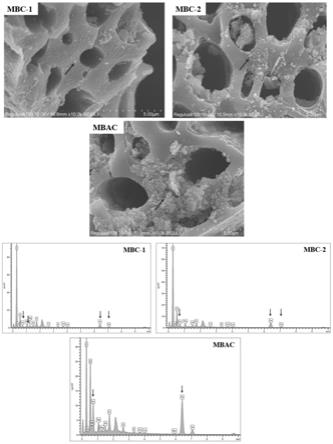
1.本发明属于磁性生物炭技术领域,具体涉及一种磁性活性生物炭的制备方法及应用。
背景技术:2.生物炭由于具有多孔、比表面积大、吸附能力强等特点而被广泛应用于重金属的去除。对生物炭进行磁改性一方面可增加吸附活性位点和酸性官能团含量,增强表面极性,有利于重金属的吸附,另一方面经磁改性后的生物碳可通过外加磁场方式实现材料的快速分离,达到污染物质从环境中彻底去除的目标。
3.常用的生物炭负磁方法如浸渍热解法、液相沉淀法等。申请号cn202010964672.x专利中披露了一种通过浸渍热解法制备生物炭的方法:将生物质材料和铁盐充分浸渍,充分烘干后高温热解。但是浸渍热解法虽实现了负磁和热解同时完成,但过量的金属氧化物在热解后会导致生物炭表面、孔隙中被磁性材料挤占,阻隔了生物炭与重金属离子的接触,进而影响其吸附效果。申请号cn201610360584.2专利中披露了一种通过共沉淀法制备磁性谷壳生物炭的方法:将fecl3和fecl2溶解到hcl溶液中,再将其与以生物炭和氨水溶液混合,经沉淀形成磁性谷壳生物炭。而共沉淀法虽反应过程简单,但磁性氧化铁与炭之间的结合相对松散、磁力不稳定,无法实现生物炭和污染物的有效回收。
4.因此,亟需开发一种负磁物质用量少,但载磁效率高,磁性结构稳定、易重复利用的新型磁性生物炭的制备方法。
技术实现要素:5.本发明为了克服现有技术中存在的缺陷,提供了一种磁性活性生物炭的制备方法,通过膨化预处理技术产生的高温高压作用,在热解过程中通过水蒸气的高温活化作用,增强负磁稳定性,保证磁回收效率。最终获得负磁效率高且结构稳定的磁性活性生物炭复合材料。
6.第一方面,本发明提供了一种活性磁性生物炭的制备方法,所述制备方法包括以下步骤,
7.(1)将秸秆剪碎至2-3cm,蒸馏水反复清洗后烘干至恒重;所述秸秆是常见的成熟农作物的茎、叶、枝梗等部分,可以小麦、水稻、玉米等。
8.(2)在烘干后的秸秆中加入fe
2+
与fe
3+
混合铁盐进行搅拌浸渍,超声分散,水浴蒸干至含水率40~70%备用;
9.(3)将水浴蒸干后的秸秆进行膨化干燥预处理;
10.(4)将获得的膨化物在氮气保护下进行热解,待热解后样品冷却至室温研磨后过筛,获得磁性生物炭;
11.(5)将得到的磁性生物炭进行水蒸气活化,得磁性活性生物炭。
12.进一步地,所述烘干的温度为55-70℃。
13.进一步地,所述fe
2+
与fe
3+
混合铁盐为feso4·
7h2o和fecl3·
6h2o混合溶液,所述fe
2+
与fe
3+
的物质的量比为1:2,所述秸秆与所述混合铁盐的质量比为(5-10):1,所述搅拌浸渍时间为15min,超声时间2h,超声温度为室温,水浴温度为75℃。
14.进一步地,所述膨化条件为:膨化温度为90℃,停滞时间为10min,压差为0.1~0.2mpa,真空干燥温度为70℃,真空干燥时间为120min。
15.进一步地,所述热解在管式炉中进行,管式炉升温速率10℃1min1氮气流速50ml1min,热解温度300-500℃,保持2h。
16.进一步地,所述水蒸气活化具体为在管式炉中通入氮气直至达到活化温度,达到活化温度后将所述氮气转换为水蒸气,活化温度与热解温度相同,活化时间为通入水蒸气质量与水蒸气流速比。
17.进一步地,所述水蒸气活化在管式炉中进行,所述管式炉升温速率50℃1min,氮气流速50ml1min,水蒸气流速1ml1min,通入水蒸汽质量与磁性生物炭的质量比为2~4:1。
18.进一步地,所述制备方法还包括,将得到的磁性活性生物炭冷却后分别用乙醇和蒸馏水清洗3次,60℃烘干备用。
19.第二方面,本发明提供了一种采用本发明第一方面所述的磁性活性生物炭的制备方法制得的磁性活性生物炭。
20.第三方面,本发明还提供了本发明第二方面所述的磁性活性生物炭在作为吸附剂中的应用。
21.本发明相对于现有技术而言,具有以下技术效果:
22.1、本发明采用膨化技术对秸秆进行处理,通过膨化处理产生的实现瞬时高温高压作用,使秸秆内部纤维体积膨胀增大,有效提高了秸秆纤维素包裹结构的松散程度,可以明显增强具磁物质铁盐的渗透能力,使得铁盐能够最大程度的被膨化秸秆均匀吸持,并且紧密的结合在生物质材料表面。
23.2、本发明在热解过程中通过水蒸气的高温活化作用,实现了对纤维材料的造孔和扩孔的同时将裸露在生物炭材料表面的铁离子进一步氧化为铁氧化物,增强其负磁稳定性,保证污染物有效去除的同时实现了吸附材料的重复利用。
24.3、通过本发明的方法制得的磁性活性生物炭,其负磁物质用量少,且载磁效率高,磁性结构稳定,在实际应用中可通过再生回收技术对磁性活性生物炭进行重复利用,降低其使用成本,是一种新型的磁性活性生物炭符合材料。
附图说明
25.为了更清楚地说明本发明具体实施方式或现有技术中的技术方案,下面将对具体实施方式描述中所需要使用的附图作简单地介绍。
26.图1为不同磁性生物炭的扫描电镜图及对应能谱图;
27.图2为不同磁性生物炭的磁滞回线;
28.图3为不同磁性生物炭对cd
2+
的去除率;
29.图4为不同磁性生物炭对cd
2+
的吸附曲线;
30.图5为不同磁性生物炭的连续吸附-再生对cd
2+
的去除率。
具体实施方式
31.下面将结合附图对本发明技术方案的实施例进行详细的描述。以下实施例仅用于更加清楚地说明本发明的技术方案,因此只是作为示例,而不能以此来限制本发明的保护范围。需要注意的是,除非另有说明,本技术使用的技术术语或者科学术语应当为本发明所属领域技术人员所理解的通常意义。
32.实施例1
33.将水稻秸秆剪碎至2-3cm,用蒸馏水反复清洗后置于烘箱60℃烘干。
34.称取1.83gfeso4·
7h2o和3.33g fecl3·
6h2o分别溶解后混合定容至100ml,加入烘干水稻秸秆7g,搅拌10min后再进行超声分散,超声时间2h,后将其在水浴锅加热,水浴温度75℃,加热至秸秆鲜重约10.5g。
35.将该样品置于膨化罐中进行膨化预处理。膨化罐参数设置:膨化温度90℃,停滞时间为10min,压差0.1mpa,真空干燥温度为70℃,真空干燥时间为120min。
36.将样品置于管式炉中在氮气氛围下进行热裂解,升温速率10℃1min,氮气流速50ml1min,热解温度500℃,保持时间2h。热解结束取出样品研磨过0.25mm筛,并进行称重,磁性生物炭样品质量6.75g。
37.将样品重新置于管式炉中,期间按照氮气流速50ml1min通氮气,按照50℃1min的升温速率升温至500℃立即转通水蒸气,水蒸气流速1ml1min,水蒸气通入质量与磁性生物炭的质量比为4:1,即保持活化时间27min。
38.活化结束后将样品分别用蒸馏水和乙醇清洗3次,置于烘箱中60℃烘干,获得磁性活性生物炭,样品标记为mbac。
39.实施例2
40.将水稻秸秆剪碎至2-3cm,用蒸馏水反复清洗后置于烘箱60℃烘干。
41.称取1.83gfeso4·
7h2o和3.33g fecl3·
6h2o分别溶解后混合定容至100ml,加入烘干水稻秸秆7g,搅拌10min后再进行超声分散,超声时间2h,后将其在水浴锅加热,水浴温度75℃,加热至秸秆鲜重约10.5g。
42.将样品置于管式炉中在氮气氛围下进行热裂解,升温速率10℃1min,氮气流速50ml1min,热解温度500℃,保持时间2h,热解结束取出样品研磨过0.25mm筛。
43.将样品分别用蒸馏水和乙醇清洗3次,置于烘箱中60℃烘干,获得磁性生物炭,样品标记为mbac-1。
44.实施例3
45.将水稻秸秆剪碎至2-3cm,用蒸馏水反复清洗后置于烘箱60℃烘干。
46.称取1.83g feso4·
7h2o和3.33g fecl3·
6h2o分别溶解后混合定容至100ml,加入烘干水稻秸秆7g,搅拌10min后再进行超声分散,超声时间2h,后将其在水浴锅加热,水浴温度75℃,加热至秸秆鲜重约10.5g。
47.将该样品置于膨化罐中进行膨化预处理。膨化罐参数设置:膨化温度90℃,停滞时间为10min,压差0.1mpa,真空干燥温度为70℃,真空干燥时间为120min。
48.将样品置于管式炉中在氮气氛围下进行热裂解,升温速率10℃1min,氮气流速50ml1min,热解温度500℃,保持时间2h,热解结束取出样品研磨过0.25mm筛。
49.将样品分别用蒸馏水和乙醇清洗3次,置于烘箱中60℃烘干,获得磁性生物炭,样
品标记为mbac-2。
50.效果例1
51.通过带能谱的电镜扫描针对分别采用实施例1-3制备方法制得的磁性生物炭复合材料mbac、mbac-1、mbac-2进行表面形态和表面元素分析,如图1所示,三种磁性生物炭的表面相对粗糙,且表面和通道内部分布了数量不一的碎屑和细颗粒物(如箭头所示),为形成的铁氧化物附着其中。进一步地通过对其表面元素进行扫描分析发现三种磁性生物炭mbac-1、mbac-2、mbac的能谱图中有明显的fe的峰,占到总元素的比例(w1w)分别为4.95%、6.10%和17.64%,说明fe成功负载于生物炭表面,且经膨化预处理和水蒸气活化过程协同制备获得的磁性生物炭mbac的铁元素占比最高。
52.效果例2
53.实施例1制备的磁性活性生物炭,以及实施例2-3制备的磁性生物炭材料的理化性质进行检测,制备的磁性活性生物炭mbac的质量为6.68g,产率54.9%,mbc-1和mbc-2的质量分别为5.25g和5.72g,产率为43.2%和47.0%。三种生物炭理化性质如表1所示,
54.表1磁性生物炭的理化性质
[0055][0056]
从表1中可以看出,在制备过程中不进行膨化预处理及水蒸气活化制备获得的磁性生物炭,也就是采用本领域常规的制备方法获得的磁性生物炭,其在比表面积、孔径、孔隙率及磁化强度等方面都表现一般;在制备过程中采用了膨化预处理获得的磁性生物炭,其在比表面积、孔径、孔隙率及磁化强度等方面都有所增加;在制备过程中同时采用膨化预处理和水蒸气活化制备获得的磁性活性生物炭,比表面积、孔径、孔隙率及磁化强度等方面都明显的增加,相对于传统制备方法获得的磁性生物炭mbc-1而言,比表面积增加133.2%,孔径增加28.1%,孔隙率增加20.3%。在磁化强度方面,图2是上述三种生物炭的磁滞回线,从中可以看出三种生物炭的磁滞回线均经过原点且呈中心对称,说明三种材料均具有超顺磁性,可进行回收利用。但其中采用膨化预处理和水蒸气活化制备获得的磁性生物炭的饱和磁化强度值为17.69emu1g,较传统不进行膨化预处理及水蒸气活化制备获得的磁性生物炭的磁性强度增加近11倍,说明在使用等量铁盐浸渍的情况下,利用膨化预处理和水蒸气活化不仅增加了磁性生物活性炭的比表面积和孔隙率而且使得更多的磁性物质吸附在生物炭孔道中,大幅度提高样品的磁化强度,进而提高材料的负磁效率,更有利于分离。
[0057]
实施例4
[0058]
将水稻秸秆剪碎至2-3cm,用蒸馏水反复清洗后置于烘箱60℃烘干。
[0059]
称取2.78g feso4·
7h2o和5.406g fecl3·
6h2o分别溶解后混合定容至100ml,加入烘干水稻秸秆13.44g,搅拌10min后再进行超声分散,超声时间2h,超声温度为室温。后将其进行水浴加热,水浴温度75℃,水浴加热至秸秆鲜重约22g。
[0060]
样品置于膨化罐中进行膨化预处理。膨化罐参数设置:膨化温度80℃,停滞时间为10min,压差为0.1mpa,真空干燥温度为70℃,真空干燥时间为120min。
[0061]
样品置于管式炉中在氮气氛围下进行热裂解,升温速率10℃1min,氮气流速
50ml1min,热解温度400℃,保持时间2h。热解结束磁性生物炭样品研磨过筛,并进行称重,重量为14.05g。
[0062]
将样品重新置于管式炉中,期间按照氮气流速50ml1min通氮气,按照50℃1min的升温速率升温至400℃立即转通水蒸气,水蒸气流速1ml1min,水炭质量比为4倍,依据热解后的磁性生物炭样品质量确定需要的水蒸气质量56.2ml,活化时间56min。
[0063]
活化结束后将样品分别用蒸馏水和乙醇清洗3次,置于烘箱中60℃烘干,获得磁性活性生物炭mbac-0.1-4。
[0064]
实施例5
[0065]
本实施例制备方法相对于实施例4制备方法的而言,仅将膨化处理的压差设置为0.2mpa,其中热解后的磁性生物炭质量为14.22g,故需要的水蒸气质量56.88ml,活化时间57min,其他步骤与实施例4相同,制备获得磁性活性生物炭mbac-0.2-4。
[0066]
实施例6
[0067]
本实施例制备方法相对于实施例5制备方法的而言,仅将水炭质量比设置为2:1,故需要的水蒸气质量28.44ml,活化时间28min,其他步骤与实施例4相同,制备获得磁性活性生物炭mbac-0.2-2。
[0068]
效果例3
[0069]
对实施例4-6中的3种磁性活性生物炭样品进行水体cd
2+
的去除实验,具体操作如下:
[0070]
称取2.7441g cd(no3)2·
4h2o溶解定容于100ml,得到cd
2+
浓度为10g1l的母液。(1)吸附动力学试验:用0.01m的kno3作为平衡电解质将母液稀释至50mg
·
l-1
,分别称取50mg mbac-0.1-4、mbac-0.2-4、mbac-0.2-2于50ml离心管中,加入20ml浓度50mg1l cd
2+
,在恒温往复式摇床中以220r1min振荡,分别在0.5h、2h、6h、12h、24h取样,利用磁铁将磁性生物活性炭从水体中分离,测定上清液cd
2+
浓度,计算磁性活性生物炭对cd
2+
的去除率。(2)等温吸附试验:用0.01m的硝酸钾作为平衡电解质将母液进行稀释至浓度分别为10、20、50、100、200、500mg1l。分别称取50mg mbac-0.1-4、mbac-0.2-4、mbac-0.2-2于50ml离心管中,加入20ml不同浓度cd
2+
溶液振荡24h后过滤测定上清液cd
2+
浓度。
[0071]
如图3所示,3种磁性活性生物炭对cd
2+
的吸附量随着吸附时间的增加逐渐增加,在24h后,去除率mbac-0.1-4、mbac-0.2-4、mbac-0.2-2对cd
2+
的去除率均超过90%,分别为92.2%、96.9%、97.1%,说明用本方法制备的磁性生物炭对cd
2+
具有良好的吸附效果。当活化的水炭质量比4:1时,膨化预处理压差为0.2mpa条件下对cd
2+
的去除效率(96.9%)高于0.1mpa(92.2%),说明增大膨化压差有利于cd
2+
的去除;当膨化预处理压差为0.2mpa时,活化的水炭质量比2:1条件下对cd
2+
的去除效率(97.1%)与水炭质量比4:1下的基本接近(96.9%)。
[0072]
利用langmuir等温吸附曲线qe=k
lqmce
1(1+ce)对4种磁性活性生物炭的吸附过程进行拟合并计算最大吸附量。qe表示平衡时的吸附量(mgg-1
),ce表示平衡时的溶液浓度(mg
·
l-1
),qm表示最大吸附量(mg
·
g-1
),k
l
表示吸附材料表面对cd的结合力(l
·
mg-1
)。拟合结果如图4和表2所示,langmuir等温吸附曲线可以很好地拟合三种磁性生物炭对cd
2+
的吸附过程,相关系数r2为0.989~0.993,说明磁性生物炭对cd
2+
的吸附以化学吸附为主;mbac-0.1-4、mbac-0.2-4、mbac-0.2-2对cd
2+
的最大吸附量分别为48.80、57.07和63.80mg1g。
mbac-0.2-2的最大吸附量最高,说明说明增大膨化压差可提高磁性生物炭对cd
2+
的最大吸附量,而增加水炭比会在一定程度上降低对cd
2+
的最大吸附量。
[0073]
结合3种磁性生物炭对cd
2+
的去除率结果,说明设置膨化压差0.2mpa、活化水炭比2:1时所制备磁性活性生物炭具有更高cd
2+
吸附量和去除率。在不影响磁性生物炭去除效率的条件下为了缩短制备时间,建议将水炭比设置为2:1即可。
[0074]
表1不同磁性活性生物炭对cd
2+
的吸附等温参数
[0075][0076]
为探究磁性活性生物炭的再生利用性能,用磁铁回收等温吸附试验中平衡吸附cd
2+
的4种磁性活性生物炭(cd
2+
初始浓度50mg
·
l-1
)后超纯水洗净烘干。用1mol1l的硝酸溶液按照固液1:100(g:ml)分别与4种磁性活性生物炭混合,于25℃、220r1min振荡培养箱中解吸24h,洗净烘干后再重复一次吸附实验(cd
2+
浓度50mg
·
l-1
),连续进行5次吸附-再生。取吸附后的上清液测定cd
2+
浓度,计算每次磁性活性生物炭的去除率。
[0077]
如图5所示,用硝酸可以较好地解吸被磁性活性生物炭吸附的cd
2+
,4种类型的磁性活性生物炭对cd
2+
的吸附过程是可逆的且再生吸附性能良好。在经过连续吸附-再生的4个周期后,mbac-0.1-4、mbac-0.2-4、mbac-0.2-2对cd
2+
的去除率分别为50.6%、47.8%和52.1%,基本都保持在50%左右,表明磁性活性生物炭的吸附性能较为稳定。在实际的应用中,可通过再生回收技术对磁性活性生物炭进行重复利用,降低其使用成本,并对重金属进行回收。
[0078]
综上,本方法所制备的磁性活性生物炭可实现对重金属的快速高效吸附,且磁性结构稳定,易重复再生利用,在实际应用中具有明显优势。
[0079]
除非另外具体说明,否则在这些实施例中阐述的数值并不限制本发明的范围。在这里示出和描述的所有示例中,除非另有规定,任何具体值应被解释为仅仅是示例性的,而不是作为限制,因此,示例性实施例的其他示例可以具有不同的值。