效蒸发器,具有热蒸汽再压缩,消泡器和夹带抑制器。在这一实施方式中,第三加热容器522优选在大气压下和在约70℃至150℃的温度范围操作。基于BTX研究520,将预定量的额外溶剂加入到第三加热容器522。将预定量废热施加到第三加热容器,用于提高第三加热容器522的的温度和形成两相,即蒸汽相530和液相532。液相532中优选包含烃,残留的溶剂,有限的固体和有限的盐。蒸汽相530中包含蒸汽,其具有一部分溶剂,全部结合水和游离水。通过管线538将蒸汽相530供给到冷凝器536。冷凝器536从蒸汽相530中除去热量,随后通过冷凝/分相器540进行处理。冷凝/分相器540优选形成第一层542和第二层544。第一层542包含纯净水,其可以在工艺中重复使用或包装后出售。第二层544包含溶剂,通过与溶剂管线510混合,其可以在工艺中重复使用。液相532不含结合水,随后通过管线534将其加入到第四加热容器526。第四加热容器526在大气压下和在约90℃至105℃的温度范围操作。如图所示,将预定量溶剂流G(参照图6)加入到第四加热容器526。加热容器526产生蒸汽相546和液相548。液相548包含全部剩余溶剂和一部分游离水。液相548包含烃,剩余游离水,有限的固体,有限的盐和明矾。经由管线550将蒸汽相546加入到了冷凝器536。将液相548供给到第六离心机552。在这一实施方式中,第六离心机552是热离心机或热沉降槽,其在大气压下和在等于或小于95℃的温度下操作。第六离心机552优选产生两层,顶层554和底层556。顶层554是烃产品,其具有微量的水,盐和固体。将顶层554储存或包装出售。底层556包含水,有限的盐,有限的固体和明矾。通过反渗透装置558处理底层556以获得纯净水流560和废料流562。纯净水流560与第一层542混合。在这一实施方式中,废料流562沿着管线-H。将底层518供给到第五加热容器564,其在大气压下和在约90℃至105℃的温度范围内操作。为第五加热容器564提供废热以达到所需的温度范围。第五加热容器564产生蒸汽相566和液相568。蒸汽相566优选包含溶剂和部分水的蒸汽,如图所示,其通过冷凝器536进行进一步的处理。液相568优选包含剩余的水,有限的烃,盐和固体。液相568具有相当低的浑浊度,其沿着图示的管线-E。如图6所示,将沿着管线-E的液相568供给到第三沉降槽602,其中添加预定量的明矾流604。优选添加明矾流604以降低液相568的浑浊度,并降低其到低于2.0NTU。第三沉降槽602可以任选地提供有热量,以在热条件下促进明矾处理。在加热条件下,在80℃至90℃的范围内的温度下添加明矾至少四小时,可以降低废油的浑浊度至少90%。明矾流604的添加在加热下更有效,允许液滴的更广泛分布模式,其首先允许油颗粒彼此附着,并形成凝胶。在此应当理解,明矾流604的添加的效力不受离子可用性的限制,因为是动力学问题。沉降槽602优选形成两层,即顶层606和底层608。顶层606是水占主导的明矾层,其中优选包含水,明矾,固体,盐和微量的烃。底层608优选是凝胶含油层,其中包含烃,明矾,水,固体和盐。然而,在此应当理解,在本发明的其它替代性实施方式中,可以在顶部或既在顶部又在底部收集浮渣,这取决于ppm级。将顶层606发送至过滤装置610,其将顶层606分为滤液流612和残留物流614。残留物流614优选包含固体,具有微量的烃,盐和明矾。残留物流614通过管线616与底层608混合。滤液流612优选包含水,明矾和盐。为了获得纯净水流620,如果滤液流612的总溶解固体(TDS,下同)高,则通过管线617将滤液流612发送至反渗透装置618。如果液流612的总溶解固体低,则经由管线622直接存储或包装出售。在此应当理解,在第三沉降槽602中添加明矾提高了在过滤装置610中的过滤速率,从而基本上降低浑浊度到低于2NTU。沿着管线-H,底层608与第三层420混合(参照图4),并将其传送至第一热干燥器624。第一热干燥器624优选在大气压下和在约108℃的温度下操作,其将水沸腾为水蒸气流626形式,从而保持粘稠液体流628,其包含烃,明矾,固体和盐。将粘稠液体流628供给到搅拌器/脱油装置630。将预定量的溶剂流连同底层428(参照图4)加入到搅拌器/脱油装置630,底层428沿着管线-K并包含涂有烃的固体。搅拌器/脱油装置630产生自由流动液体流632,其优选包含溶剂,具有烃,明矾,盐和脱油固体。通过管线633将自由流动液体流632传送至第七离心机634。然而据了解,在本发明的其它替代性实施方式中,第七离心机634可以是分相器。第七分离机634优选产生三层,即第一层636,第二层638和第三层640。第一层636优选包含溶剂和烃,通过管线-G将其添加到加热容器526(如图5所示)。第二层638是水占主导的明矾层,其优选包含水,具有明矾和盐以及有限的溶剂。将第二层638供给到第六加热容器642,其在大气压下和在约90℃至105℃的温度范围内操作。第六加热容器642产生两相,即蒸汽相643和液相644。液相644中优选包含水,明矾和盐包含。经由再循环管线646将液相644再循环到反渗透装置618。蒸汽相643优选包含溶剂和水的蒸汽。为了除去热量,将蒸汽相643传送至冷凝器648,然后通过冷凝/分相器650进行处理。冷凝/分相器650优选形成第一层652和第二层654。第一层652包含纯净水,其可以在重复使用或包装出售。第二层654包含溶剂,其可以在工艺中重复利用。第三层640优选包含具有溶剂,有限的盐和有限的明矾的湿脱油固体的滤渣。将第三层640传送至第二热干燥器656,其在大气压和约200℃的温度下操作。将预定量废热施加到干燥器656以达到预期温度。第二热干燥器656处理第三层640,从而除去蒸汽流658,从而形成残留物流660。蒸汽流658优选包含包含在其中的溶剂和水的蒸汽。残留物流660优选包含具有微量的明矾和盐的干脱油固体。如图所示,蒸汽流658与蒸汽相643混合,并通过冷凝器648进一步处理。参照图4至图6,在运行中,工艺400和500有利地将污染物转化为有价值的产品流,从而减轻环境污染和环境损害的问题。此外,工艺400和500有利于油和有价值水的最好的可能的回收,其中水可以以低于污泥/废油存储成本的成本,用作商业用途的饮用水。工艺400和500有利于用于回收油的化学品的使用,以至于使用的化学品在工艺中全部循环使用和重复利用。另外,本发明的方法通过利用在整个工艺中的废热以几乎为零的能源成本运行。具体实施方式提供了下列实施例和对比例用于说明本发明的具体实施方式。在实施例和对比例中的方法应该为本领域的技术人员所理解,下面仅表示本发明示范性实施方式。本领域的技术人员根据本发明公开的内容,应该理解对描述的具体实施方式中可以进行改变,并且在不脱离本发明的精神和范围的情况下仍然获得相同或类似的结果。实施例1表1.1-实验室用油的说明SI号说明炉油柴油1按每BTX在烃中的水重量百分比0.210.012油的热值(kcal/kg)10,17311,0023在油中灰分重量百分比0.230.00表1.2-炉油污泥的制备表1.3-柴油污泥的制备污泥/乳状液的制备,用于后续除去结合水和游离水使用粘稠/非粘稠烃用水制备预定量的内部污泥,为了理解污泥,也用于后续从其中除去全部结合水。因此,如果存在,称重的水,烃和作为乳化剂的十二烷基硫酸钠混合,并使用高速剪切混合器以10,000rpm搅拌1分钟,并进行5次,同时确保混合材料的温度绝不超过58℃。在每1分钟混合后,冷却材料到接近环境温度。接着,在分批式离心机中,以21,893相对离心力(RCF)进行连续离心代表性样本10分钟,以发现是否分离出了任何水。如果是,那么它被认为是废油。剩余的材料被认为是具有结合水的污泥。如下表1.2和1.3所示,制备了不同类型的污泥。可以理解的是,具有结合水的污泥意味着其中没有游离水明显地出现,即使在RCF峰值处以21,893RCF分批离心10分钟。使用粘稠炉油但不使用自由流动柴油制造污泥,而无需使用外部乳剂,如十二烷基硫酸钠(SLS)。据观察,由于粘度的阻力对烃紧紧抓住细水滴来说是一个重要原因。据观察,对于柴油,十二烷基硫酸钠的使用是必要的。即使这样,如可以从表3中看出,只有存在的总水的5.96wt%可以结合到柴油,而当使用2.43wt.%十二烷基硫酸钠时,82.64wt%的柴油可以结合到水,从而形成45.18wt%污泥。还可以观察到,可以使用十二烷基硫酸钠制备污泥,均有炉油和柴油。然而,具有同样数量的水,具有结合水的柴油污泥的量接近于用炉油获得的污泥的一半。进一步观察到,随着十二烷基硫酸钠的存在,在污泥中炉油保持水的能力急剧恶化。这是因为随着十二烷基硫酸钠的使用,污泥变得十分不粘稠。这表明,由于粘度,烃和水之间的结合和十二烷基硫酸钠的使用并没有增加。换言之,它们对于结合烃和水的贡献不叠加。另外,据观察,随着十二烷基硫酸钠的使用,具有结合水的污泥的量下降。这是因为现在只有四分之一的水存在,其参与了与炉油的结合。然而,据观察,结合的强度比在没有十二烷基硫酸钠的情况下的可能的强度要强很多。从表1.2中观察到,在污泥号5中,在污泥产生之前,将十二烷基硫酸钠添加到水中。而在污泥号6中,将十二烷基硫酸钠添加到已经用49.75wt%水制备的污泥中。从这个表中可以观察到,在产生污泥之前,当十二烷基硫酸钠均匀地溶解于水时,水与烃之间的结合稍强。据观察,炉油基于其粘性可以抓住多少结合水上有上限,其中可以从表2中清楚看到,通过剧烈混合不能让炉油保持全部水作为结合水,其超过水的自身重量的1.5倍。另外,据观察,炉油可保持水作为结合水仅达其自身重量的67%至82%,超出了阈值。此外,随着增加水含量,发现用结合水形成的污泥的量急剧下降。据观察,剩余的水作为游离水停留,游离水中具有微量的烃。这就是所谓的废油。如可以在后面的表4.3中的样本2至4中看出,尽管经混合使用炉油很难产生新鲜污泥,其中具有超过60至62wt%结合水,但后来通过从已经制备的污泥中使用溶剂与离心机除去一部分炉油,人们总能保留80wt%以上的结合水在炉油污泥中。最后,它从根据在其中的水含量的比例,污泥的热值恶化中观察到的。实施例2使用离心机预处理进来的污泥/乳状液目的在于确定存在于进入污泥中的结合水的程度,从而通过离心机将其分为具有结合水的污泥和废油。此外,目的是建立单独用间歇式离心机回收增值的可销售烃;除去一部分存在的水和也减少污泥的量是可能的,污泥需要进一步的处理。因此,在间歇式离心机中以具有不同停留时间的4,500和21,853RCF处理在内部制备的污泥和从印度石油天然气公司(ONGC)采购的泻湖污泥,从而在那之后分离和称重馏分,然后对离心的材料进行质量平衡。此外,通过BTX方法评估这些馏分的水分含量,然后是通过在马弗(muffle)炉中加热评估灰分含量,随后使用弹式热量计评估热值,使用哈希(Hach)浊度仪评估出来的游离水的浑浊度。下面的表2.1至2.8,提到了制备的污泥中的成分,和这些污泥的离心条件。表2.1-在炉油污泥样品中的成分表2.2-离心详细说明表2.3-在离心机中炉油污泥的预处理结果基于柴油的污泥表2.4-在柴油污泥样本中的成分表2.5-离心详细说明表2.6-在离心机中柴油污泥样本的预处理结果进来的泻湖污泥表2.7-离心详细说明表2.8-在离心机中ONGC污泥样本的预处理结果可以观察到,对包含高达61wt%水的炉油污泥无影响,同时在21,893的RCF的峰值处用10分钟停留时间离心污泥,只要污泥不含有如十二烷基硫酸钠的乳剂。取回全部污泥,预期有东西会粘附到离心瓶的壁上。这可以从表2.3看出,对于具有50wt%水的污泥,热值没有上升。然而,一旦污泥中水的重量百分比超过一定的阈值,其值位于61至70之间,则即使没有十二烷基硫酸钠,如果在RCF的峰值以21,893RCF离心炉油污泥10分钟,就会发现其被分为具有结合水的污泥和废油。可以观察到的,如果污泥具有70wt%水且没有十二烷基硫酸钠,那么就会发现它可这样划分成53wt%污泥含有44wt%的水,且全部水是结合水。发现剩余的材料是废油。另一方面,可以观察到,如果炉油含96wt%水且没有十二烷基硫酸钠,然后在21,893的RCF峰值对其离心10分钟,就会发现污泥这样分成,即只有其中的6wt.%形成了具有40wt.%水的污泥,全部水会是结合水,剩余材料主要作为废油。还可以观察到,超过70wt.%的水,随着提高含水量,产生少量的其中具有结合水的污泥。然而,据观察,在污泥内的结合水的量变化不大。此外,可以观察到,相对于较少的污泥产量,获得更多废油。此外,可以观察到,具有96wt.%水的炉油污泥具有320kcal/kg的热值。然而,在21,893的RCF峰值离心污泥10分钟,产生了6wt.%的污泥,而且该污泥中具有19倍以上的能量密度,热值为6,130kcal/kg。这里通过对其离心分离出了污泥重块,其中能量比废油相对集中,废油中具有非常少的能量。此外,可以观察到,在污泥中使用如十二烷基硫酸钠的乳剂并以21,893RCF离心炉油污泥10分钟,与没有使用十二烷基硫酸钠的类似污泥相比,产生了更少量的具有结合水的污泥。然而,使用十二烷基硫酸钠的污泥质量更好,因为它具有较高的热值,更少的水含量。这里,离心机通过从污泥中挤压出水再次产生了重要性。这可能仅仅是因为十二烷基硫酸钠的存在,由于其粘性,部分降低了污泥保持水的能力。然而,可以观察到,SLS有助于使离心机有效,没有十二烷基硫酸钠,离心机对污泥没有影响。另外,可以观察到,只有当污泥中使用如十二烷基硫酸钠的乳剂时,以21,893RCF离心柴油污泥13分钟重要性增加。这只有在水结合到柴油时是可能的。然而,没有使用十二烷基硫酸钠时,发现将水从柴油中分离,不会形成污泥。但是一旦十二烷基硫酸钠存在,离心能够将87wt.%柴油浓缩为具有6.44wt.%水的污泥,从而污泥的能量密度立即增长了将近一倍,高达10,160kcal/kg,这是纯柴油能量密度的92%。另外,可以观察到,关于使用十二烷基硫酸钠的柴油污泥,通过离心增加的重要性取决于提供的停留时间和选择的RCF峰值。这里发现离心的累积效应是一个辅助因素。可以观察到,随着以3,502的RCF离心使用十二烷基硫酸钠的柴油污泥10分钟,发现挤压出的水较少。因此,发现产生的污泥的量从45wt.%增加到66wt.%,同时能量密度的增加从84%降至29%。这可以从表2到表6看出。可以观察到,没有使用十二烷基硫酸钠,就没有柴油和水之间的结合。离心机迅速分离柴油和水,从而在一端提供纯柴油。然而,有十二烷基硫酸钠存在,运送的柴油不是完全的不含水。因此到那种程度,从离心机的角度来看,发现十二烷基硫酸钠在含有炉油的污泥的情况下起辅助作用,而在含有柴油的污泥的情况下起阻碍作用。因此,对于柴油污泥,确认间歇式离心机可以破坏在水和柴油之间的基于乳剂的键。通常不期望离心机除去结合水。然而,随着使用更高的RCF值、增加的停留时间,键断裂更为明显。可以观察到,看到用离心机预处理污泥的最好效果在ONGC泻湖污泥中观察到,可以从表2.7和2.8看出。这里,观察到,人可以提高污泥的商业价值,通过提取污泥,其41wt.%可售,自由流动烃含有10,633kcal/kg热值,0.88wt.%灰分含量和0.39wt.%的水分含量。此外,可以观察到,人们可以减少需要进一步处理的污泥的重量,获得三倍多的相应的好处。此外,可以观察到,随着停留时间和RCF数值的增加,可以挤出更多的水。还可以观察到,污泥预处理有助于降低烃中的盐含量和灰分含量。可以观察到,仅离心不能从污泥除去全部的水。可以观察到,离心增强了重力所致的加速度,这是通过大力加速天然发生的由其密度差异所造成的两种不同的不相混合的液体的分离。可以观察到,当特定液体的小液滴之间的平均自由路径较小时,离心有促进作用,随后将小液滴凝聚为更大的液滴,阻力减小,其有助于液滴移动更快。此外,可以观察到,改变移动液滴之间的加速度导致了在给定时间内更大数量的碰撞,因此更快的凝结,然后建立连锁反应。此外,随着停留时间增加,两种不同液体的液滴不断集中动能,同时朝着相反方向移动。一旦它们之间的动能差超过阈值,那么它们就能打破将这些液滴结合在一起的力,从而影响它们之间的永久的分离,否则用以类似RCF允许的在线离心机是很难实现的。因此,确定了来自ONGC的泻湖污泥的成分之间的分离。此外,可以观察到,尽管事实是在离心时,块状粘稠烃在游离水出现之前出现,但是可以在具有结合水的不渗透的,粘稠的层后面从ONGC污泥收集游离水。最后,可以观察到,泻湖污泥的成分并不随时间自然分离,甚至在数十年之后,其中键断裂量取决于离心机的操作RCF和污泥在离心机内的停留时间。实施例3使用二甲苯作为溶剂对具有结合水的污泥的效果通过在室温和高温下添加不同数量低粘性溶剂,如二甲苯,降低污泥的粘性,研究随着时间推移从污泥中释放结合水的影响。此外,人们发现水如何被烃仅仅抓住的。因此,将约58wt.%和200wt.%的二甲苯加入到粘稠炉油污泥,粘稠炉油污泥不含有内部制备十二烷基硫酸钠,而具有50wt.%结合水。可替代地,将约58wt.%和200wt.%的二甲苯加入到粘稠炉油污泥中,其具有20.47wt.%结合水和3.74wt.%十二烷基硫酸钠,该污泥是通过以21,893RCF离心10分钟,从在内部的具有47.5wt.%水和2.51wt.%十二烷基硫酸钠的污泥中提取的。此外,将58wt.%和200wt.%的二甲苯加入到粘稠ONGC污泥,其具有42.21wt.%结合水和8.61wt.%灰分,其是通过以4,500RCF间歇离心进来的ONGC泻湖污泥10分钟回收而来。随后,将混合物充分搅拌,并一口气将一部分低粘稠混合物在约28℃至32℃的环境温度下保存在沉降槽中6至72小时,同时将另外一组样品在80至85℃下在水浴保存6小时。在测试期结束时,去除来自沉降槽的顶部,中间和底部的材料馏分,并使用BTX方法评估水含量。接着,对存在于各种水平的水与全部混合物的平均水含量进行测量。而最顶层常常是几乎不含水的,没有发现在最底层收集到游离水或废油。最底层是类似于中间层的组合物,因此在表3-2,3-4,3-6和3-9中加入相同的物质。表3.1-在炉油污泥加二甲苯混合物中的成分表3.2-在无乳剂、具有37wt.%二甲苯的炉油污泥中的测试结果表3.3-具有37wt.%二甲苯、无乳剂的炉油污泥中不同材料层的水重量百分比研究表3.4-66.5wt.%二甲苯对无乳剂的炉油污泥的影响表3.5-具有66.5wt.%二甲苯、无乳剂的炉油污泥中不同材料层的水重量百分比研究表3.6-66.5wt.%二甲苯对具有乳剂的炉油污泥的作用表3.7-具有66.5wt.%二甲苯和无乳剂的炉油污泥中不同材料层的水重量百分比研究表3.8-在ONGC污泥加二甲苯的混合物中的各成分SI号说明样本1具有结合水的污泥的重量(g)438.662由BTX确定的上述污泥中结合水的重量百分比42.213污泥中的灰分重量百分比8.614加入并混合上述污泥的二甲苯重量(g)882.715最终混合物中的二甲苯的重量百分比66.806上述具有二甲苯的污泥中水的重量百分比14.017为处理制备的污泥和二甲苯混合物的总量(g)1,321.37表3.9-ONGC污泥中66.5wt.%二甲苯的影响表3.10-具有66.5wt.%二甲苯和无乳剂的ONGC污泥中不同材料层的水重量百分比研究在之前的实施例1中,可以观察到,将外源乳剂、如十二烷基硫酸钠加入相对于其中的总水量包含有高达61wt.%%水到炉油污泥中时,作为结合水由炉油容纳的水量从100%下降到十分低的水平。对于其中具有48至49wt.%水的污泥,当添加的十二烷基硫酸钠为2.4至2.5wt.%时,我们发现仅有25-23wt.%水存在于污泥,其作为结合水保持粘在炉油上。但随后仅以21,893RCF离心污泥10分钟后,对其进行测量。然而,按照本实施例3,以21,893RCF离心其中具有47.52wt.%水和2.51wt.%十二烷基硫酸钠的炉油污泥10分钟,收回了粘稠污泥,其中含有20.47wt.%结合水和3.74wt.%十二烷基硫酸钠。对仅取具有20.47wt.%结合水的粘稠污泥进行处理。在之前的实施例2中,可以观察到,在以21,893RCF或甚至以4,500RCF间歇式离心进来的NOGC泻湖污泥10分钟时,污泥分离为三种不同层,而中间层是其中具有30wt.%结合水的粘稠污泥。当RCF仅为4,500时,中间层中具有42.2wt.%总水量,而其中只有72wt.%是结合水。然而,按照本实施例3,据评估,在以4,500RCF离心进来的ONGC污泥10分钟后,中间层中产生了42.21wt.%总水量。换言之,仅将作为溶剂的二甲苯加入粘稠污泥,其中除了ONGC污泥,全部水是如此紧密结合到烃,即使在以21,893RCF离心10分钟时,也没有水分离出来。也观察到,以这一高RCF值,ONGC污泥只分离出28wt.%的水。因此,可以观察到,二甲苯大大降低了所得混合物的粘性,特别是当其加入的二甲苯的量是污泥的两倍时。此外,在80℃至85℃下加热所得混合物,以进一步降低其粘度。除了立即降低粘性,认为二甲苯提高了不混溶烃与水之间的密度差。然而,可以观察到,没有游离水或废油可以分离出来,甚至是在等待六小时之后;因此,可以确认,粘度不是烃容纳如此大量的水唯一原因。如表3.1所示,可以观察到,混合物甚至平均容纳31.27wt.%水。可以观察到,分散水滴大小是如此微小,以至于粘度立即降低,而密度差缓慢提高。然而,它们所经历的阻力保持太高以至于不能使它们快速分离。此外,可能是因为分散的水滴尺寸如此小,以至于尽管以这样大的RCF保持离心操作10分钟,不混溶的水仍然不能从烃中分离出来,即使当水以高达50wt.%.的量存在。为了评估随着时间加入二甲苯到污泥对结合水向下渗透的影响程度,表3.3,3.5,3.7和3.10横向读取为最顶层,中间层和最底层。因此,据观察,超出阈值的二甲苯的添加是必不可少的,以对炉油基污泥产生很大影响。据观察,对于为炉油基污泥添加的不同量的二甲苯,只有当水以66wt.%的水平存在于最终混合物中时,二甲苯是有效的,并且当水的存在限制在37wt.%时,二甲苯的益处被减弱。据观察,甚至是最顶层也不是任何地方都接近无水的,具有37wt.%二甲苯存在于混合物中。另外,可以观察到,底部没有收集游离水或污水,但是在最顶层收集了几乎无水的烃。除了在最底层收集更大量的水的事实,表明水滴实际上随着时间非常缓慢地向下移动。非常缓慢的水向下渗透的速度可能是因为乳剂的存在或由于分散水滴的超小尺寸。因此,经确定,水和烃之间的密度差减少了,这反过来又在水结合到油的情况下,由于乳剂降低了浮力的力。因此,可以确认在乳剂存在的情况下,在最底层的水的浓度不能超出在没有乳剂的情况下可能存在的水的平均浓度,其中其它物质保持不变。此外,可以观察到,如果防止冷凝水蒸汽滴回到最顶层,或如果防止回归水蒸汽自身的冷凝,使用二甲苯额外加热,在约6小时中可以得到无水最顶层,甚至从具有高水含量的污泥中。但如果乳剂存在于污泥中,为此需要的时间将更长。另外,只有一部分无水烃可以因此从污泥中释放。此外,可以观察到,温度对混合物有两个影响。首先,除了进一步降低混合物的粘度,温度增强了最顶层的水的蒸发速率。再次,后者具有两层含义。首先,它有助于减少在最顶层中的水。第二,它增加了冷凝的速率。部分我们的沉降槽超出在上述水浴中的水位。因此,沉降槽的顶部相对较冷,从而可以迅速凝结。就这样,冷凝水滴迅速滴回到最顶层。这反过来又解释了为什么在顶层有更多的水,如图3.5,3.7和3.10所观察到的。另外,可以观察到,通过不允许沉降槽的顶端保持在水浴中以冷却除了获得非常干燥的最顶层之外,还可以防止出现水蒸汽。通过修改我们沉降槽自身的设计,也可以实现防止冷凝水滴回到最顶层。可以观察到,随着减少二甲苯,如在表3.5,3.7和3.10中看到的混合物中相对较高的粘度,在表3.3中不重复出现。据观察,它可能对蒸发的速率产生不利影响。可以看到,当存在于混合物中的二甲苯限于37wt.%时,则只有2.39wt.%的混合物通过水蒸气的方式蒸发。然而,当存在于混合物中的二甲苯升至66.5wt.%,则约4.63wt.%的混合物通过水蒸气的方式蒸发。因此,可以确认,随着较少的蒸发,有更少的冷凝,因此较小伤害是通过冷凝完成的。这可以通过比较表3.2和3.4来确定。此外,在表3.3中,最顶层由仅6.12wt.%的总混合物组成,相比于表3.5中的9.07wt.%,在表3.5中使用了更多的二甲苯。如可以从表3.3中看出的,通过考虑更薄层,在最顶层有较低的水分。然而,在十二烷基硫酸钠存在的情况下,观察到了非常低的蒸发速率,尽管降低了同样大的粘度。这是因为,当水通过乳剂结合到烃,在给定的压强下它的沸点变高,这样,在给定温度下蒸发速率连同冷凝率下降了。因此,可以观察到,当水通过乳剂结合到烃,可以或不可以结合全部水或烃。因此,水和烃之间分离的过程变得缓慢和不完全,而没有完全停止。因此,当乳剂存在时,观察到任意层与平均水含量的偏差都小于无乳剂时的偏差。这也可以从表3.5和3.7中证实。对ONGG污泥的一个重要发现是,即使在通过添加两倍于自身重量的二甲苯极大降低ONGG污泥的粘度后,在环境条件下,对存在于ONGG污泥中的结合水的向下渗透也几乎没有影响。如从表3.10可以看出,甚至在等待72小时之后,当混合物的总含水量为14wt.%.时,在最底层中的平均水含量上升到16wt.%。相反,对于炉油污泥,当加入两倍于自身重量的二甲苯时,平均水含量变为16.67wt.%。但在等待72小时之后,在底层的水上升至69wt.%,将近是四倍之多。然而,关于ONGC污泥,额外的热量产生巨大的影响,尽管没有和关于炉油污泥看到的一样大。还可以观察到,溶剂,即使当大量加入时,它没有迅速和选择性溶解存在于污泥中的全部烃,然后由于通常认为的密度差,排出了不混溶的水。然而,仅仅发现削弱了将水与烃结合在一起的力,到通过缓慢溶解少量的烃缓慢提高烃和水之间的密度差促进的程度。这当然不是完全或立即消除结合水与烃的力。实施例4离心机和溶剂对具有结合水的污泥的组合影响为了理解该机制和对从烃中释放结合水的影响,首先降低了粘稠污泥的粘性,然后添加溶剂,使得混合物包含67wt.%溶剂,随后以4,500RCF在约28℃至32℃的环境温度下离心混合物10分钟进行研究。具体来说,将溶剂如二甲苯和甲苯加入在内部制备的具有50wt.%水的粘稠炉油污泥中。或者,将溶剂如二甲苯和甲苯加入粘稠炉油污泥,其具有20.47wt.%结合水和3.74wt.%十二烷基硫酸钠,是通过以21,893RCF离心10分钟,从在内部的具有47.5wt.%水和2.51wt.%十二烷基硫酸钠的污泥中提取出来的。或者,将溶剂、如二甲苯和甲苯加入具有42.21wt.%结合水的粘稠ONGC污泥中,其回收自以4,500RCF间歇离心进来的ONGC泻湖污泥10分钟之后,使得混合物包含67wt.%溶剂,然后在立即搅拌它后,以4,500不停离心10分钟。离心的过程产生了两个或三个不同的液体层。只有在ONGC包含清水的情况下,才能获得第三层。最顶层总是无水。它含有大量加入的溶剂,也包含大量从污泥中释放的烃。在获得三层的情况下,中间层包括烃和水。接着,评估中间层。在以21,893RCF离心中间层10分钟时,我们得到了具有结合水的污泥,溶剂加一些溶解的烃的自由流动层和略带颜色的废油,尽管在结合水数量上小得多。然后使用BTX评估如此获得的污泥的结合水,使用弹式热量计评估热值。具有结合水的炉油基污泥表4.1-炉油污泥的说明表4.2-离心详细说明SI号说明样本1样本2样本31达到最大时相对离心力所花费的时2.652.702.65间(min)2运行的最大相对离心力4,5004,5004,5003最大相对离心力的保持时间(min)1010104回到零相对离心力所花费的时间1716.516.55离心机内的总停留时间(min)29.6529.2029.15表4.3-分离与溶剂对炉油污泥的组合效果具有结合水的ONGC粘稠污泥表4.4-ONGC粘稠污泥的说明表4.5-离心详细说明表4.6-离心与溶剂对ONGC污泥的组合效果可以观察到,将溶剂与离心机结合比仅仅加成它们的各自的影响大。例如,以21,893RCF对其离心10分钟之后,无乳剂而有50wt.%结合水的炉油污泥不可以除去任何水或油。随后,通过加入类似量的同样溶剂,在等待6小时之后,我们在具有0.31wt.%水的最顶层中,仅仅可以得到8wt.%的混合物。然而,在降低的RCF峰处以4,500RCF离心,即4.9倍,从而保持与在RCF峰值处时间同样的停留时间,有可能在无水的最顶层以仅仅30分钟的时间收集80wt.%混合物。这主要是因为通过结合溶剂和离心机增强了有助于增加浮力的力的因素,自然有助于分离两种不混溶液体。然而,另一方面,合并溶剂和离心机,降低粘性,抑制分离的阻力实质上降低。如可以从表4.1至4.3清楚看出,在具有乳剂如十二烷基硫酸钠的炉油污泥的情况下,最高的无水层的大小急剧缩水,从80wt.%缩水至50wt.%。这清楚的确定,当水通过乳剂额外地结合到烃时,即使溶剂和离心机的组合也是不太有效的。随着最顶层的收缩,中间层从20wt.%扩大到50wt.%,而这样做,其中具有结合水的污泥的存在从72wt.%提供到95wt.%。甚至更重要的是,在较高馏分的污泥内结合水从85wt.%下降到9wt.%,从而污泥的热值从1,520kcal/kg提高到9124kcal/kg。随着乳剂如十二烷基硫酸钠的存在,污泥中的烃成分略有上升,从76至87wt.%,而由于溶剂和离心的组合处理,其含水量下降,从20到9wt.%。但是,当十二烷基硫酸钠不存在时,使用同样的处理,污泥中的炉油成分从50wt.%下降到15wt.%,而其中的水含量从50wt.%提高到85wt.%。当十二烷基硫酸钠存在时,污泥的质量需要进一步的处理,实际上与在没有十二烷基硫酸钠的情况下,从55wt.%减少到57wt.%相比,增加了41wt.%。这基本上意味着,随着十二烷基硫酸钠的存在,由于一些水从污泥中移出,污泥中的烃含量的增加没有这么多,但因为更多溶剂进入污泥,而很少量的炉油离开了污泥。当十二烷基硫酸钠存在时,仅有2wt.%的存在于污泥中的炉油离开,并移动到最顶层,而25wt.%添加的二甲苯移动到污泥中,然而紧密结合到水。这里最顶层主要仅包括二甲苯,因此只有轻微着色。与此相反,在十二烷基硫酸钠存在的时候,约86wt.%的存在于污泥中的炉油移出到无水最高层,而无二甲苯移进。因此,只有在存在十二烷基硫酸钠的时候,二甲苯和离心机的组合有可能从污泥内部除去87wt.%的炉油。因此,确定了溶剂与离心机的组合效果。可以观察到,对于炉油污泥,发现使用甲苯作为溶剂与使用二甲苯同样好,除了以下事实,使用甲苯与二甲苯相比,发现污泥的质量收缩了约4.6wt.%,水含量减少3.3wt.%,从而其热值,从1,520提高到1,860kcal/kg。使用甲苯,还发现中间层包含少量其中具有溶解烃的溶剂。观察到甲苯除去85wt%存在于污泥中的烃以及34wt.%的水,二甲苯除去86wt.%烃以及存在于污泥中的87wt.%烃和26wt.%水。发现甲苯以相对更好的方式从污泥中提取水,而与甲苯相比,二甲苯似乎以稍微更好的方式提取烃。观察到ONGC污泥,溶剂和离心机的组合使用可以除去游离水,其浑浊度值在20NTU的范围内。在ONGC污泥的情况下,甲苯优于二甲苯,因为它降低了具有结合水的污泥的质量,降低系数为2.89,而二甲苯为2.51。同样,观察到,没有外源乳剂的炉油污泥的系数分别是2.48和2.30。因此,发现溶剂与离心机的组合可以更好地处理ONGC污泥。在ONGC污泥的情况下,发现甲苯降低了48wt.%的污泥中的烃含量,而二甲苯降低了46wt.%。没有外源乳剂的炉油污泥的相似数字分别是85wt.%和87wt.%。在ONGC污泥的情况中,发现甲苯降低了污泥中90wt.%的水含量,而发现二甲苯降低了79wt.%水含量。同样,对于无外源乳剂的炉油基污泥,发现甲苯降低了污泥中34wt.%的水含量,发现二甲苯降低了污泥中26wt.%的水含量。因此,可以确认,相比于无外源乳剂的炉油基污泥,在ONGC污泥的情况中,水含量更容易萃取。通过在底部收集的游离水也可以看出。当从污泥中除去水时,发现甲苯尤其更好。因此,优选甲苯用于ONGC污泥。另外,可以观察到,从污泥中除去结合水比从污泥中提取烃优选,因为从污泥中除去结合水提高了污泥的热值,而无需在溶剂中装载过多烃。然而,在从溶剂中分离烃之前,当溶剂具有较少的烃在其中时,可以重复利用溶剂。在ONGC污泥的情况中,有可能从其中含结合水的污泥中提取近50wt.%的烃,而当分别使用甲苯和二甲苯时,无需在最顶层装载超过8.5或9.5wt.%的溶剂与烃。这是因为大量释放的烃不是通过在最高无水层收集的溶剂溶解。实施例5与水纯共沸的研究进行研究,以理解和评估具有水的溶剂在933mbar的常压下的纯共沸沸点,如苯,甲苯和二甲苯,然后比较结果与来自文献的类似值。按一定比例在Dean-Stark装置的圆底烧瓶中放入预称取重量的溶剂和去离子水,然后在覆套炉中加热。将具有在6℃的冷却水的冷凝器连接到RB烧瓶,在那里冷凝溶剂和水的蒸汽。在接收器的底部放置了节流塞,其周期性地开启以定期收集冷凝物,并在分离烧瓶中分离它们之后,单独称量不混溶成分。使用数字式温度计连续纪录在RB烧瓶中接近底部的材料的温度。表5.1-使用溶剂的说明表5.2-933mbar下,溶剂与水的共沸点研究可以观察到,与水的最低共沸沸点应该是固定点。然而,观察到了小范围的沸点。可以观察到,尽管在我们这里的气压低,但平均得到苯最低共沸沸点6.05℃,甲苯最低共沸沸点9.55℃和二甲苯最低共沸沸点5.7℃,高于文献中报道的最低共沸沸点。这部分可能是因为,在RB烧瓶内没有搅拌器。在最低共沸重量比的情况下,观察到比文献中报道的高的值。据观察,对于苯,发现其高至3.3倍。对于甲苯,它最初高至1.43倍。对于二甲苯,它起初高至1.46倍。在苯的情况中,漂浮在水的溶剂的量是非常高的,因此,夹带也有望成为最大。可以观察到,随着水蒸气出现的溶剂的比率随着时间增加。这只对于苯和甲苯显著发生。另外,在RB烧瓶中的残留材料中溶剂与水的重量比逐渐变得远低于苯和甲苯的最低共沸点比自身。据推测,发现如果按重量以小于最低共沸点比的溶剂与水的比,使这些溶剂与水沸腾,那么发现每单位除去的水除去了更多溶剂。实施例6在具有或不具有结合水和游离水的炉油存在下上述共沸的研究为了更好地了解炉油存在下以及之后改变炉油在结合水和游离水存在下,各溶剂的沸腾情况,首先,将预定重量比的甲苯和炉油按比例加入RB烧瓶。随后,将苯、甲苯和二甲苯依次与含结合水的炉油基污泥称取。再将上述每种溶剂依次与含特定比例饮用水的炉油称取在RB烧瓶中。该RB烧瓶为Dean-Stark设备的一部分,用覆套式加热器加热。将装有冷却水的冷凝器接入RB烧瓶,冷却水温度为6℃。溶剂蒸汽和水蒸气在冷凝器中冷凝。接收容器底端有节流塞,以周期性地收集冷凝物并分别称量分离瓶中分离的各种不混溶的成分。用数字温度计实时监测接近烧瓶底部的材料的温度。表6.1在933mbar下,对各种溶剂在炉油存在下沸点变化的研究SI.号说明苯甲苯二甲苯1烧瓶中加入炉油的重量(g)-300.41-2RB烧瓶中称取溶剂的重量(g)-300.20-3初始溶剂/炉油重量比-1.00-4在933mbar观察到的沸腾温度范围(℃)-110.93-350.15-5结束时收集到的溶剂重量(g)-305.96-6因蒸发等的损失重量百分比-0.21-表6.2在933mbar,对各种溶剂在炉油和结合水存在下沸点变化的研究表6.3在933mbar,对各种溶剂在炉油和游离水存在下沸点变化的研究可以观察到,当甲苯和炉油以50:50重量比混合时,两者均为非极性,形成溶液。可以观察到,由于炉油的沸点在350℃左右,所以甲苯沸点从110.8℃开始上升。可以观察到,当沸腾开始时,甲苯优先沸腾出来,因为其沸点比炉油沸点低得多。甲苯逐渐被耗尽,沸点便连续上升。如表6.1所示。如表6.1所示,在气压933mbar下,从110.93℃时开始沸腾。海平面上,纯甲苯的沸点是110.80℃。沸腾于350.15℃终止,刚好是纯炉油的初始沸点。实际上,我们收集到的溶剂比我们加入的稍多,最后,一些炉油也蒸发出来。可以观察到,当将溶剂加入任何污泥中,以蒸馏出烃中的结合水时,除溶剂之外,另一种现象发挥着作用,降低了水的沸点,炉油粘度也极大降低,这有助于减弱炉油与结合水的作用力,反之亦然。可以观察到,结合水的熔点随自身粘度降低而降低。表6.2中可见,代替纯炉油,在含50wt.%结合水的炉油基污泥情况下,可以观察到,水与炉油的结合非常牢固,即使在21,893RCF下离心10分钟也没有水从炉油中分离。基于此,在91.2℃-108.86℃温度范围内,通过沸腾起始存在的69wt.%的甲苯,除去了所有结合水。甲苯和水释放的平均重量比为6.93。与纯水和甲苯混合液相比,朝着试验后期,一旦甲苯与炉油的比例下落低于某个特定值时,沸点升高。这是由于当甲苯溶解在炉油中时,炉油提高了甲苯的沸点,如表6.1所示。此外,由于溶剂溶解在炉油中,导致夹带减少,回流的溶剂与水的重量比从9.34降低到6.93(如表5.2所示)。同样地,对二甲苯而言,用35wt.%的二甲苯,脱掉了全部结合水。可以观察到,相对甲苯的脱水率0.30g/min,二甲苯的脱水率为0.33g/min甚至更好。此外,观察到的温度范围较大,约在96.33℃-136.28℃。这是由于,纯二甲苯的沸点比甲苯的高,如表5.1所示。有趣的是,可以观察到,最终沸点升高至接近纯溶剂的沸点。这有可能是因为,接近终点时,由于结合水的耗尽,RB烧瓶中残留物质变得与起始物料相同,如表6.1所示。这里,蒸馏出来的溶剂与水的重量比是1.92,比表5.2中所示的2.08低。可以观察到,在接近终点时结合水减少,温度有所上升。然而,优选多效蒸发器来蒸馏出烃类中的水和溶剂。多效蒸发器使得材料保持在部分或容器中,其中当沸点上升时环境压力以及绝对温度较低,这成功避免热裂解。可以观察到,对苯而言,用93wt.%的苯除去全部的结合水。经发现,苯对结合水的脱水作用是最弱的,每脱掉一单位的结合水需要82单位的苯(重量比)。苯是三种溶剂中脱掉结合水最慢的一种溶剂,但苯也有其优点,整个过程可以在80℃下完成。发现,这里的沸点范围为72.11℃-79.54℃。可以观察到,从纯水中蒸发出的苯与水的平均重量比为82.34,这比表5.2中显示的61.97要高。这里所说的水确实是结合水而非游离水。因此,由于苯脱去游离水的效果最差,需要更多的苯。当溶剂将结合水蒸馏出来时,接近终点时,脱去单位重量的水需要的溶剂的量随沸点增加急剧上升。同时,还观察到,所需溶剂量增加的部分原因是,溶剂蒸气在从炉油中蒸发前很难遇到剩余水份将其带出。也有可能的部分原因是最后的一点水与炉油结合最紧密。由于溶液中再也没有能够降低沸点的溶剂存在,而只有高沸点的炉油,所以沸点在接近终点时也会上升。溶剂降低熔点只能在更早时期发挥作用,这是因为已经没有水了。炉油基污泥中结合水被游离水取代的行为研究见表6.3。烧瓶中加入特定比例的饮用水和纯炉油以及溶剂,加入的水为过量的。可以观察到,相反所有的溶剂全部被蒸馏出来,沸点范围也低得多,留下了过量的游离水与炉油。并未发现游离水与炉油混合,用重力分离法将其去除。可以观察到,三种溶剂都在97℃-99℃温度范围被完全蒸馏出来。除了苯从86.7℃开始沸腾并上升至98.31℃。有趣的是,游离水将所有溶剂从炉油中蒸馏出来,最终沸点达到的是游离水的温度而不是溶剂的温度。当游离水将溶剂蒸馏出来时,蒸馏出来的溶剂与水的重量比比最低共沸点比低得多。这与用溶剂从结合水蒸馏出来的情形完全相反。当溶剂被全部或稍过量地去除时,仅有30wt.%的初始游离水残留,同时蒸馏出苯,对于蒸馏出甲苯来说,有43wt.%的游离水残留,对蒸馏出二甲苯来说,有53wt.%的水残留。如表6.3所示,蒸馏出来的溶剂与水的重量比几乎一致,例如,苯和甲苯的分别为2.26和2.38。去除甲苯时,有一部分水残留,这是因为去除甲苯需要的水更少。二甲苯脱去结合水更有效,而甲苯脱去游离水更有效。从高沸点烃类(如炉油)溶液中,用游离水去除溶剂的去除率比污泥中相同炉油,用相同溶剂对结合水的脱水率高得多。例如,二甲苯对炉油中结合水的脱水率为0.33g/min。而游离水去除炉油中二甲苯的去除率为1.76g/min。这是由于用二甲苯去除炉油中结合水时加热缓慢。这是考虑到各自的溶解性能,相比二甲苯和炉油的结合强度,水与污泥中炉油的结合更加紧密。此外,可以观察到,当炉油中仅有微量溶剂时,接近蒸馏终点时需要更多的水来去除一定重量的溶剂。这是由于,尽管溶剂在小于99℃时即可被蒸馏除去,但是炉油中存在极少的溶剂时,沸点接近炉油或达到350℃。据统计,发现当炉油中只有微量溶剂存在时,在相对体积大得多的炉油中,很难带出水蒸气以与其中的溶剂相遇。因此,可以确定的是,当烃溶液中存在诸如苯、甲苯、二甲苯溶剂时,向烃溶液中加入游离水可以大幅降低溶剂的沸点,同时大幅提高该烃的沸点。同时还可以确定的是,在炉油中可以通过改变混合物中水和溶剂的比例来选择性去除其中所有的水或所有的溶剂。实施例-7用共沸溶剂的方法,从含50wt.%结合水的炉油基污泥中脱去结合水为了评价不同量的各种溶剂对脱去含50wt.%结合水的炉油基污泥中结合水的影响,将污泥和溶剂按预先确定的重量比例放入Dean-Stark装置的RB烧瓶中,然后用覆套式加热器持续加热,用数字温度计实时监测烧瓶中的物质温度。结合水和溶剂的蒸气进入绝缘冷凝器,在5℃-6℃循环冷凝水作用下冷凝,并用接收容器收集。用接收容器底部的节流塞将冷凝物收集到分离瓶中。每次待相分离后,将收集的水和溶剂分别称重。用二甲苯去除结合水表7.1A-933mbar下,通过改变不同比例的二甲苯从炉油污泥中去除结合水表7.1B-933mbar下,通过改变二甲苯的比例除去炉油污泥中的结合水表7.1C-933mbar下,通过改变二甲苯的比例去除炉油污泥中的结合水用甲苯脱去结合水表7.2-933mbar下,通过改变甲苯的比例除去炉油污泥中的结合水用苯除去结合水表7.3-933mbar下,通过改变苯的比例除去炉油污泥中的结合水从以上表格中可以看出,污泥中所有的水都是结合水。可以观察到,以二甲苯为溶剂的情况下,加入的溶剂量必须是污泥中水重量的5.5倍。这个量可能降低到3.5-4.5倍,而实验末期最高温度不会升高太多。可以观察到,当二甲苯的量占污泥中水重量的3倍时,末期温度不仅高,而且在残留物质中有剩余水分。据观察,以甲苯为溶剂的情况下,加入的溶剂量必须是污泥中水重量的10倍。可以观察到,残留的溶剂和炉油中水分含量低。以苯为溶剂的情况下,加入的溶剂量必须是污泥中水重量的80倍。这种情况下,基本可以脱去污泥中所有的结合水。如表7-2所示,当蒸馏出的甲苯/水平均重量比与反应初始加入的甲苯/水初始重量比接近时,尽管并不能完全脱去污泥中的水,但温度达到了最高。这是因为,在这种情况下水不能完全蒸馏出溶剂,溶剂也不能完全蒸馏出水。然而,如果蒸馏出的溶剂/水的平均重量比高于反应初始加入的溶剂/水初始重量比的话,水可能随时间逐渐累积,并可能将所有溶剂从混合物中蒸馏出来,如试验1所示。相反,如试验3所示,如果蒸馏出的溶剂/水的平均重量比远低于反应初始加入的溶剂/水初始重量比的话,溶剂会随时间逐渐累积,从而确保脱去污泥中所有的水。对于二甲苯来说,溶剂/水最差的重量比为1.85。这是因为蒸馏出的溶剂/水平均重量比刚好与反应初始加入的溶剂/水重量比一样。可以观察到,当实验开始时混合物中的溶剂/水重量比与蒸馏出的蒸气相中溶剂/水平均重量比相同时,最终温度会非常高。也可以观察到,在那种情况下,很难将所有水或所有溶剂从污泥中脱去。据察,至少有1wt.%至1.5wt.%的水和相似比例的溶剂残留。当在含水量为50wt.%的炉油污泥中加入二甲苯的量为水重量的1.65倍或1.85倍时,最终我们未能达到预期目的。结合水将所有溶剂完全蒸发去除,而非溶剂将所有结合水完全脱去。这是由于当二甲苯为污泥中水重量的1.85倍时,蒸馏出的溶剂/水平均重量比本身就是1.86。尽管最终温度上升到180.1℃,还是有0.54wt.%的二甲苯和1.09wt.%的水残留。类似地,对甲苯和苯来说,加入的溶剂量可能有个分界点。如果加入的溶剂量少于分界值,那么结合水可能将所有溶剂蒸馏去除,而非溶剂将所有结合水蒸馏去除。对甲苯来说,这个分界量是含水量为50wt.%的炉油污泥中水重量的5-6倍。对苯来说这个分界量是含水量为50wt.%的炉油污泥中水重量的80倍。可以观察到,二甲苯为溶剂时,脱水率为0.33g/min,以甲苯为溶剂时为0.30g/min,但是以苯为溶剂时仅为0.02g/min。因此,脱去单位质量的水需要多得多的苯,这也是为什么脱水率会如此之低。然而,可以观察到,二甲苯的工作温度范围为96℃-138℃,甲苯的为89℃-109℃,相对来说,苯的唯一优势就是工作温度范围为72℃-80℃。使用二甲苯、甲苯和苯,其脱水率比使用同样溶剂的游离水小(参见表5.2)。可以观察到,当溶剂/水初始比例在1.65-4范围时,蒸馏出的单位重量水中二甲苯的含量增加。即使对甲苯和苯来说,加入的溶剂越多,脱去单位质量水所蒸出的溶剂越多。从表7.1C测试3中可以看出,蒸馏出的溶剂/水平均质量比可能比反应体系中溶剂/水初始质量比和最终质量比都低。那是因为最低质量比并不是在反应最开始,而是紧接着出现在反应开始后某个点。从表7.1C中也可以看出,当溶剂/水初始质量比很高时,在反应终点,反应体系中质量比急剧增加。这种现象一旦发生,最终温度依然会上升,但是仅高于纯溶剂在周围环境压力下的沸点,不会高出太多。尽管实验末期蒸馏出的溶剂/水重量比急剧增加。可以观察到平均重量比与其初始重量比相比没有多大差异。这是由于在蒸馏过程临近终点的短时期内,重量比例和沸点都急剧上升的原因。相反,如表7.1A和7.1B所示,当加入的二甲苯的重量为污泥中水重量的1.85-3.0倍时,最终温度会超过纯二甲苯在相同环境压力下的沸点。因此,可以推断质量比越低,最终温度会上升得越高。这有可能是因为当二甲苯相对较少时,并不能充分地降低炉油中最后一点结合水的沸点。因此,可以确定的是,首先,为了使得给定升温速率下炉油中剩余的溶剂能充分降低其粘度,并且充分降低炉油中最后一点结合水的沸点,反应初始加入的溶剂量得与反应终止的一致。而且,可以观察到,要想完全脱去所有的结合水,必须使得剩余炉油中存在大量的溶剂,来降低工作温度。这可能通过三个途径发挥作用:首先,炉油粘度非常小,可以在反应后期仍然保持自由流动;其次,可溶性的炉油和大部分的剩余溶剂的存在使得在反应后期沸点仍然不会显著上升;再次,大量剩余溶剂使得反应后期更容易将剩余的少量水脱去。可以观察到,以二甲苯、甲苯、苯为溶剂时,从更低粘度的油中完全脱去结合水,剩余溶剂/油重量比最小值分别为3.59、3.09和2.98。然而,要想得到上述剩余重量比,溶剂/水的初始比值应当分别为5.5、10.0和80.0并适宜控制加热速率。实施例-8溶剂加入量评价基础的建立为了建立加入溶剂量多少的评估依据,是基于污泥中水的含量或是烃的含量。将预先确定好重量比例的污泥和溶剂加入Dean-Stark装置的RB烧瓶中,然后用覆套式加热器持续加热,用数字温度计实时监测烧瓶中的物质温度。结合水和溶剂的蒸气进入冷凝器,在5℃-6℃循环冷凝水作用下冷凝,并用接收容器收集。用接收容器底部的旋塞将冷凝物收集到分离瓶中。每次待相分离后,将收集的水和溶剂分别称重。表8.1-933mbar下,确定除去炉油污泥中的结合水所加入二甲苯的依据可以看出,当实验末期剩余溶剂/炉油重量比高时,得到的结果最好。在试验3中,上述剩余比例为5.07,温度升高最少,脱去的结合水最多,剩余的水分仅为85ppm。可以认为,无论是通过污泥中水的重量还是炉油的重量来衡量加入溶剂的量都无关紧要。从试验1和2可以看出,当炉油污泥中含水较少时,水的收集率相当低。这与单位质量溶剂脱去的水越多这个事实相背。显然,炉油基污泥中的含水量水限制在可降低溶剂沸点的程度。实施例-9从不同炉油污泥中除去结合水的工艺效率的评价实验的目的在于评价从不同含水量(均为结合水)的炉油污泥中除去结合水的效率。将预先确定好重量比例的污泥和溶剂加入Dean-Stark装置的RB烧瓶中,然后用覆套式加热器持续加热,用数字温度计实时监测烧瓶中的物质温度。结合水和溶剂的蒸气进入冷凝器,在5℃-6℃循环冷凝水作用下冷凝,并用接收容器收集。用接收容器底部的旋塞将冷凝物收集到分离瓶中。每次待相分离后,将收集的水和溶剂分别称重。这里,炉油污泥中的结合水的含量为2.15%-84.94%。表9.1A-933mbar下,从具有不同含水量但固定比例的二甲苯的炉油污泥中除去结合水表9.1B-933mbar下,从具有不同含水量但固定比例的二甲苯的炉油污泥中除去结合水可以观察到,污泥中的所有水都是结合水。可以理解的是,将水和炉油混合不可能制得所含60wt.%或61wt.%以上水分全是结合水的污泥。如实施例-1中所解释的,如果将85wt.%的水和15wt.%的炉油混合,得到的是含结合水的污泥和废油的混合物。但是仍然有可能得到含结合水85wt.%的污泥。对于含结合水50wt.%的炉油污泥,加入两倍于其重量的溶剂(如二甲苯),然后21,893RCF下离心10min。污泥中大部分的炉油被去除,剩下14.5wt.%带溶剂的初始污泥,其粘度稳定,含15wt.%炉油和85wt.%结合水。这种污泥用于表9.1B的测试4中,脱去其中的结合水。在结合水为2wt.%-85wt.%范围时,用二甲苯为溶剂可以在温度不超过140.12℃的条件下脱去污泥中所有的结合水。自始至终,二甲苯的加入量为污泥中炉油重量或水重量的5.5倍。以允许加入过量的溶剂的为准。在最终温度上升至140.12℃的情况下,最终收集到的水最少,剩余物中水含量为159ppm。也可以看出,当污泥中水含量为15wt.%或更低时,脱水率明显较低。结合水的脱水率与水和炉油的键合强度成反比。当含水总量越低,这种强度越高。另外,可以看到脱水率最大值为0.33g/min,是二甲苯对游离水脱水率1.37g/min的4.15倍(如表5.2所示)。因此,可以证明这里脱掉的水是结合水而非游离水。还可以看出,当炉油污泥中水的含量仅为2.15wt.%时,起始沸点为121℃,而其他所有情况下起始沸点为95℃或96℃。同时,当水含量为2.15wt.%时,脱掉每单位质量的水除去的二甲苯的量平均为水的14.79倍。如此高的值,有可能是由于污泥中存在大量的二甲苯。通常,这个重量比在3.3-1.92之间。可以观察到,当炉油基污泥中水的含量为2.15wt.%时,收集到的水超过100wt.%。这可能是因为BTX测试结果误差较大,特别是低水分情况下。同时,即使BTX测试的含水量,其值也比实际含水量稍低。实施例-10加入不同比例的溶剂后,通过改变加热速率,从含有50wt.%结合水的炉油污泥中除去结合水实验目的在于评价加入不同比例溶剂及不同加热速率对除去含50wt.%结合水的炉油污泥中所有结合水的影响。将预先确定好重量比例的污泥和溶剂加入Dean-Stark装置的RB烧瓶中,然后用覆套式加热器持续加热,用数字温度计实时监测烧瓶中的物质温度。结合水和溶剂的蒸气进入冷凝器,在5℃-6℃循环冷凝水作用下冷凝,并用接收容器收集。用接收容器底部的旋塞将冷凝物收集到分离瓶中。每次待相分离后,将收集的水和溶剂分别称重。除此之外,通过改变加热器的输入电压来调节加热速率。加热速率的变化也就是说,在多数情况下,得到每25ml冷凝液需要约30、20或10分钟的时间。表10.1-在933mbar,通过改变加热速率,从二甲苯/水重量比为1.85的污泥中除去结合水表10.2-在933mbar,通过改变加热速率,从二甲苯/水的起始重量比为2.25的污泥中除去结合水表10.3在933mbar下,使用不同的加热速率从二甲苯与水的起始重量比为3.5的污泥除去结合水表10.4在933mbar下,使用了不同的加热速率从二甲苯与水的起始重量比为5.5的污泥除去结合水相对于污泥中存在的水,二甲苯按照4个重量比,即1.85、2.50、3.50、5.50加入到具有50wt%结合水的炉油中。然后对于每个比值,改变加热速率。可以观察到,除了对于1.85、3.50和5.50重量比外,不同加热速率的影响是最低的。可以观察到,加热的中等速率对于重量比1.85是必要的,其中水的去除率为0.48g/min或者冷凝液的去除率为1.35g/min。可以观察到,剩余材料在剩余低湿度方面获得了最佳的结果,温度上升最少。经发现这是非常敏感的比值,因为返回到剩余炉油中的剩余溶剂极少且因此随着最小的温度上升,其中微小的变化对于取出最后一点结合水来说都关系重大。在这一加热速率,相比于溶剂而言,稍多的水蒸馏出去,因此使得稍多的溶剂聚集,随后剩余的水在那一升高的温度快速蒸馏出去。因此,可以确定的是,对于加入任何数量的溶剂而言,如果想要在最少的温度从污泥中除去全部的水,必须总是试图通过经沸腾除去每单位重量的水使得平均最少数量的溶剂蒸馏出去,而在剩余的炉油中保留下最大数量的溶剂。然而,直到最后保留下来的剩余溶剂数量的微小增加对保证最小温度下从污泥中完全除去水起着巨大的作用。可以观察到,最慢的加热速率适合于3.50和5.5的重量比,尽管对于3.50而言,中速和慢速之间没有太大的差异。然而,对于5.5而言,问题很清楚。对于3.50,中等的加热速率发现并不是可行的,尽管保留下来的溶剂与同样保留下来的水一样多。这里,除去保留下来的额外的水不得不显著增加温度以及消耗大量剩余溶剂。然而,可以观察到,当加入的二甲苯的重量是污泥中水重量的1.65倍时,二甲苯不能蒸馏出全部的水。相反,污泥中存在的水蒸馏出全部二甲苯。这会发生,是因为溶剂与水蒸馏出来的平均重量比是1.79(这可从表7.1的试验1中看到),该数值比沸腾之前它们存在的起始重量比高得多。此处,可以确定的是,加热速率反而可能不得不更快。参照表7.1A和7.1C,可以看出,当加入的二甲苯是水重量的1.65倍时,水以0.52g/min的平均速率滚沸除去,当加入的二甲苯的数量为水存在重量的5.5倍时,对应数值为0.33g/min。因此,可以确定的是,对于优选重量比的二甲苯,当不得不蒸馏出全部水时,加热速率必须要慢,当必须驱赶出溶剂时,加热速率必须要快。实施例11严格控制加热速率对使用溶剂从炉油污泥中除去结合水的影响研究了额外的严格控制加热速率对除去污泥中存在的最后部分结合水的作用。相应地,在Dean-Stark装置的RB烧瓶中称取了预定重量比例的污泥和溶剂,接着在覆套式加热器中对其连续加热,同时用数字热量计监控RB烧瓶中材料的温度。在绝热冷凝器中用5℃-6℃的循环冷却水对其冷凝后,在接收器中收集结合水和溶剂的蒸汽。冷凝液出来并使用接收器底部的节流塞收集在分离烧瓶中。在相分离后,收集的水和溶剂每次单独称重。除了以下事实,朝着该过程的结尾,当约6wt%的水保留在污泥中时,加热速率显著降低,甚至周期性地使混合物的温度下降3℃-10℃。理念在于保持混合物在固定温度范围更长的时间,通过小步骤先降低,后在那一范围内再升高剩余材料的温度。此外,这意味着整个停止和再启动沸腾过程许多次。这使得最终微量的水从具有大量溶剂的污泥中剧烈且短暂的喷出。然而,需要小心以保证冷凝液不会从冷凝器顶部溢出。表11-A当使用二甲苯除去结合水时严格控制过程结尾处的加热速率的影响表11.B-随着工艺随时间进行RB烧瓶中二甲苯与水的剩余重量比正如从表11-A中看到的,冷凝液收集的平均速率仅为1.20g/min,对于成功的试验来说相对数值为1.83。因此,通过沸腾除去每单位的水,更高数量的二甲苯不会滚沸除去。因此从表11-B可以看出,直到5次收集保留下来的溶剂与水的重量比对于失败试验而言稍微较高,在那之上我们不会朝着上述过程中所述方法的结尾显著减慢加热速率。因此,正如根据表11-B可以看出的,由于高的加热速率,我们几乎以从第6次到第19次收集相等的比值结束溶剂和水的滚沸。可以观察到,至少直到10次收集,排出的溶剂要轻微超过水,因此,剩余的溶剂与水的重量比至少保持轻微下降。但是,从第11次到第17次收集,它们几乎以相等的比例滚沸除去。随着混合物的温度接近232℃,水不会保留下来。更多的热量以快于通过沸腾所能消耗的热量的速率来供给。然而,通过沸腾除去比水更多的溶剂,由于朝着结尾显著减慢了加热速率,这是因为不能提供充足的潜热以滚沸出水。在加入的二甲苯的重量是存在的水重量的2.28倍情况下。在此情况下,当加热缓慢使得冷凝液的收集速率仅为0.50g/min时,其中二甲苯与水滚沸出去的重量比为2.07。这使得二甲苯聚集,而不是通过优选经沸腾从污泥中去除水。此处,首先随着冷凝液的收集速率为2.30g/min,失败样品的整体加热速率较高,这是因为,与较慢的加热速率相比,除去每单位重量的水,它开始滚沸出去很少量的溶剂。幸运地是,直到第三次收集并没有发生太多的损害。在第4次和第5次收集,随着快速加热保留下更多的溶剂。此外,朝着结尾,对失败样品并不减慢加热速率。可以观察到,当加热速率供给远远超过需求时,剩余炉油的温度保持上升。在那之后,首先,水开始快速释放,因为考虑到它的高潜热能够吸收热量。因此,从第7次收集开始,保留下来的溶剂与水的剩余重量比一致上升并在第9次收集后大幅上升。然后在大部分水保留下之后,由于高温,在除去水的代价下,溶剂沸腾速率快速上升。因此,在第10次收集后,尽管事实上一些水仍然保留了下来,但很难存在任何溶剂来去除这些水。正如表11-A中看到的,在结尾处,剩余溶剂与炉油的重量比下降到0.02。在大量剩余溶剂的帮助下,通过降低水沸点,从炉油中取出剩余的水对起始加入的二甲苯的该比值是期望的。这就是无论是否已超过300℃,都要从炉油中除去整个水。因此,可以确定,通过选择较慢的加热速率使得到第6次收集为止,较少的溶剂释放出去,因此在RB烧瓶中保留下来较高的溶剂与水的重量比。随后,通过剧烈地减慢加热速率来提供接近于从炉油中滚沸出少量水和溶剂所需的加热速率。从第7次收集直到第11次收集结束,水仅稍微优选于溶剂滚沸出来,但并不是如之前有很大的优选。因此,最终在RB烧饼中保留下来大量溶剂,以驱赶出最后一点水,炉油温度仅上升到163℃,而非307℃。最后,可以观察到,利用快速加热速率,水优先于溶剂较大值沸腾,因为水需要大量潜热进行相转变。因此,可以观察到,如果保留下来的溶剂与水的剩余重量比较高,但高得仅较小的值,利用极慢的加热速率,水重新优先于溶剂沸腾,原因在于供热速率并不是驱动因素。最后,可以观察到,如果存在的溶剂数量比水高得多,则水利用极低的加热速率优先沸腾出来。实施例12通过将其用共沸物溶剂沸腾而从含乳化剂的柴油污泥中去除结合水本试验的目的在于评价用共沸物溶剂从包含乳化剂的柴油污泥中滚沸出结合水和非结合水的方法。因此,在Dean和Stark装置的RB烧瓶中称取预定重量比的含乳化剂污泥和共沸物溶剂的混合物,接着在覆套式加热器中对其连续加热,同时利用数字热量仪连续监控RB烧瓶中材料的温度。在绝热冷凝器中用5℃-6℃的循环冷水冷凝之后在接收器中收集结合水与溶剂的蒸汽。冷凝液流出并使用接收器底部的节流塞收集在分离烧瓶中。相分离后,每次单独称取收集的水和溶剂。表12-使用二甲苯&甲苯在933mbar从柴油污泥中除去结合水和非结合水可以观察到,当向其中加入如十二烷基硫酸钠的乳化剂时,在柴油污泥中仅存在微小量的结合水。换句话说,仅有全部水存在量的约6wt%紧密结合到柴油上,使得即使在21,893RCF对其离心10分钟,那些水也不能与柴油分离。与炉油污泥相比,当使用二甲苯时水的去除率快约2.2倍,当使用甲苯时快约1.6倍,炉油污泥中,结合水的存在量为49.81wt%,如表7.1C和7.2中清楚地看到。这是因为仅存在的少量水为结合水。然而可以观察到,水的收集速率显著地低于表5.2中观察到的,其中二甲苯和甲苯分别以1.37g/min和0.67g/min的速率去除游离水。这里可以看出,当加入的二甲苯的重量是全部水存在量的5.51倍时,二甲苯结果将污泥中的全部水除去,即结合水和游离水两者。可以观察到,尽管事实上大部分存在的水是非结合水,但甲苯和二甲苯两者都除去了污泥中存在的结合水和非结合水,但最终的温度分别上升到110.61℃和139.24℃。这是因为一旦全部的水被除去,这些溶剂的沸点不能再进一步地降低。一旦全部的水被去除,所留下的是溶剂和柴油的溶液,其中柴油正好具有轻微较高的沸点。可以观察到,在那一阶段,随着进一步施加热量,在给定周围压力下,溶剂开始在它们各自的沸点滚沸出来。尽管事实上收集的溶剂和水的最终重量比极高,但平均比值仍然极小,且仅轻微高于起始的重量比,这意味着仅在朝着该方法的结尾,溶剂与水的重量比存在短暂和剧烈的上升。实施例13通过用共沸物溶剂沸腾从其中具有42wt%结合水的ONGC污泥中去除结合水目的在于评价使用不同数量的不同溶剂对从其中具有42.21wt%结合水的ONGC污泥中去除结合水的影响。因此,在Dean和Stark装置的RB烧瓶中称取预定重量比的ONGC污泥和共沸物溶剂的混合物,接着在覆套式加热器中对其连续加热,同时利用数字热量仪连续监控RB烧瓶中材料的温度。在绝热冷凝器中用5℃-6℃的循环冷水冷凝之后在接收器中收集结合水与溶剂的蒸汽。冷凝液流出并使用接收器底部的节流塞收集在分离烧瓶中。相分离后,每次单独称取收集的水和溶剂。具有结合水的ONGC污泥表13.1-通过不同比例的溶剂在933mbar下从ONGC污泥中除去结合水可以观察到,当甲苯和二甲苯分别相对于污泥中存在的水或者烃的重量以10和5.5的重量比加入时,从而促使加入了最大数量的溶剂。可以观察到,对于甲苯和二甲苯两者来说,优选慢的加热速率,从而最终保留下来的溶剂多于烃。可以确定,通过加入最佳数量的溶剂、采用慢的加热速率以及大气压力,将粘稠的ONGC污泥中存在的几乎全部的结合水除去而不使温度上升到超过这些纯溶剂的沸点是可能的。实施例-14通过结合使用共沸溶剂从不同的污泥中去除结合水目的在于评估结合使用二甲苯和甲苯对从分别具有42.21wt.%和49.81wt.%结合水的ONGC和炉油污泥中去除结合水的影响。相应地,将预定重量比的污泥和共沸溶剂混合物放入Dean-Stark装置的RB烧瓶中,接着在覆套式加热器中对其连续加热同时用数字温度计连续监测RB烧瓶中材料的温度。结合水和溶剂的蒸气在绝缘冷凝器中用5℃到6℃的循环冷却水对其冷凝之后收集到接收器中。冷凝物流出并使用接收器底部的节流塞收集在分离烧瓶中。在每次相分离之后,单独称量收集的水和溶剂。表14.1-在933mbar下,结合使用二甲苯和甲苯从污泥中去除结合水这些测试确定,通过结合使用二甲苯和甲苯作为共沸溶剂可将全部结合水从ONGC和炉油污泥中去除。此外,可以观察到,当这些溶剂单独地用于ONGC和炉油污泥时,观察到的最大沸腾温度几乎介于两个最大沸腾温度之间。实验例-15通过使用游离水加热从烃中去除全部溶剂实验目的是建立和评估通过向其添加游离水使全部如炉油中的二甲苯、甲苯和苯的溶剂在低于100℃以及大气压933mbar情况下沸腾出来。因此,称取一定量的炉油、溶剂和水按特定比例添加到Dean-Stark装置的RB烧瓶中,接着在覆盖式加热器中对其加热,同时用数字温度计周期性记录下RB烧瓶中材料的温度。可以确定的是,溶剂与炉油的初始重量比大于从炉油污泥中去除全部结合水之后留在RB烧瓶中溶剂与炉油的重量比。沸腾出的水和溶剂蒸气冷凝在绝缘冷凝器中,其中,水在5℃到6℃下循环。冷凝物在接收器中收集,因而使用接收器底部的节流塞以周期性地排出分离烧瓶中的冷凝物,同时记录经过的时间。在相分离之后,单独称量收集的水和溶剂。最后。称量留在RB烧瓶的材料,且进行质量平衡。表15.1A-在933mbar下通过改变游离水比例从炉油中去除二甲苯表15.1B-在933mbar下通过改变游离水比例从炉油中去除二甲苯表15.2A-在933mbar下通过改变游离水比例从炉油中去除甲苯表15.2B-在933mbar下通过改变游离水比例从炉油中去除甲苯SI号说明试验1试验2试验31RB烧瓶中称取的炉油重量(g)150.59150.20150.002RB烧瓶中称取的溶剂重量(g)602.89600.95600.013添加到RB烧瓶中的游离水重量(g)301.66450.90600.364水与溶剂的初始重量比0.500.751.005溶剂与炉油的初始重量比4.004.004.006观察到的沸腾温度范围(℃)95.17-111.7894.78-111.9897.28-98.57收集的溶剂与水的初始重量比6.614.974.858收集的溶剂与水的最终重量比0.740.110.089收集的溶剂与水的平均重量比5.062.482.3810收集的水的总重量(g)119.60244.24252.3111收集的溶剂总重量(g)605.84606.01602.6612溶剂的平均收集速度(g/min)6.424.042.9613实验结束RB烧瓶中留下的炉油重量(g)147.64145.14147.3514实验结束RB烧瓶中留下的游离水重量(g)177.53199.47343.8615由于蒸发等损耗的重量百分比0.430.600.31表15.3A-在933mbar下通过改变游离水比例从炉油中去除苯表15.3B-在933mbar下通过改变游离水比例从炉油中去除苯表15.4-在933mbar下,用游离水从炉油中完全去除50:50二甲苯和甲苯SI号说明试验11RB烧瓶中称取的炉油重量(g)151.212RB烧瓶中称取的甲苯重量(g)226.653RB烧瓶中称取的二甲苯重量(g)227.164添加到RB烧瓶中游离水重量(g)682.025水与二甲苯的初始重量比3.006二甲苯与炉油的初始重量比1.507水与甲苯的初始重量比3.008甲苯与炉油的初始重量比1.509观察到的沸腾温度范围(℃)96.20-97.1810收集的溶剂与水的初始重量比3.6511收集的溶剂与水的最终重量比0.0612收集的溶剂与水的平均重量比1.3513收集的水总重量(g)337.2114收集的溶剂总重量(g)456.6115溶剂的平均收集速度(g/min)1.5816实验结束RB烧瓶中留下的炉油重量(g)148.4117实验结束RB烧瓶中留下的游离水重量(g)339.4018因蒸发等损耗的重量百分比0.42表15.5-在933mbar下用游离水从柴油中完全去除溶剂SI号说明试验1试验21RB烧瓶中称取的柴油重量(g)75.3575.292使用溶剂的名称甲苯二甲苯3RB烧瓶中称取的溶剂重量(g)301.15226.074添加到RB烧瓶中的游离水重量(g)303.20454.565水与溶剂的初始重量比1.012.016溶剂与柴油的初始重量比4.003.007观察到的沸腾温度范围(℃)92.54-97.2496.50-97.278收集的溶剂与水的初始重量比5.171.989收集的溶剂与水的最终重量比0.820.6110收集的溶剂与水的平均重量比3.571.1511收集的水总重量(g)86.33200.2312收集的溶剂总重量(g)308.36232.9913溶剂的平均收集速度(g/min)3.302.0414实验结束RB烧瓶中留下的柴油重量(g)68.1468.3715实验结束RB烧瓶中留下的游离水重量(g)211.77250.1516因蒸发等损耗的重量百分比0.750.55表15.6-在933mbar,用游离水从ONGC粘稠脱水烃中去除溶剂SI号说明试验1试验21RB烧瓶中称取的ONGC烃重量(g)86.0786.092使用溶剂的名称甲苯二甲苯3RB烧瓶中称取的溶剂重量(g)378.73322.134添加到RB烧瓶中游离水重量(g)379.16644.345水与溶剂的初始重量比1.002.006溶剂与ONGC烃的初始重量比4.403.747观察到的沸腾温度范围(℃)88.21-99.4093.30-96.338收集的溶剂与水的初始重量比4.891.989收集的溶剂比水的最终重量比0.080.0310收集的溶剂与水的平均重量比2.161.0711收集的水总重量(g)177.25304.8812收集的溶剂总重量(g)382.89326.7713溶剂的平均收集速度(g/min)1.351.1714实验结束RB烧瓶中留下的ONGC烃重量(g)81.9181.4515实验结束RB烧瓶中留下的游离水重量(g)106.82335.3416因蒸发等损耗的重量百分比0.600.39可以观察到,溶剂在无游离水存在的情况下不能完全从炉油沸腾除去,且溶剂沸点不会最终升到350℃,这是纯净炉油是初始沸点。可以观察到,在溶剂与炉油的初始重量比为1或更高的情况下,在相同气压溶剂可能总是在纯溶剂的沸点开始沸腾。但是最终随着最后一点溶剂沸腾出去,其沸点可能接近纯净炉油的沸点,在大气压为933mbar的情况下为350℃。对于甲苯,这在表6.1中可清楚地看到。然而,可以看出,在压力为933mbar的情况下,当游离水存在的量合适,全部溶剂在低于100℃下可从相同炉油中煮出。对于甲苯,如从表15.2A看到的,观察到的本实验例的沸腾温度为95.90℃到97.60℃。然而,如从表6.1看到的,在游离水不存在的情况下,所述范围是110.93℃到350.15℃。此外,可以观察到的,当从其中具有50wt.%结合水的炉油污泥中去除全部结合水时,通过添加污泥中存在的水重量5.5倍的二甲苯。可以看出,在过程的末尾,留下的二甲苯与炉油的重量比是3.59。因此,添加的二甲苯是炉油重量的6倍,且添加的水是存在的炉油重量的3倍。经发现,在添加的二甲苯是炉油重量的6倍且添加的水是二甲苯初始重量的1倍的情况下,沸腾温度在96.24℃到97.90℃的范围内。可发现的是在添加的二甲苯是炉油重量的3倍且添加的水是二甲苯初始重量的2倍的情况下,沸腾温度在96.89℃到97.58℃的范围内。因此,可确定的是存在溶剂的比例越小,在100℃下需要来保留溶剂沸点范围的游离水越多。此外,如之前看到的,在从上述炉油污泥中去除结合水的末尾,如表7.2所示留下的甲苯与炉油的重量比是3.09,且如表7.3所示留下的苯与炉油的重量比是2.98。因此,该过程通过添加存在的炉油重量4倍的甲苯开始,且之后添加存在的炉油重量3倍的甲苯。在这两种情况下,优选的游离水与溶剂的初始重量比为1。在优选的游离水数量的情况下,甲苯的沸点范围分别为97.28℃到98.50℃和96.40℃到98.30℃。对于苯,苯的重量比例是存在的炉油重量的3倍,且之后存在的炉油重量的2倍。可以看出,对于3倍的苯,优选的游离水与溶剂的初始重量比是2。然而对于2倍苯,优选游离水与溶剂的初始重量比为1.50倍替代。可以看出,对于这两种优选的游离水的量,沸腾温度范围分别是80.12℃到98.59℃和86.70℃到98.31℃。因此,可以确定的是,明显对多少溶剂能初始地存在于炉油中或存在的溶剂类型没有限制。然而,无论是苯、甲苯或二甲苯,其全部溶剂能通过先于加热添加合适数量的游离水且在低于100℃的温度下煮沸去除。事实上,更多的初始存在溶剂通常是更少的游离水比溶剂的添加重量比例。此外,可以看到的是游离水的量超出一定限制,不仅溶剂沸点范围下降,而且通过单位质量的水煮出来去除的溶剂量也下降。在全部情况中,尽管并未考虑将会蒸发的一些溶剂,但收集到的溶剂都超过100wt.%。那是因为,在也收集到一些炉油之后,接近结束时沸腾终止。然而,可以看出,在933mbar下,溶剂最后的沸点总是保持在低于100℃。随着溶剂,一些炉油也被收集仅为确保100%去除溶剂。因此,炉油轻微损耗。但是如果该溶剂重复使用,炉油不会有进一步的损耗。可以看出,收集的溶剂与游离水的平均重量比总是低于收集的溶剂与结合水的平均重量比。还观察到平均收集温度低于优选的游离水与溶剂的初始重量比。如表15.4看到的,当如二甲苯和甲苯的混合溶剂例如以50:50的重量比例存在于炉油中,在低于100℃的温度下通过确保游离水添加重量是结合的初始存在溶剂重量的1.50倍,二甲苯和甲苯可通过沸腾全部除去。然而,如表15.4表明,当使用混合溶剂来从污泥中煮出全部结合水时,留在过程末尾的溶剂与炉油的重量比更高。明显地,只要煮沸之前添加的游离水数量合适,对多少溶剂存在于炉油中没有上限。如表15.5和15.6看到的,在例如自由流动的柴油的烃或高度稠脱水ONGC烃等的情况下,存在的全部溶剂在低于预定义温度下可以煮出。在烃中含有盐和/或灰分或固体的情况下,游离水则在低于100℃下,除了沸腾出全部的纯溶剂用于重复使用或销售之外,还可能额外执行脱盐和脱灰分的功能。实验例-16游离水和炉油的分离目的在于确定,游离水可以随时间通过基于重力的沉降或离心甚至从粘稠烃中分离。因此,称量一定量的粘稠炉油和游离水放入RB烧瓶中,并剧烈煮沸15分钟。此后,在高温条件下,该物质转移到预热的和绝缘的分液烧瓶中。可以看到的是大部分游离水由于密度差异和重力从不混溶炉油中分离。累积的游离水大约30分钟之后从分液烧瓶底部去除。分液烧瓶中的剩余材料在去除其绝缘性之后,在干热灭菌器中放置48h并维持在90℃的温度。收集的水周期性地从分液烧瓶底部去除。48h之后,取出、均质化剩余材料然后并使用BTX方法测试剩余湿度。随后地,重复煮沸且将热材料转移到非绝缘分液烧瓶中。该材料在其大部分游离水去除之后很快去除。然后取出剩余含有17.33wt.%水分的炉油。部分炉油被再次加热且允许剩余部分冷却到室温。这两个冷热部分在4,500RCF下离心5分钟。离心之后,150g炉油从顶部去除并通过BTX方法测试湿度。表16.1-通过基于重力的沉降从炉油中分离游离水表16.2-通过热离心机从炉油中分离游离水表16.3-通过冷离心机从炉油中分离游离水可以观察到,从相对粘稠的炉油中去除全部游离水是困难的。将粘稠炉油加热到大约99℃来减少其稠度,然后以最少的温度下降热转移到预热的绝缘良好的分液烧瓶中。在其中保留30分钟且温度下降少于6℃,大约94wt.%到95wt.%的水被排出并收集在分液烧瓶的底部。此外,在接下来的48小时内,在大约85℃到90℃下加热全部剩余材料来得到剩余5wt.%到6wt.%的水。最后可观察到的,在周期的去除从分液烧瓶底部收集的游离水之后,少于3,500ppm的残留水留在炉油中。因此,像需要的沉降时间、加热所需最大温度和粘稠烃中残留水含量的参数被确定。可看到的是大约83wt.%的水在热条件下通过重力沉降后在4,500RCF下对其离心5分钟去除。但是炉油中仍有残留的水分从17.3wt.%降到11.8wt.%。然而热离心在进气温度90℃下操作,其中炉油中残留水分在4,500RCF下离心5分钟之后从16.48wt.%减少到2900ppm。明显的是浑浊度为6NTU到7NTU的回收水优选用于工业使用,其几乎无油,可进一步处理用于生产饮用水。实验例-17从石油污泥中去除纯净烃、结合水、溶剂以及游离水本实验旨在根据本发明方法定量和定性回收稠污泥中存在的纯净烃和包括结合水的全部水,并回收全部溶剂和游离水。因此,首先确定存在于污泥中的结合和非结合水的重量分数,进而计算添加到污泥的溶剂量,之后在Dean-Stark装置中使用覆盖式加热器加热。因此,存在于污泥中的全部结合水和游离水通过结合溶剂和加热的效用去除。随后全部水被冷却并与部分使用的溶剂被收集。此外,将计算出来的游离水的量加入到RB烧瓶中的剩余物质中,使用相同的装置再次加热。随后,去除了全部的剩余溶剂,并与一些游离水一起被收集。此后在烃较稠的情况下,加热烃并将其保留在热环境下预定义的时间周期之后,通过重力沉降收集残留烃中全部量的剩余游离水。最终,通过质量平衡研究,水和烃都要评价其质量/纯度,此外回收的量也要估算。炉油污泥表17.1-通过与共沸溶剂煮沸从仅具有结合水的炉油污泥中去除全部结合水表17.2-通过使用游离水从脱水的炉油去除全部溶剂SI号描述试验1试验21RB烧瓶中存在的脱水炉油重量(kg)0.5030.5022RB烧瓶中存在的溶剂重量(kg)1.78351.5613RB烧瓶中添加的游离水重量(kg)3.5691.5614水与溶剂的初始重量比2.001.005观察到的沸腾温度范围(℃)96.89-97.5896.40-98.306收集的溶剂与水的初始重量比2.075.127收集的溶剂与水的最终重量比0.054.148收集的溶剂与水的平均重量比1.052.359收集的游离水总重量(kg)1.8960.6710收集的溶剂总重量(kg)1.7881.56511实验结束RB烧瓶中留下的炉油重量(kg)0.4990.49812实验结束RB烧瓶中留下的游离水重量(g)1.6340.8613因蒸发等损耗的重量百分比0.510.66表17.3-从具有溶剂和无结合水的炉油中去除全部游离水表17.4-测试结果表17.5炉油污泥中回收的结合水的质量表17.6-通过与共沸溶剂煮沸从仅包含结合水的ONGC稠污泥中去除全部结合水表17-7-通过使用游离水从脱水烃去除全部溶剂SI号说明试验1试验21RB烧瓶中存在的脱水烃的重量(kg)0.5780.5792RB烧瓶中存在的溶剂重量(kg)2.1073.1933RB烧瓶中添加的游离水重量(kg)4.2153.174水与溶剂的初始重量比2.001.005观察到的沸腾温度范围(℃)93.25-96.3088.18-99.266收集的溶剂与水的初始重量比2.014.937收集的溶剂与水的最终重量比0.030.078收集的溶剂与水的平均重量比1.052.149收集的游离水总重量(kg)1.9941.4910收集的溶剂总重量(kg)2.1143.19811实验结束RB烧瓶中留下的烃重量(kg)0.5720.57412实验结束RB烧瓶中留下的游离水重量(g)2.1941.65913因蒸发等损耗的重量百分比0.400.62表17.8-从烃中分离全部游离水表17.9-测试结果表17.10-通过与共沸溶剂煮沸从包含结合和游离水的自由流动柴油污泥中去除全部水表17.11-通过使用游离水从脱水柴油中去除全部溶剂SI号说明试验1试验21RB烧瓶中存在的脱水柴油的重量(kg)0.4950.4982RB烧瓶中存在的溶剂重量(kg)1.3771.5783RB烧瓶中添加的游离水重量(kg)2.7671.5944水与溶剂的初始重量比2.011.015观察到的沸腾温度范围(℃)96.42-97.2192.42-97.186收集的溶剂与水的初始重量比2.015.197收集的溶剂与水的最终重量比0.600.828收集的溶剂与水的平均重量比1.133.499收集的游离水总重量(kg)1.2230.45310收集的溶剂总重量(kg)1.3831.58511实验结束RB烧瓶中留下的柴油重量(kg)0.4890.49112实验结束RB烧瓶中留下的游离水重量(g)1.5221.11213由于蒸发等损失的重量百分比0.480.78表17.12-从柴油分离游离水表17.13-测试结果参照表17.1到17.13,存在于污泥中的回收的总炉油大约是99wt.%。尽管事实在于其小部分随着溶剂收集被去除。可以看到的是回收的炉油平均含有大约3,806ppm的剩余水分而其原始水含量为2,100ppm。可观察到的是尽管水含量略高,回收炉油的平均热值为10,176kcal/kg而原始炉油热值为10,172kcal/kg。此外,可以观察到,对于ONGC烃来说,污泥中存在的大约98wt.%的烃被回收,其平均剩余水为3,000ppm,从而观察到其具有的平均热值为10,635kcal/kg。此外,可观察到的是平均大约96wt.%柴油从柴油污泥中回收,其平均水分水平为47ppm且平均热值为11,021kcal/kg,而原始柴油的热值为11,002kcal/kg。此外,可以观察到,超过99wt.%的结合水从炉油污泥中去除,且具有优良品质,这可清楚地在表17-5中看到。可以观察到,从ONGC污泥中回收的结合水为99.5wt.%。从柴油污泥中回收的结合水为100wt.%。此外,可以观察到,超过99wt.%的溶剂从炉油污泥中回收。ONGC污泥回收到的溶剂为99wt.%。柴油污泥回收到的溶剂被发现为98.9wt.%。此外,可以观察到,从炉油污泥中回收的游离水平均大约为96.5wt.%。ONGC污泥回收到的游离水为97.3wt.%。基于柴油的污泥回收到的游离水被发现为98.6wt.%。得到的游离水数量较大并对其多步处理超过48小时。实验例-18通过回收纯沙、油和二甲苯之后使用二甲苯制备涂沙油和脱油沙为了研究固体炉油和ONGC中烃的去除,制备涂覆沙子的自由流动油样品。使用像二甲苯的溶剂处理这些沙样,且此后定量和定性评价沙、油、二甲苯和水的回收。首先,称量一定量的油混入称量的沙中,其经水洗、完全干燥且十分干净。在将油混入沙中之后,涂覆沙子的油样品在分批的二甲苯中清洗。油逐步地从沙子移动到二甲苯中。一旦纯二甲苯的浑浊值和颜色在持续的沙子清洗循环之后与其原始状态相比无很大变化,则停止清洗。在此阶段,沙子被认为被二甲苯涂覆,而沙子上的全部油被认为移动到了所用的二甲苯中。在Buchi旋转蒸发器中缓慢加热涂覆二甲苯的沙子至超过二甲苯的沸点。冷却并收集二甲苯蒸汽。随后,在迪安斯塔克装置中用游离水加热二甲苯油混合物至煮出全部二甲苯和一些游离水,从而将一部分游离水留在油中。随后,全部材料在85℃到90℃保持48小时,游离水通过重力分离去除。最后,通过对其进行质量平衡评价回收的沙、油和游离水的质量。表18.1-油沙的生产SI号说明试验1试验21称取的沙重量(kg)1.001.002用水清洗沙子之后的最终水的浑浊度(NTU)1.211.153在815℃加热1小时纯沙损失的重量百分比0.160.164添加油的类型ONGC自由流动烃炉油5添加到沙中的重量(kg)0.100.156油沙的总重量(kg)1.101.157存在于油沙中的油重量百分比9.2113.16表18.2-通过二甲苯清洗从油沙中去除油SI号说明试验1试验21每次清洗中二甲苯与油沙的重量比1.52.02每次清洗中添加的二甲苯重量(kg)1.652.313洗掉油所需的最大清洗次数474使用的二甲苯总重量(kg)7.30015.2405最终清洗沙子之后二甲苯的浑浊度(NTU)0.4630.5016纯二甲苯的浑浊度(NTU)0.4210.421表18.3-沙、油和二甲苯的回收表18.4-测试结果参照表18.1到18.4,可以观察到,回收的沙大约为100wt%。此外,可以看到,回收的油大约为99wt.%且包括粘附在不同表面全部可称量材料的回收溶剂大约为96wt%。甚至用来从油中煮出溶剂的游离水的回收高达98wt%。回收的沙是无油的且其在815℃下加热1小时的wt.%损失是0.11wt%,这比无油、新鲜沙子的0.16wt.%少。观察到的浑浊度仅为0.56NTU,而用于清洗精细自由新鲜沙子的水的浑浊度为1.2NTU。回收的ONGC自由流动油的残留水分为3,420ppm,热值为10,580kcal/kg,而原始ONGC油的残留水分为3,900ppm,热值为10,652kcal/kg。可以看到,回收炉油的残留水分为约3,123ppm,热值为10,164kcal/kg,而原始ONGC油的残留水分为2,100ppm,热值为10,173kcal/kg。可以看到的是回收的溶剂其中平均仅有153ppm水分,而使用的原始二甲苯的为40ppm水分。此外,可以观察到,清洗单位质量涂覆油的沙子所需二甲苯的量取决于涂覆沙子的油的类型和涂覆沙子的油的量。所需二甲苯的重量大约是用于去除9.2wt.%ONGC自由流动油的油沙的7倍。所需二甲苯的重量相反大约是用于完全脱油的沙子的13倍,其包含13.12wt.%炉油。实验例-19废油与时间相关变化的浑度值的效应目的在于评估废油浑度值随时间的变化。此外,旨在观察哪个烃片段易于生产稳定的废油。其也旨在研究溶剂与油的行为不同的原因。因此,用不同的油和溶剂制备废油。这些油/烃以每百万变化的份量添加到水中并在高剪切混合器中在10,000RPM下随时间变化剧烈碎裂。随后用HACH浊度仪在455nm的波长下对典型的样品进行浑浊度测试。浑浊度读数以NTU(一般浑浊度单位)测量,从而定期记录这些废油的浑度值直到其趋于常数值。表19.1-用于制备废油的油和溶剂的说明SI号烃说明存在的水Wt.%灰分含量Wt.%热值kcal/kg1椰子油0.04Wt.%游离水0.018,9722ONGC油0.39Wt.%游离水0.8810,6333ONGC稠烃42.21Wt.%结合水8.605,2134柴油0.01Wt.%游离水0.0011,0025炉油0.21Wt.%结合水0.2310,1736二甲苯0.004Wt.%游离水0.0010,2057甲苯0.004Wt.%游离水0.0010,0748苯0.002Wt.%游游离水0.009,995可以观察到,不像二甲苯和甲苯,苯不易碎裂或甚至很短时间内通过在水中剧烈搅拌也不能在细液滴中保持碎裂,因此苯被认为不能与二甲苯和甲苯一样适合于从废油中清理超细油滴。这是通过如图7和图8所示的其8NTU到12NTU浑浊度值的表明的。透明液体的浑浊度值能表明每液体单位体积直径为455nm的液滴种群密度。废油包含所有尺寸的油滴。其中,发现超细的液滴最难清理。发现当目的是去除超细油滴时,苯没有二甲苯和甲苯有效。可发现的是极大的溶剂液滴更合适用于去除所有油滴,而不是其尺寸极小的部分。较大的溶剂液滴能更快地去除大量存在的油。因为这些溶剂大液滴是当大量较小液滴由于浮力上升时被冲走和被其携带的物质。可以看出,仅全部油的一小部分残存在超细液滴中难以去除。然而,发现超细液滴导致浑浊度达到一定程度。因此,当特别是通过轻度混合将其手工混入废油,像苯或甚至是二甲苯和甲苯的相对较大的溶剂液滴不能降低废油浑浊度超过某一点。因此,可确定的是必须使用立刻碎裂成超细液滴并快速凝聚成极大尺寸的液滴来得到所有尺寸溶剂液滴的优点的溶剂。尽管发现二甲苯和甲苯用于处理废油是好的,但是二甲苯因其初始碎裂成大量较小尺寸液滴而优于甲苯。图9到图12与图13到图20相比,证明良好的溶剂快速凝聚,不像废油中存在的烃一样的论述。不像少数柴油,大部分分散的烃需要几天时间凝聚并减少其浑浊度。然而,甲苯和二甲苯的浑浊度值几小时内下降。也可看到的是不像那些大部分烃,二甲苯和甲苯的浑浊度值随浓度的增加快速下降。这可通过对比图9和图14清楚的看到。可看到的是使用溶剂,更高的浓度不能导致更高种群密度的超细液滴。相反其触发即时的凝聚。此外,可看到的是,甲苯和二甲苯的浑浊度值通过在10,000RPM下混合时间的增加快速下降。这与包括柴油的大部分烃发生的反应相反。对于像柴油和ONGC油的烃,混合时间的增加进一步引起随超细液滴碎裂,种群密度增加。但是对于椰子油,其初始缩小液滴尺寸的变化。可能通过使液滴尺寸更均匀且其浑浊度值不随时间变化制造更稳定的废油。然而,对于溶剂,更多的混合导致表面能的不稳定增加,其进一步触发立刻的凝聚。可看到的是通过在10,000RPM下把混合时间从1分钟延长到5分钟,2500ppm甲苯的浑浊度值从1,570NTU和4,682NTU下降到54NTU和874NTU。可确定的是快速凝聚的溶剂帮助其快速长成较大液滴并降低阻力,由于浮力这之后帮助液滴快速上升。此处,观察到甲苯优于二甲苯。在柴油的情况下,可以看出,柴油初始时也碎裂,但没有甲苯和二甲苯多。还可看到的是柴油在凝聚方面与其他烃相比极快,但仍未发现其与甲苯和二甲苯凝聚一样快。在10,000RPM下混合13min之后,2,500ppm的柴油废油的浑浊度值为3,852NTU,而相同ppm&RPM的甲苯和二甲苯在5mins单独混合之后的浑浊度值分别为54NTU和874NTU。然而,如图21清楚的看到,发现由于天然快速凝聚,基于柴油的废油最易于处理回收油和干净水。在2,500ppm椰子油在水中在10,000RPM下混合3分钟的情况下,得到非常稳定的废油。但是该稳定性随混合时间的进一步增加消失。因此,可确定的是对于非常稳定的基于椰子油的废油,在对其处理回收纯油和水之前必须以剧烈的混合开始。看起来高度稳定的基于ONGC自由流动油的废油可通过延长其混合时间或通过增加其烃浓度来形成。然而,发现不确定的是取决于废油颜色的值的程度和油滴尺寸的程度。实验例-20加热对废油浑浊度的影响目的在于理解,当废油在85℃到95℃的烤箱中加热几个小时或经受剧烈煮沸5分钟时,加热对废油浑浊度的影响。因此,如下述表20.1和20.3解释的,用椰子油和自由流动ONGC油制备低等和中等浑浊度的废油。仅在加热前后立刻测量低浑浊度废油的浑浊度值。此外,如表20.4解释的在有或没有初始加热的情况下,基于椰子油的中等浑浊度的废油经受意图减少浑浊度的五步处理。表20.1-使用高剪切混合机生产废油表20.2-上述废油剧烈沸腾的结果SI号说明试验1试验2试验3试验41煮沸时间(min)77772温度范围(℃)95-9895-9895-9895-983加热之后废油的平均浑浊度38.243552.168.9表20.3-使用高剪切混合器生产基于椰子油的废油SI号说明加热处理煮沸处理无加热处理1废油总重量(kg)0.500.500.492混合时间(min)5.005.005.003混合RPM10,00010,00010,0004废油中油含量(ppm)2,4992,4992,4995检查浑浊度之前过去的时间(min)4.003.704.056废油的浑浊度(NTU)4,7014,8144,763表20.4-在不去除时间效应情况下上述废油的逐步处理结果发现如表20.1和20.2所示的剧烈沸腾对废油浑浊度的影响的研究是重要的,因为其仅限于浑浊度低、ppm低的废油。在五步处理的2步之后得到这种废油,即在用溶剂第三次离心之后去除溶剂和烃的全部最上层。此后,全部分散溶剂在其中存在的游离水帮助下从废油中滚沸出。尽管如此进行,我们想要分别单独地评价仅沸腾对废油的剩余浑浊度的影响,除了去除的溶剂对废油的剩余浑浊度的影响之外。除非沸腾出溶剂之后废油剩余浑浊度很大,此处研究表明沸腾影响很小。对于剩余值为38NTU到69NTU和剩余值为废油浑浊度2.09%到4.5%,沸腾影响进一步减小。然而,对于像435NTU的高残留值,由于单独沸腾,浑浊度的减少是残留浑浊度值的33%。由于溶剂的去除,煮沸相关的浑浊度值减少是额外的。这些浑浊度值减少的部分原因是时间的流逝。因此,结论是对低残留浑浊度值,煮沸的影响可以忽略。如表20.3和表20.4看到的,由于加热时未去除时间流逝的影响,对于中等浑浊度的基于椰子油的废油,可观察到浑度值立刻减少大约9%到14%。可观察到煮沸时该影响更大。加热或煮沸对基于椰子油的废油的浑浊度的影响随后续废油的处理减少。可看到的是煮出溶剂之后或添加明矾之前,加热和煮沸的影响都完全消失。因此,可确定的是预热或煮沸废油是不需要的。实验例-21在减少废油浑浊度方面仅溶剂的时间校正的影响在去除来自报道的浑浊度结果受时间的影响之后,研究了仅使用像甲苯的低稠度溶剂在减少废油浑浊度方面的影响。因此,将5Wt%甲苯添加到制备的废油中。使用高剪切混合器在10,000RPM下混合1分钟。添加溶剂之前,测试废油的浑浊度并记录时间。对大部分油,允许添加溶剂的样品放置20小时且溶剂在顶部收集。之后,包含溶剂和油的顶层从每种废油样品中分离,且均质化之后测试剩余材料的浑浊度并再次记录时间。随后地,在废油中存在的游离水的帮助下,在95℃到98℃的温度范围内从剩余材料中煮出全部的残留溶剂。冷却之后,添加补充水来代替煮沸过程中损失的水。此后,再次测试废油的浑浊度并记录时间。此处测试样品的每个浑浊度值都是时间校正的。这通过浑度值随时间的流逝不断变化的对照样品实现,通常浑浊度仅减少。相同的时间过去之后,将对照样品的浑度值添加到测试样品的浑浊度值中,从报道的值中去除时间影响,从而仅反应溶剂的影响。表21.1-使用高剪切机器生产基于ONGC的废油表21.2-溶剂添加到上述废油的时间校正结果表21.3-使用高剪切机器生产基于椰油的废油表21.4-通过使用溶剂处理上述废油对于产自ONGC自由流动油的废油,其生产所需混合时间的影响比基于椰油的废油大。可观察到,2,500ppm的ONGC废油的浑浊度数值随着混合时间从1分钟增加到5分钟,从5,626NTU增加到9,894NTU。在相同条件下,对于基于椰油的废油,其从4,354NTU上升到4,856NTU。对产自ONGC自由流动油的废油,烃浓度增加对浑浊度数值的影响也比基于椰油的废油稍大。可以看到,添加甲苯不对椰油废油或ONGC废油产生帮助。尽管从废油中去除大量烃并将其与烃保留在最上层,甲苯不能减少这些废油的浑浊度数值。相反,尽管煮沸全部添加的溶剂,添加溶剂之后,浑浊度数值事实上升高。对于2,500废油,与废油混合5分钟相比,在废油混合1分钟的情况下浑浊度增加较多。溶剂总是通过在10,000RPM下混合1分钟添加到废油中。该混合可能进一步碎裂椰油和ONGC油现有液滴,且其可能通过增加超细液滴的种群密度增加浑浊度数值。与混合5分钟产生的废油相比,预料在通过1分钟混合产生废油的情况下进一步碎裂的影响更高。因此,我们发现1分钟混合之后的废油浑浊度数值增加更多。使用溶剂失败也可能因为消耗的大部分溶剂去除大量液滴。因此,在批次中,超细液滴可能额外需要溶剂来保持完整。可以看出,对于5,000ppm的废油,1分钟和5分钟废油的上升的差值超过我们实验范围而不能确立为最后数值。然而,对于5,000ppm基于椰油的废油,至少在煮出全部添加溶剂之后,其浑浊度数值随溶剂的使用上升。实验例-22单独离心在减少废油浑浊度方面的时间校正效果研究从报告的浑浊度结果中去除时间的影响之后的单独离心对废油浑浊度减少的影响。因此,使用自由流动ONGC油和椰油在表22.1和22.3中解释的参数下制备废油。表22.2和22.4展示3轮离心的时间校正结果和样品离心条件。每轮离心之后,仔细去除全部顶层积累油之后,测试浑浊度数值并记录时间。可理解的是时间校正结果的意义在实验例-21中已解释。表22.1-使用高剪切混合机器生产基于ONGC的废油SI号说明试验1试验2试验3试验41废油总重量(kg)0.490.500.510.502混合时间(min)15153混合RPM10,00010,00010,00010,0004废油中油含量(ppm)2,4962,4865,0014,9935检测浑浊度之前过去的时3.023.354.104.10间(min)6废油的平均浑浊度(NTU)5,911>10,000>10,000>10,000表22.2-上述基于ONGC的废油离心结果表22.3-使用高剪切混合机器生产基于椰油的废油表22.4-上述基于椰油的废油离心结果可以看出,相同条件下制备自自由流动ONGC油的废油浑浊度数值总比基于椰油制备的废油的浑浊度数值大。基于椰油的废油浑浊度随用于其制备的混合时间增加,也随存在于其中的烃浓度增加,且存在的烃浓度比混合时间的影响大。经发现,离心的时间调整效果大体上取决于初始浑浊度数值。随着每个相继的操作,其浑浊度逐步减少。可以看出,第一轮离心的影响较大。在相继的离心轮中,影响保持递减。可观察到的是因为液滴阻力影响小,离心在去除尺寸较大的油滴上更有效。可以看出,在第一轮中,对尺寸较大的液滴,浮力更好地工作,浑浊度大幅减小。可以看到由于一个或更多下述原因,离心变得无效。一旦分散油滴的尺寸变化变窄,离心会变得无效。第二,一旦分散液滴的种群密度随平均自由路径的增加下降,离心会变得无效。第三,当初始浑浊度数值太大时,离心会变得无效。第四,由于分散液滴可能带电,离心会变得无效。最后,由于油和水之间密度差异小,离心会变得无效。可确定的是液滴尺寸的变化变窄能导致所有液滴运动的速度和加速度相同。这能导致更少的碰撞和缓慢的聚集。离心功效也随着无尺寸较大的油滴的扫除影响而下降。此外,尺寸均匀的分散液滴比带有较大平均自由路径的小种群密度对离心的破坏更大。可以看出,初始浑浊度数值或超细液滴初始种群密度太高,离心下降,这然后损害离心功效。可以看出,当初始浑浊度数值太高时,第3次离心尝试之后剩余浑浊度还是大。结论是,离心不能减少废油浑浊度到所需值1NTU到4NTU。事实上,离心浑浊度数值的限制非常高。对有色废油的情况更是这样。进一步总结出,油和水之间的密度差异,还有离心中RCF和剩余时间在这方面起重要作用。实验例-23离心和单独溶剂对减少废油浑浊度的时间-溶剂-离心调整结合效果从所有报道的浑浊度结果中去除单独的时间、离心和其溶剂的影响之后,研究结合使用溶剂和离心对减少废油浑浊度的影响。因此,在表23.1和23.3给定的条件下制备废油。随后测量废油浑浊度数值。此后,在0(nil)剩余时间内在最大RCF4,500下将这些废油离心2次。此外,通过在10,000RCF下将其混入废油1分钟添加溶剂。此后,将这些物质再次以0保留时间在最大RCF4,500下离心。来自废油的剩余溶剂在废油中存在的游离水的帮助下,全部去除顶层溶剂和油之后,在温度范围为95℃到98℃下煮出。冷却之后,添加在剧烈沸腾过程中损失的补充水。之后,测试剩余材料的浑浊度数值并记录时间。为去除时间影响,我们添加一定量到上述结果,该量是如果我们让废油从其产生后在容器中保留相同时间,浑浊度数值减小的值。接着去除单溶剂影响,时间调整量被去除,对通过在10,000RPM下混合将溶剂添加到废油中,浑浊度数值增加。最后,去除单独离心的影响,我们将上述时间调整量添加到上述结果,在0剩余时间内在最大RCF4,500下将它们离心2次,废油浑浊度数值减少。表23.1使用高剪切混合机器生产基于ONGC油的废油表23.2通过结合使用溶剂和离心处理上述废油表23.3-使用高剪切混合机器生产基于椰油的废油表23.4通过结合使用溶剂和离心处理上述废油从表23.2中测试2、3、4和表23.4中测试3和4可以看出,我们无法获得数值,因为我们可以量化这些测试中添加到废油中的溶剂的影响,如从表21.2&21.4看到的。然而,未量化使用溶剂的影响,我们不能去除溶剂对这些测试的影响。然而,从测试1中对2,500ppm基于ONGC油的废油和从测试1和2中对1和5分钟的混合2,500ppm基于椰油的废油,可发现这2种单元操作仅当结合时减少废油的浑浊度。表23.2和23.4表明结合使用溶剂和使用该溶剂的离心有协同效果。实际上单独使用溶剂大幅增加废油浑浊度。仅当初始浑浊度数值不大时,单独使用离心较成功。但当溶剂与离心结合使用时,其不仅消除单独使用溶剂全部负面影响,而且在像ONGC废油一样,初始浑浊度数值较大的情况下额外的有利。可确定的是离心必须优选用于去除较大油滴,而溶剂必须用于去除超细液滴。溶剂必须仅在离心对需要的宽的液滴尺寸分布或细液滴的低种群密度或油和水之间的低密度差异不再有效之后添加。必须当废油初始浑浊度数值较大时使用该结合。实施例24使用明矾降低废油浑浊度的效果研究了明矾添加对降低废油浑浊度的影响。相应地,按照下述表24.1A和24.2A中述及的条件制备了具有低浑浊度和高浑浊度数值的废油样品。按照表24.1B和24.2B中述及的数字添加明矾并设置静置时间。针对高浑浊度的样品以3个不同的比例添加明矾,4天后评价浑浊度数值,调节或者不调节时间影响。明矾对低ppm废油的效果表24.1A-使用高剪切力混合机器制造废油表24.1B-明矾对上述废油的影响明矾对高ppm废油的效果表24.2A-使用高剪切力混合机器制造废油表24.2B-明矾对上述废油的影响不同组分的明矾对废油的效果表24.3A-使用高剪切力混合机器制造废油SI号说明试验1试验2所用油名称ONGC自由流动油椰油1废油总重量(kg)0.490.502混合时间(min)553混合RPM10,00010,0004废油中的油含量(ppm)2,4982,4965检测浑浊度前经过的时间(min)1.982.186废油的平均浑浊度(NTU)>10,0004,740表24.3B-不同比例的明矾添加到废油中可以看出,当起始浑浊度较大时,明矾在24小时内对降低废油浑浊度的影响较大。正如表24.2B中看到的,随着除去时间的影响,可以看到,明矾单独对废油浑浊度数值降低的影响约比时间本身影响大1.5倍。正如从表24.3B看到的,当起始浑浊度数值大于10,000NTU时,添加0.05wt%的明矾并不足够。明矾的添加量必须增加到0.1wt%。然而,超过0.1wt%的明矾添加量,没有看到更进一步的改善。因此,可以确定,只有当人们想要在一天或两天内得到快速结果时明矾的添加数量才是重要的。如果给定24小时,明矾和时间的组合影响足够多地将浑浊度值从大于10,000NTU降低到约5.5NTU。然而,经发现,随后从水中除去明矾污染的油层相当困难。此外,油的热值降低2%,正如下面实施例29中所示。此外,可以看出,随着来自明矾的污染,油中碱含量增加。也已经观察到,随着其中存在的每wt%的明矾,油的粘度极大地改变。实施例25明矾、加热与时间的组合使用对降低废油浑浊度的效果目的在于评价明矾、加热与时间的组合使用对降低废油浑浊度的影响并将其与只用明矾和时间的使用影响进行比较。因此,低浑浊度的废油样品按照表25.1中述及的条件制备。之后,加入明矾并保持一部分样品在环境条件下,在从3小时到5.8小时的不同时间测试了它们的起始浑浊度和最终浑浊度。样品的剩余部分在炉中于80℃加热从1到4小时的不同时间,甚至这些也被测试起始浑浊度和最终浑浊度数值。随后,对加热的样品加入补足水以补给蒸发水。表25.1-使用高剪切力混合机器制造废油表25.2-加入明矾并加热上述废油从表25.2可以看出,发现明矾、加热和时间对降低低浑浊度ONGC和椰油基废油的浑浊度数值的组合影响要远好于单单明矾和时间的影响。在试验1中,可以看出,在未加热加入明矾的废油情况下,浑浊度数值在5.04h内下降了73%。然而,当加入明矾的废油在80℃加热4小时时,废油的浑浊度在5.11小时降低了93%。在试验2,3和4中,当未加热时,实际上发现浑浊度数值分别在5.84,3.44,和4.56小时内增加了2.3%,35.3%和9.6%。当加入明矾的废油未加热,具有较低的起始浑浊度和较少的静置时间时,废油的浑浊度数值实际上随着时间比它们的起始数值生长的多得多。然而相反,在加入明矾的废油样品于80℃加热,甚至具有56.1NTU的低起始浑浊度数值以及甚至具有1小时的较少时间的情况下,浑浊度数值降低67%。此外,对于42.1NTU的起始浑浊度数值和在80℃加热4小时,在5.11小时内下降93%。可以确定,样品加热经历的时间长度越长,浑浊度数值下降得越快。该试验确定的事实是,必要时通过施加低强度的热量,用明矾处理能够加速减少整体的处理时间。实施例26过滤对降低废油浑浊度的影响为了评估快和慢的过滤速度对降低高和低的起始浑浊度废油的浑浊度数值影响,按照表26.1中述及的条件废油样品。这些样品使用40和41级沃特曼(Whatman)纤维素过滤纸重复过滤4次。在一组读数中,重复使用相同的过滤纸,而在另一组读数中,每次使用新的过滤纸。在每次过滤之前和之后,记录浑浊度数值。对于过滤给定重量的废油花费的时间每次也进行记录以得到过滤比率。表26.1-使用高剪切力混合机器制造废油SI号说明试验1试验2所用油名称ONGC自由流动油椰油1废油总重量(kg)0.490.512混合时间(min)553混合RPM10,00010,0004废油中的油含量(ppm)2,4982,4975检测浑浊度前经过的时间(min)4.703.726废油的平均浑浊度(NTU)9,3564,434表26.2-对于上述废油使用沃特曼(Whatman)过滤纸的过滤过程可以看出,具有8微米孔径的40级沃特曼(Whatman)过滤纸在每次过滤后都给出了更低的浑浊度,然而发现过滤很慢。当每次重复使用相同的滤纸时,甚至过滤更慢。也发现在高浑浊度的废油情况下要慢得多。可以观察到,随着重复使用相同的过滤纸,过程减慢了但过滤质量改善了,以便得到低浑浊度数值。可以看出,每次过滤不能给出一致结果。过滤比率每次改变且相应地浑浊度数值降低也改变。可以看出,过滤效率依赖于废油中烃的性质。例如,正如表26.2中看到的,对于椰油基废油,过滤要比ONGC基废油低效得多。然而,可以看出,除了作为降低最后少量的浑浊度数值的完成步骤,由于以下一个或多个原因,发现过滤是期望的工业过程。首先,过滤过程发现是非常慢的过程。其次,过滤过程是不一致的过程。第三,当孔径较小时,发现过滤介质很快堵塞,从而使进一步的过程甚至更慢。第四,废油中的烃不能容易地回收或成可销售形式。最后,废油中的固体存在进一步损害了该过程的效率和流速。实施例27明矾和过滤的组合使用对降低废油浑浊度的效果为了评估明矾和过滤的组合使用对具有低和中浑浊度数值的废油浑浊度的影响,在下表27.1A和27.2A中述及的条件下制备了废油样品。在测试起始浑浊度数值后向这些样品中加入0.05wt%的明矾。在密闭到24小时后,重新测试这些样品的浑浊度数值。此外,依次用41级和40级沃特曼(Whatman)纤维素过滤纸过滤样品,每次过滤后记录浑浊度数值的降低。明矾和过滤对低ppm废油浑浊度的效果表27.1A-使用高剪切力混合机器制造废油表27.1B-通过添加明矾,然后用沃特曼(Whatman)纤维素过滤纸过滤来处理上述废油明矾和过滤对高ppm废油浑浊度的效果表27.2A-使用高剪切力混合机器制造废油表27.2B-通过添加明矾,然后用沃特曼(Whatman)纤维素过滤纸过滤来处理上述废油可以看出,对于具有较大起始浑浊度数值的废油,在相同时间段和用相同的剂量,明矾的百分比的影响大很多,这可通过比较表27.IB和27.2B看出来。进一步可以看出,明矾能够使用离心和大量的溶剂。但是它是不真实的。这是因为明矾花费相同的时间和剂量来将废油的浑浊度从4,755NTU降低到45NTU,及从45NTU降低到4.5NTU。明矾需要降低浑浊度直到2-5NTU。因此,可以确定,对明矾而言起始浑浊度必须低于60-70NTU。一旦浑浊度数值从2-5NTU降低,然后观察到更快的过滤对于传送约1NTU的水是非常有效的,且此外观察到过滤介质的负载或阻隔较小。其次,发现明矾对于从废油收集的油的质量有不良影响。因此,可以确定,如果收集的油的质量不重要且如果能够忽略过滤和过滤介质饱和所花费的时间,那么就废油处理而言,明矾和过滤能够使用离心和大量溶剂。实施例-28组合使用离心、溶剂、明矾和过滤以及用不同溶剂对不同废油浑浊度的综合效果目的在于评估离心、溶剂、明矾和过滤对降低由不同油/烃类制备的废油浑浊度的组合效果以及不同溶剂对浑浊度降低的效果。因此,按照表28.1A,28.2A,28.3A,28.4A,28.5A,28.6A和28.7A中述及的条件进行废油的制备。制备过程也描述在表28.1B,28.2B,28.3B,28.4B,28.5B,28.6B和28.7B中。随后,溶剂如甲苯和二甲苯以不同比例混合使用。使用高剪切力混合机以8,090RPM将溶剂与废油混合1分钟。废油中的油含量从5PPM到4,99,052PPM之间变化。使用的不同油选自以下的一种或多种:椰油、炉油、柴油、ONGC自由流动油和ONGC粘稠烃。随后,依次使用包括使用离心、溶剂、明矾和过滤的所有四个处理步骤。因此,进行如下观察。椰油基废油表28.1A-使用高剪切力混合机器制造椰油基废油表28.1B-通过组合使用离心、溶剂、明矾和过滤来处理上述废油表28.2A-使用高剪切力混合机器制造椰油基废油表28.2B-通过组合使用离心、溶剂、明矾和过滤来处理上述废油炉油基废油表28.3A-使用高剪切力混合机器制造炉油基废油表28.3B-通过组合使用离心、溶剂、明矾和过滤来处理上述废油柴油基废油表28.4A-使用高剪切力混合机器制造柴油基废油SI号说明试验1试验2试验31废油总重量(kg)0.510.490.522混合时间(min)13.5313.4213.483混合RPM8,0908,0308,1304废油中的油含量(ppm)2,4922,4997,4425检测浑浊度前经过的时间(min)5.473.453.576废油的平均浑浊度(NTU)3,4423,8529,702表28.4B-通过组合使用离心、溶剂、明矾和过滤处理来自表28.4A的废油ONGC自由流动油基的废油表28.5A-使用高剪切力混合机器制造ONGC油基的废油表28.5B-通过组合使用离心与溶剂、明矾和过滤处理上述废油表28.6A-使用高剪切力混合机器制造ONGC油基废油表28.6B-通过组合使用离心、溶剂、明矾和过滤处理来自表28.6A的废油粘稠ONGC烃表28.7A-使用高剪切力混合机器制造粘稠ONGC烃基废油SI号说明试验1试验2试验31废油总重量(kg)0.490.490.512混合时间(min)5.005.005.003混合RPM10,00010,00010,0004废油中的粘稠烃含量(ppm)2,4884,9959,9995废油中的油含量(ppm)1,2322,4744,9526废油中的灰分含量(ppm)2064138277废油中的结合水(ppm)1,0502,1084,2208检测浑浊度前经过的时间(min)3.907.194.309废油的平均浑浊度(NTU)1,6373,2728,633表28.7B-通过组合使用离心、溶剂、明矾和过滤处理上述废油可以观察到,当废油中存在不溶于水的固体时,正如包含ONGC粘稠烃类的那些,有必要在加入明矾后包含油过滤以得到低的浑浊度,因为过滤在除去极细的灰分颗粒方面更有效。这能够从表28.7B中看到,进一步确定的是柴油废油是最容易处理的。此外,可以看出,过程中包括所有四个单元的操作如离心、加入溶剂、加入明矾随后过滤使得废油处理更快,具有较少的操作问题和优良的结果。此外,可以看出,发现污染问题全部减轻。另外,可以发现,所述的操作全部回收几乎优质的烃类和水以供使用或销售。发现能量消耗是极小的。此外,使用的溶剂以其起始形式完全回收供重复使用。可以看出,需要的溶剂数量以及溶剂加入模式依赖于废油中存在的烃的数量。当烃类很多时,需要的溶剂数量更多,加入溶剂的同时需要搅拌。可以看出,当废油中的烃含量较高,正如表28.6B的测试4中所清楚看到的,仅仅手动摇晃是优选的加入溶剂的模式。也可以看出,即使轻柔的手动摇晃同样是有效的。也可以看到的是,随着烃类的收集,溶剂使用变得非常容易。收集的重量百分比也上升。最后,可以看到的是,通常的溶剂及油层中具有非常少的水。实施例29本发明的方法对包含极高烃含量的废油的作用目的在于研究组合方法对具有极高烃含量包括回收的烃类和溶剂的废油的作用。因此,在如下表29.1中述及的条件下使用椰油制备废油。这些废油样品保留在分离烧瓶中48小时,导致形成三个层。获得的顶层包含纯油。获得的中层包含油和水两种,而底层大部分包含其中具有极少油的水。按如下所述,除去底层并处理废油以及来自中层的废油。中层用明矾处理并保留在分离烧瓶中另外48小时,导致进一步形成三个层,即包含纯油的顶层,包含油和明矾以及水的中层和废油的底层。干燥含明矾的层并测试热值。从顶层和中层回收的纯椰油的重量百分比和干明矾层的热值可在表29.2中看到,同时废油的处理结果以及椰油和溶剂的回收重量百分比可在表29.3中看到。表29.1-使用高剪切力机器制造椰油基废油SI号说明试验1试验21废油总重量(kg)0.500.502混合时间(min)553混合RPM10,00010,0004废油中的油含量(ppm)95,921240,1505检测浑浊度前经过的时间(min)5.304.826废油的平均浑浊度(NTU)>10,000>10,000表29.2-从不同部分收集的油部分SI号说明试验1试验21从最顶层收集的油的重量百分比16.3833.682从中层收集的油的重量百分比63.6054.163从中层获得的浮渣的热值(kcal/kg)-8,6824起始椰油的热值(kcal/kg)8,9728,9725附着到不同表面损失的油的重量百分比7.198.82表29.3-通过组合使用离心、溶剂、明矾以及过滤处理底层废油可以观察过,对于给定的烃,废油中烃的总量越高,利用静置分离出纯烃就越容易。此外,可以观察到,除了使其粘稠并增加其碱含量和灰分含量之外,椰油中明矾的存在降低了其热值3.2wt%。实施例-30使用本发明的整个方法从大量样品中定性和定量回收烃、溶剂以及水目的在于通过评价回收的烃、溶剂和水的数量和质量研究本发明的方法对大规模废油的作用。因此,废油样品按照表30.1中述及的条件制备。然后按照表30.2中述及的方法处理废油。随后,从表30.2中的步骤3除去的烃类和溶剂层接着按照实施例15和实施例16中述及的方法处理。获得的结果清楚地在表30.3中显示。表30.1-使用高剪切力混合机器制造粘稠ONGC烃类基废油表30.2-通过组合使用离心、溶剂、明矾和过滤处理上述废油以及回收油表30.3-从油中分离溶剂表30.4-测试结果可以观察到,从上述废油中定性以及定量回收溶剂和水是极好的。可以进一步看到,少部分烃类随着溶剂沸腾出,从而降低了其回收的重量百分比。最后,可以看出,ONGC烃类中的湿度可能是较低的,如果所述方法已经选择用于热静置超过48小时。最后,可以观察到,从粘稠烃类中除去游离水是十分困难的。已经以例示的方式对本发明进行了描述,可以理解的是,使用的术语旨在描述性的,而非限制性的。本发明并不旨在详尽的或去限制本发明为公开的精确形式。根据上述教导,许多修改和验证是可能的。本发明意在本发明的保护范围并不受该详细说明的限制,而仅受到所附权利要求的限制。也可以理解的是,以下的权利要求旨在覆盖所有本文描述的本发明的一般特征和特定特征。