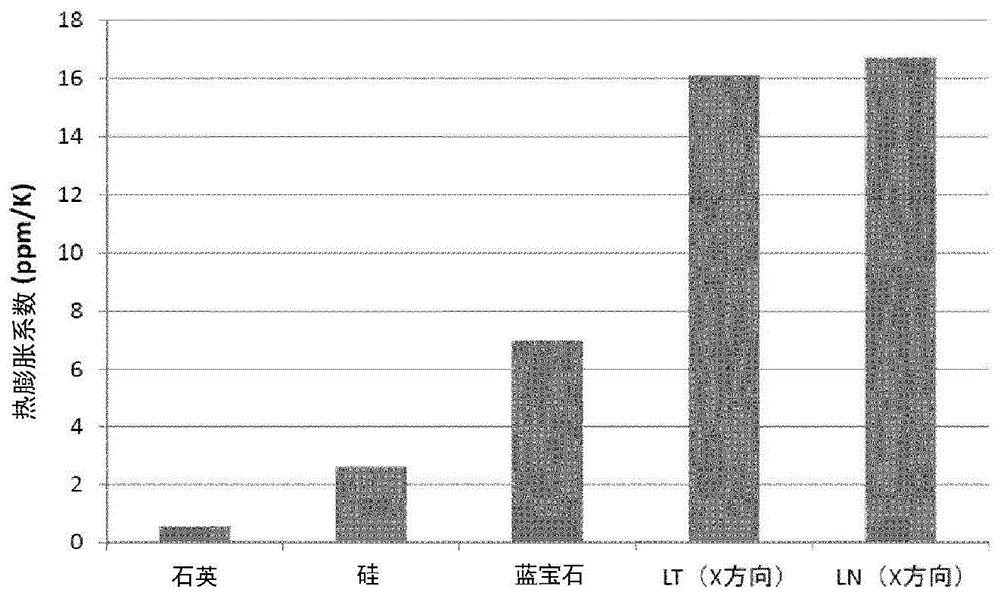
本发明涉及复合基板、表面弹性波器件及复合基板的制造方法。
背景技术:
:近年来,在以智能手机为代表的移动体通信的市场中,通信量急剧增大。在为了应对该问题而增加所需的波段数的过程中,各种部件的小型化、高性能化不可避免地逐渐成为必须。作为普通的压电材料的钽酸锂(lithiumtantalate:有时也简称为lt)或铌酸锂(lithiumniobate:有时也简称为ln)被广泛用作表面弹性波(saw)器件的材料,这些材料具有大的机电耦合系数,可实现宽频带化,但是另一方面,具有如下这样的问题点,即:温度稳定性低,由于温度变化导致能够对应的频率发生偏移。这起因于钽酸锂、铌酸锂具有非常高的热膨胀系数。为了减少该问题,提出了在钽酸锂(lt)或铌酸锂(ln)等压电单晶贴合蓝宝石、硅(si)等膨胀系数小的材料,并通过磨削等将压电单晶侧薄化为几μm~几十μm的方法。图1为对各种材料的热膨胀系数进行对比表示的曲线图。通过贴合膨胀系数小的材料来抑制压电单晶的热膨胀,温度特性得到改善(例如,参照非专利文献1)。但是,该方法存在如下这样的问题,即:由于将薄的压电单晶膜层叠于支承基板,从而在反谐振频带中产生被称为寄生或纹波的噪声。该噪声是由于来自压电单晶膜与支承基板的界面反射而产生的。作为例子,图2示出了由在硅基板上层叠有20μm厚的lt膜的复合基板制成的谐振器中的反射系数(s11)的频谱的实例。在图2中,将频谱的波峰与波谷之差定义为寄生强度(amplitude)。为了解决该问题,提出了几种方法。例如,在非专利文献2中,公开了用1000号的磨削石使lt的贴合面粗糙化,得到算术平均粗糙度(ra)为300nm的粗糙度后,通过粘合剂与支承基板进行贴合的方法。但是,在该方法中使用有机物粘合剂进行贴合,从可靠性的观点出发存在问题。具体而言,预定在贴合后在基板表面进行图案形成,进行切割,将芯片安装于器件的多个工序,但是在该过程中会反复进行加热到250~400℃的处理。结果,构成粘合剂的有机物发生变质,导致贴合基板的压电晶体膜剥离或产生裂纹这样的问题发生。因此,存在如下方法:在形成有凹凸构造的压电单晶基板形成由无机材料构成的中间层,使得夹着该中间层来接合支承基板。作为用作中间层的无机材料,可例示出siox(1.5≤x≤2.5)、al2o3、aln、sin、sion、ta2o5等。作为形成该中间层的方法的例子,代表性的是cvd法(chemicalvapordeposition;化学气相沉积法)或以溅射法等为代表的pvd法(physicalvapordeposition;物理气相沉积法)等。或者,也能够采用将有机硅化合物的溶液涂敷在晶片上,通过热处理使其固化而形成sio2膜的方法。在通过这些方法沉积无机材料膜之后,需要在一定程度的高温下进行热处理,使从膜内部产生的气体(逸气(outgas))枯竭。这是因为,如果不进行该处理,则在贴合后的后工序中的加热处理反复执行的过程中,在贴合界面附近的沉积膜处产生的气体成分到达贴合界面,有可能从贴合界面引起剥离现象。但是,lt、ln等压电单晶体存在被称为居里温度的极化被破坏的上限温度,为了保持极化状态,不能施加这以上的温度。特别是lt处于600℃附近,即使在该温度以下进行处理也很难将逸气完全消除,因而关于剥离难以确保长期可靠性。另外,中间层所使用的无机材料sio2的热膨胀系数与lt、ln等压电晶体的热膨胀系数具有较大的差这一点是不能施加高温的另一个原因。lt或ln的热膨胀系数为16ppm左右,sio2的热膨胀系数为0.5ppm左右,由于该差,若经过高温处理,则会产生裂纹,导致无法进行以后的处理。据发明人等所知,在lt单晶基板分别沉积2μm左右的sio2、al2o3、aln、si3n4、sion、ta2o5作为中间层,在施加热处理时,不显著依赖于中间层的材质或沉积方法,在500~600℃左右产生裂纹。作为例子,图3示出了关于通过3种不同的方法制备出模拟中间层的无机材料层的样品,对逸气进行分析而得到的结果。第一个是通过在lt单晶基板利用cvd法沉积5μm的sio2而形成,并且从室温起实施加热处理直至1000℃时的tds(thermaldesorptionspectrometry,热释放谱)分析结果。由该结果可知,逸气的峰值位于500℃附近,之后,持续产生气体直至达到1000℃。第二个是通过旋涂甲基三甲氧基硅烷(溶剂:丙二醇单乙醚)沉积5μm的sio2而形成,并且实施同样的加热处理时的tds分析结果。在此也是在500℃附近存在逸气的峰值,并且在600℃以上也继续脱气,在1000℃也继续产生气体。第三个是通过pvd法沉积5μm的sio2而形成,并且实施了同样的加热处理时的tds分析结果。这也是在500℃附近存在逸气的峰值,在600℃以上也持续脱气直至达到1000℃。由此可知,在以这些方法沉积的中间层中,脱气需要1000℃或其以上的高温处理。现有技术文献非专利文献非专利文献1:电波新闻高科技2012年11月8日“用于智能手机的rf前端的saw-duplexer的温度补偿技术”非专利文献2:2010ieeeinternationalultrasonicsymposium(ius2010),2010vol.v1.p.637-640“astudyontemperature-compensatedhybridsubstratesforsurfaceacousticwavefilters”技术实现要素:发明所要解决的问题本发明鉴于上述情况而完成,其目的在于,提供一种即使在贴合后的工序中反复进行加热冷却也难以产生剥离的、以无机材料作为中间层将压电单晶层与支承基板贴合在一起的复合基板。用于解决问题的手段(1)本发明的复合基板的特征在于,具有压电单晶基板、支承基板以及设置在所述压电单晶基板与所述支承基板之间的中间层,所述中间层为由无机材料构成的膜,其至少一部分为热合成二氧化硅。本发明的发明人进行了潜心研究,结果发现,热氧化二氧化硅或合成二氧化硅烧结体等热合成二氧化硅具有能够吸收一定程度的气体的性质。通过如上述结构那样将中间层的至少一部分设为热合成二氧化硅,从而即使中间层的其他部分为脱气不充分的无机材料,也由于热合成二氧化硅对在后工序的加热冷却过程中有可能产生的逸气进行吸收,因此能够难以发生剥离。(2)在本发明中,所述中间层可以沿着复合基板的接合面分为至少2层,在这种情况下,与所述支承基板相接的第一中间层设为含有热合成二氧化硅的层为宜。由于在支承基板侧,居里温度等加热温度的制约较少,因此中间层中的与支承基板相接的层能够通过沉积热合成二氧化硅来形成。另一方面,压电单晶基板侧的中间层采用能够通过在居里温度以下的低温下进行沉积而形成的无机材料。在后工序的加热冷却反复执行的过程中,由支承基板侧的热合成二氧化硅吸收有可能从压电基板侧的中间层放出的逸气,因而难以发生剥离。(3)在本发明中,支承基板的材质可以为硅基板,在这种情况下,所述热合成二氧化硅通过所述硅基板的热氧化而合成为宜。这样,能够在硅基板的表面形成热氧化层,并将其用作中间层的一部分。另外,能够容易地形成热合成二氧化硅。(4)或者,热合成二氧化硅也可以是合成二氧化硅的烧结体。这样,作为支承基板的材质,不仅能够使用硅,还能够使用蓝宝石、氮化硅、氮化铝、碳化硅、石英玻璃等耐热性基板。能够将通过任意的方法沉积于支承基板的二氧化硅与支承基板一起进行加热而在支承基板表面形成烧结体二氧化硅,将其用作中间层的一部分。作为二氧化硅的沉积方法,采用化学气相沉积法(cvd)、物理气相沉积法(pvd)、有机硅化合物溶液的涂敷/烧成等为宜。例如,在通过pvd法制成的二氧化硅的情况下,由于刚成膜后的膜质不致密,因此通过1000℃左右的加热处理来进行烧结为宜。(5)在本发明中,设置于比与支承基板相接的第一中间层更靠压电单晶基板侧的第二中间层的材质含有siox、al2o3、aln、sin、sion、ta2o5中的至少一种为宜。上述物质能够通过cvd法、pvd法等在500℃以下的比较低的温度下进行沉积、处理,从这一点出发为优选。(6)在本发明中,所述第二中间层具有材质不同的至少2个层为宜。另外,该至少2个层设为热膨胀系数不同的材质的层为宜。这样,能够通过不同材质的多个层来缓和热应力,从而能够使裂纹、剥离难以产生。(7)在本发明中,将所述第一中间层的厚度设为20nm以上为宜。这样,能够使第一中间层具有充分的逸气吸收能力。(8)在本发明中,将所述第二中间层的厚度设为25μm以下为宜。这样,能够防止由于压电单晶基板与第二中间层之间的热膨胀系数差所引起的应力而导致在压电单晶基板产生裂纹的情况。另外,在第二中间层的厚度的下限并无特别限制,在与压电单晶基板之间的界面平坦的情况下,只要为50nm以上的厚度即可。另外,在界面具有凹凸构造的情况下,只要压电单晶基板的凸部容纳在第二中间层内即可。(9)在本发明中,在支承基板的背面(即,和夹着中间层与压电单晶接合的面相反一侧的面)还具备热合成二氧化硅层为宜。这样,在支承基板的两面形成热合成二氧化硅层,从而施加于支承基板的应力平衡,基板的翘曲得到减轻。(10)在本发明中,第一中间层和第二中间层夹着由非晶硅构成的第三中间层而接合为宜。这样,能够提高接合强度,从而能够使裂纹或剥离难以产生。另外,第三中间层的厚度设为50nm以下为宜。这样,能够使在第二中间层侧产生的逸气良好地透过到第一中间层侧。(11)在本发明中,将中间层的厚度设为8μm以下为宜。这样,能够提高复合基板的耐热性。(12)另外,将中间层的厚度设为7μm以下更好。这样,能够进一步提高复合基板的耐热性。(13)在本发明中,将压电单晶的厚度设为20μm以下为宜。这样,能够提高复合基板的耐热性。(14)在本发明中,使所述压电单晶与所述中间层之间的界面成为凹凸构造为宜。这样,能够抑制由复合基板制成的谐振器的寄生现象。(15)本发明的表面弹性波器件构成为包括上述任一复合基板为宜。这样,能够实现小型且性能高的表面弹性波器件。(16)在本发明中,将压电单晶的厚度设为表面弹性波的波长的1.0倍以上且3.5倍以下为宜。这样,能够提高使用复合基板制作出的谐振器的q值。(17)本发明的复合基板的制造方法具备:在支承基板的表面形成含有热合成二氧化硅的第一中间层的工序;在压电单晶基板的表面形成含有无机材料的第二中间层的工序;使所述第二中间层的表面平坦化的工序;以及将所述第一中间层的表面与所述第二中间层的平坦化后的表面进行贴合的工序。通过上述制造方法,作为中间层的一部分的第一中间层含有热合成二氧化硅,由此,第一中间层能够吸收在后工序的加热冷却中有可能从第二中间层产生的逸气。由此,能够使贴合后的基板难以产生剥离。(18)在本发明中,还具备使第一中间层的表面平坦化的工序为宜。这样,即使在形成热合成二氧化硅而得到的第一中间层的表面为非平坦的情况下,也能够实现牢固的贴合。另外,使该第一中间层的表面平坦化的工序在进行贴合的工序之前实施。(19)在本发明中,还具备在压电单晶基板的表面形成凹凸的工序为宜。这样,能够使由通过该制造方法得到的复合基板制成的器件的特性良好。具体而言,例如能够抑制由通过该制造方法得到的复合基板制成的谐振器的寄生现象。(20)在本发明中,所述第一中间层也可以采用对通过化学气相沉积法(cvd)沉积的二氧化硅层在800℃以上进行烧结而成的热合成二氧化硅。(21)所述第一中间层也可以采用对通过物理气相沉积法(pvd)沉积的二氧化硅层在800℃以上进行烧结而成的热合成二氧化硅。(22)或者,所述第一中间层也可以采用涂敷有机硅化合物的溶液并在800℃以上进行烧结而成的热合成二氧化硅层。在上述(20)~(22)的方法中,通过对二氧化硅层在800℃以上进行烧结,从而促进从二氧化硅层的脱气,能够形成经烧结后的致密的热合成二氧化硅(烧结二氧化硅)膜。并且,该热合成二氧化硅具有良好的气体吸收能力。另外,烧结时的温度优选设为1000℃以上。(23)在本发明中,所述支承基板的材质选自硅、蓝宝石、碳化硅、氮化硅、氮化铝、石英玻璃为宜。通过使用这些耐热性优异的材质的支承基板,能够在上述(20)~(22)的方法中以800℃以上的高温对二氧化硅层进行烧结。(24)另外,在支承基板的材质为硅的情况下,也可以对上述支承基板进行热氧化而形成第一中间层。这样,能够在硅基板的表面形成热氧化层,并将其用作中间层的一部分。另外,能够容易地形成热合成二氧化硅。(25)在本发明中,还包括以比所述压电晶体的居里温度低的温度对所述第二中间层进行加热的工序为宜。这样只要以低温对第二中间层加热,就能够减少残留气体,从而能够抑制在后工序的加热冷却反复执行的过程中产生的逸气,能够减少剥离的产生。(26)加热第二中间层时的温度优选设定为600℃以下。这样,能够抑制由于热膨胀的差异而导致第二中间层发生破裂的情况。(27)在本发明中,除了在支承基板的表面之外,还在支承基板的背面(即,和夹着中间层与压电单晶体接合的面相反一侧的面)也形成与第一中间层相同材质的热合成二氧化硅层为宜。这样,在支承基板的两面形成热合成二氧化硅层,从而施加于支承基板的应力平衡,因此能够减轻基板的翘曲。另外,也可以在贴合支承基板与压电单晶基板之后,使用氢氟酸等适当地去除支承基板的背面的热合成二氧化硅层。(28)在本发明中,在第一中间层的表面、第二中间层的表面中的至少任意一方还沉积非晶硅之后进行贴合为宜。这样,能够提高接合强度,从而能够使裂纹或剥离难以产生。(29)此时,非晶硅层的厚度的合计设为50nm以下为宜。这样,能够使在第二中间层侧产生的逸气良好地透过到第一中间层侧。(30)在本发明中,在第一中间层和第二中间层中的至少一方的表面实施活化处理之后,将第一中间层的表面与第二中间层的表面进行贴合为宜。(31)表面活化处理采用臭氧水处理、uv臭氧处理、离子束处理、等离子体处理中的任意一种为宜。通过活化处理,能够实现牢固的贴合。(32)在本发明中,通过化学机械研磨使第一中间层的表面和/或第二中间层的表面平坦化为宜。(33)在本发明中,第二中间层的材质含有siox、al2o3、aln、sin、sion、ta2o5中的任意一种为宜。上述物质能够通过cvd法、pvd法等在500℃以下的比较低的温度下进行沉积、处理,从这一点出发为优选。(34)在本发明中,可以通过化学气相沉积法(cvd)形成第二中间层。(35)或者,也可以通过物理气相沉积法(pvd)形成第二中间层。(36)或者,也可以通过涂敷有机硅化合物的溶液并使其固化而形成第二中间层。(37)在本发明中,在进行贴合的工序之前,具有在压电单晶基板进行离子注入处理的工序,在进行贴合的工序之后,在注入了离子的区域的界面处进行剥离为宜。(38)在进行离子注入处理的工序中,注入6.0×1016atoms/cm2~2.75×1017atoms/cm2的氢离子为宜。(39)或者,在进行离子注入处理的工序中,也可以注入3.0×1016atoms/cm2~1.37×1017atoms/cm2的氢分子离子。(40)另外,在进行剥离的工序中,沿着注入了离子的区域的界面机械性地进行剥离为宜。(41)或者,在剥离的工序中,也可以通过闪光灯退火进行剥离。(42)在本发明中,也可以在进行贴合的工序之后,具有对压电单晶基板进行磨削和/或研磨而使其薄化的工序。附图说明图1为对各种材料的热膨胀系数进行对比表示的曲线图。图2表示由现有的复合基板制成的谐振器中的反射系数的频谱。图3表示从中间层排出的逸气排出量的温度依赖性。图4表示贴合前的支承基板的处理方法。图5表示贴合前的压电单晶基板的处理方法。图6表示贴合以及之后的处理方法。图7示意性地表示在第一中间层与第二中间层之间设置有非晶硅层的复合基板的构造。图8表示在实施例1中制成的复合基板的截面显微镜照片。图9表示在实施例8中制成的谐振器中的反射系数的频谱。具体实施方式经由对支承基板100和压电单晶基板200分别进行贴合前的处理,然后贴合两基板的工序,制造出本实施方式的复合基板1。以下,参照图4至图6对其制造方法进行说明。[支承基板的处理]首先,准备支承基板100(图4的(a))。支承基板100选自硅、蓝宝石、碳化硅、氮化硅、氮化铝、石英玻璃。接着,在支承基板100的表面形成含有热合成二氧化硅的第一中间层310(图4的(b))。此时,在支承基板100的背面也形成与第一中间层310相同材质的热合成二氧化硅层为宜。另外,该背面的二氧化硅层可以在贴合支承基板100和压电单晶基板200之后,使用氢氟酸等适当地去除。在支承基板100的材质为硅的情况下,能够对硅基板进行热氧化而形成成为第一中间层310的热氧化二氧化硅的膜。热氧化二氧化硅由于在高温下生长,因而致密且杂质少,并且具有能够吸收一定程度的量的气体的性质。另外,无论支承基板100无论是硅还是硅以外的材料,都能够通过下述方法形成第一中间层310。即,第一中间层310可以通过在800℃以上对利用化学气相沉积法(cvd)沉积的二氧化硅层进行烧结而形成。此外,第一中间层310也可以通过在800℃以上对利用物理气相沉积(pvd)沉积的二氧化硅层进行烧结而形成。或者,第一中间层310也可以通过涂敷有机硅化合物的溶液,并在800℃以上进行烧结而形成。在将第一中间层310设为二氧化硅烧结体的情况下,优选使用耐热性基板,使得能够将沉积于支承基板100的合成二氧化硅与支承基板100一起进行烧结。接着,根据需要使第一中间层310的表面平坦化(图4的(c))。该平坦化通过化学机械研磨进行为宜。另外,在使用表面精加工成镜面的硅基板作为支承基板100,并通过热氧化形成第一中间层310的情况下,第一中间层310的表面也与基底同样地成为镜面,因而不需要该平坦化的工序。而且,虽然省略了图示,但为了提高贴合时的接合强度,也可以根据需要进行下述处理。例如,也可以在第一中间层310的表面沉积非晶硅。通过层叠非晶硅,接合界面成为si/sio2或si/si,接合强度比sio2/sio2接合会高出一些(详情参照tongq.y.andgoseleu.,semiconductorwaferbondingchapter4.7.1:scienceandtechnology,1999.)。沉积的非晶硅的厚度优选设为50nm以下,使得不阻碍气体的透过。另外,也可以在第一中间层310的表面实施活化处理。表面活化处理例如采用臭氧水处理、uv臭氧处理、离子束处理、等离子体处理中的任意一种为宜。通过以上,完成针对支承基板100的贴合前的处理。[压电单晶基板的处理]首先,准备压电单晶基板200(图5的(a))。压电单晶基板200是钽酸锂(lt)或铌酸锂(ln)等压电体的单晶体。接着,根据需要,在压电单晶基板200的表面形成凹凸(图5的(b))。该凹凸具有抑制由复合基板1制成的谐振器的寄生现象的效果。在将复合基板1用于寄生不成问题的用途的情况下,可以省略该工序。接着,通过在压电单晶基板200的表面进行沉积而形成包含无机材料的第二中间层320(图5的(c))。第二中间层320的材质包含siox(例如sio2)、al2o3、aln、sin、sion、ta2o5中的任一种。第二中间层320能够通过下述方法形成。即,第二中间层320可以通过化学气相沉积法(cvd)进行沉积。另外,第二中间层也可以通过物理气相沉积法(pvd)进行沉积。或者,第二中间层320也可以通过涂敷有机硅化合物的溶液,并使其固化而进行沉积。为了减少残留气体,在比压电晶体的居里温度低的温度下加热通过上述任一方法形成的第二中间层320为宜。为了防止由于压电单晶基板200与第二中间层320之间的热膨胀率的差异而引起的第二中间层320的破裂,加热温度优选设为600℃以下。第二中间层320也可以构成为具有材质不同的至少2个层。接着,使所形成的第二中间层320的表面平坦化(图5的(d))。该平坦化通过化学机械研磨进行为宜。而且,虽然省略了图示,但为了提高贴合时的接合强度,也可以根据需要进行下述处理。例如,也可以在第二中间层320的表面沉积非晶硅。沉积的非晶硅的厚度优选设为50nm以下,使得不阻碍气体的透过。另外,在第一中间层310也沉积非晶硅的情况下,使得厚度的合计成为50nm以下为宜。另外,也可以在第二中间层320的表面实施活化处理。表面活化处理例如采用臭氧水处理、uv臭氧处理、离子束处理、等离子体处理中的任意一种为宜。通过以上,完成针对压电单晶基板200的贴合前的处理。[贴合及其后的处理]针对如上所述处理过的支承基板100和压电单晶基本200,将第一中间层310的表面与第二中间层320的表面进行贴合(图6的(a))。此时,加热至低温(例如120℃)来提高接合强度为宜。接着,对压电单晶基板200进行磨削和研磨,使其薄化。例如,薄化到压电单晶基板200的厚度成为20μm左右(图6的(b))。然后还可以根据需要进行追加的热处理,增强接合力。这样贴合而接合在一起的第一中间层310和第二中间层320构成中间层300。另外,如图7所示,在第一中间层310与第二中间层320之间设有非晶硅层(第三中间层)330的复合基板1的结构中,第一中间层310、第二中间层320及第三中间层330构成中间层300。通过以上说明的制造方法,能够制造使压电单晶基板200和支承基板100夹着中间层300而接合的复合基板1。[表面弹性波特性的评价]在制成的复合基板1的压电单晶基板200表面溅射蒸镀0.4μm厚的铝(al)薄膜,通过光刻形成电极,由此制作出由波长5μm的2级并联谐振器和4级串联谐振器构成的4级梯形滤波器以及谐振器。光刻的曝光使用g线的步进器,al的蚀刻使用cl2、bcl3、n2及cf4的混合气体。使用网络分析仪,对所制成的4级梯形滤波器的反射系数(s11)进行了测量。将观测到的寄生的波峰与波谷之差作为寄生强度来进行了评价。进而,通过以下的数学式(1)来求取所制成的谐振器的q值与谐振频率之间的关系。[数学式1]这里,ω表示角频率,τ表示群延迟时间。q值是表示谐振波形的尖锐度的值,q越高,可以认为是损耗越少且特性优异的滤波器。由于q值具有频率依赖性,因此对q值的最大值(qmax)进行了评价。实施例[实施例1]准备了具有ra(算术平均粗糙度)为230nm左右的粗糙度(p-v为1.7μm左右)的直径为6英寸的lt基板作为压电单晶基板。在该lt基板上,以硅烷和氧气作为原料气体,通过等离子体cvd法进行沉积而形成10μm左右的sio2膜。对该sio2膜实施400℃左右的热处理,进行研磨而使其镜面化,将所述sio2膜精加工成膜厚为约2μm。另外,准备了生长有500nm的热氧化膜的直径为6英寸的si基板作为支承基板。然后,对所述附有sio2膜的lt基板和生长有热氧化膜的si基板这两者实施了等离子体表面活化。然后,将两基板贴合,施加120℃的热处理,然后通过磨削和研磨,将lt薄化成20μm左右。在图8中示出这样完成的复合基板的截面显微镜照片。将该复合基板的晶片切割成2mm见方,通过使200℃的加热板和金属制的冷却台往复(在加热板和冷却台中分别保持30秒),来调查了耐热性试验。尝试了100次往复,但未观察到剥离等。另外,在镜面的lt基板的表面以相同条件形成氧化膜并进行了同样的实验,关于耐热性,取得了完全相同的结果。这示出了在寄生不成问题的应用的情况下,通过在精加工成镜面的lt基板形成氧化膜并采用相同的方法,本发明能够直接原样应用。[比较例1]使用与实施例1同样地设有sio2膜的lt基板和未进行热氧化的si基板,进行了与实施例1同样的实验。与实施例1同样的耐热耐性试验的结果,在第5次往复时在周边观察到剥离。通过实施例1与比较例1的对比可知,通过将利用等离子体cvd法设置了sio2膜的lt基板与生长有热氧化膜的si基板进行贴合,与不使热氧化膜生长而贴合si基板的情况相比,能够抑制剥离。[实施例2]准备了具有ra为230nm左右的粗糙度(p-v为1.7μm左右)的直径为6英寸的lt基板。在该lt基板上旋涂有机硅化合物溶液并在350℃下加热,重复多次该工序,由此得到5μm左右的sio2层。这里使用的有机硅化合物溶液是全氢化聚硅氮烷(溶剂为二丁基醚)和甲基三甲氧基硅烷(溶剂为丙二醇单乙醚)这两种。将该sio2膜在400℃左右的热处理之后进行研磨而使其镜面化。另外,准备了生长有500nm的热氧化膜的直径为6英寸的si基板。对两基板实施等离子体表面活化。然后,将两基板贴合,施加120℃的热处理,然后通过磨削和研磨,将lt薄化成20μm左右,得到了复合基板。将该复合基板的晶片切割成2mm见方,通过使200℃的加热板和金属制的冷却台架往复(在加热板和冷却台架中分别保持30秒),调查了耐热性试验。尝试了100次往复,但未观察到剥离等。[比较例2]使用与实施例2同样地设有sio2膜的lt基板和未进行热氧化的si基板,进行与实施例2同样的实验。与实施例2同样的耐热耐性试验的结果,在第7次往复时在周边观察到剥离。通过实施例2与比较例2的对比可知,通过将对有机硅化合物溶液进行旋涂并加热而设置了sio2膜的lt基板与生长有热氧化膜的si基板进行贴合,与不使热氧化膜生长而贴合si基板的情况相比,能够抑制剥离。[实施例3]准备了具有ra为230nm左右的粗糙度(p-v为1.7μm左右)的直径为6英寸的lt基板。在该lt基板上,通过pvd法(此处为磁控溅射法)形成了10μm左右的sio2膜。将该sio2膜在400℃左右的热处理之后进行研磨而使其镜面化。另外,准备了生长有500nm的热氧化膜的直径为6英寸的si基板。对两基板实施等离子体表面活化。然后,将两基板贴合,施加120℃的热处理,然后通过磨削和研磨,将lt薄化成20μm左右,得到了复合基板。将该复合基板的晶片切割成2mm见方,通过使200℃的加热板和金属制的冷却台架往复(在加热板和冷却台架中分别保持30秒),调查了耐热性试验。尝试了100次往复,但未观察到剥离等。[比较例3]使用与实施例3同样地设有sio2膜的lt基板和未进行热氧化的si基板,进行了与实施例3同样的实验。与实施例3同样的耐热耐性试验的结果,在第2次往复时在周边观察到剥离。通过实施例3与比较例3的对比可知,通过将利用pvd法设置了sio2膜的lt基板与生长有热氧化膜的si基板进行贴合,与不使热氧化膜生长而贴合si基板的情况相比,能够抑制剥离。[实施例4]准备了多个具有ra为230nm左右的粗糙度(p-v为1.7μm左右)的直径为6英寸的lt基板。在准备好的lt基板上,通过等离子体cvd法形成10μm左右的sio2膜。对sio2膜实施400℃左右的热处理,进行研磨而使其镜面化后,如表1所示,以各种厚度对非晶硅(a-si)进行了成膜。非晶硅通过pvd法(磁控溅射法)和cvd法这两种方法,改变厚度而成膜。对该lt基板和生长有500nm的热氧化膜的直径为6英寸的si基板这两者实施等离子体表面活化。然后,将两基板贴合,施加120℃的热处理,然后通过磨削和研磨,将lt薄化成20μm左右,得到了复合基板。将得到的复合基板的晶片切割成2mm见方,通过使200℃的加热板和金属制的冷却台架往复(在加热板和冷却台架中分别保持30秒),调查了耐热性试验。将其结果示于表1。可知在pvd法、cvd中,若非晶硅的厚度超过50nm,则耐性都会急剧劣化。可以认为这是因为,由于非晶硅的厚度变厚,从而由lt侧的sio2产生的气体不能透过非晶硅的膜,被si的热氧化膜吸收受到阻碍。[表1]a-si厚度(nm)3510203550658080100pvd法>100次>100次>100次>100次>100次>100次75次52次12次3次cvd法>100次>100次>100次>100次>100次>100次19次11次5次2次[实施例5]不在lt基板侧而在生长有热氧化膜si基板侧进行非晶硅的成膜,并进行了与实施例4同样的实验。结果与实施例4几乎相同。由此可知,非晶硅可以设置在lt基板侧和si基板侧中的任意一侧。[实施例6]在lt基板、氧化si基板侧双方进行非晶硅的成膜,并进行与实施例4同样的实验。非晶硅的厚度为沉积于两者的非晶硅膜的总和。结果与实施例4几乎相同。由此可知,非晶硅可以设置在lt基板侧和si基板侧双方。[实施例7]将表面活化方法的方法变更为臭氧水处理、uv臭氧处理、离子束处理,来进行了上述实验,但贴合的结果并没有出现差异。可以认为本发明并不强烈依赖于活化的方法。另外,在仅对一个基板实施表面活化时,也没有发现较大差异。[实施例8]在通过实施例1的方法制成的复合基板上制作4级梯形滤波器,并测量反射系数(s11)的频谱,评价了寄生的特性。结果,如图9所示,确认了寄生的强度为1db以下。判明了通过该方式制作出的谐振器能够有效地减少寄生。[实施例9]改变生长于si基板的热氧化膜的厚度,来进行了与实施例1同样的实验。结果,确认了20nm以上的热氧化膜具有效果。相反地,在小于20nm的热氧化膜的情况下,逸气吸收能力不充分,在加热冷却循环试验中存在发生剥离的情况。[实施例10]改变沉积于lt基板的sio2膜的厚度,来进行了与实施例1同样的实验。将其结果示于表2。表2所示的沉积sio2厚度为表面平坦化后的厚度。从该结果判明,当sio2膜的厚度(仅沉积膜,热氧化膜除外)超过25μm时,会在lt层产生裂纹。这可以认为是由于通过急速加热和冷却而产生的lt与sio2的膨胀系数之差所引起的应力而发生的。在sio2为25μm以下的情况下,sio2能够在一定程度上追随膨胀系数的差进行变形,但在该厚度以上时,由于应力缓和而产生裂纹。[表2]沉积sio2厚度(um)1251015202530裂纹产生状况无裂纹无裂纹无裂纹无裂纹无裂纹无裂纹在周边散见整体产生[实施例11]准备了一面为镜面的直径为6英寸的lt基板。在该lt基板的镜面侧上通过溅射法沉积了1μm的al2o3膜。然后,在该带有al2o3膜的lt基板的al2o3膜上,以硅烷和氧气作为原料气体,通过等离子体cvd法形成10μm左右的sio2膜。对该al2o3与sio2的层叠膜实施400℃左右的热处理,进行研磨而使其镜面化,将所述sio2膜精加工成膜厚为约2μm。另外,准备了生长有500nm的热氧化膜的直径为6英寸的si基板。然后,对两基板实施等离子体表面活化。然后,将两基板贴合,施加120℃的热处理,然后通过磨削和研磨,将lt薄化成6μm左右,得到了复合基板。将该复合基板的晶片切割成2mm见方,通过使200℃的加热板和金属制的冷却台架往复(在加热板和冷却台架中分别保持30秒),调查了耐热性试验。尝试了200次往复,但未观察到剥离等。根据本实施例可知,也可以在贴合前将设置于lt基板侧的中间层(即第二中间层)多层化。[实施例12]准备了具有ra(算数平均粗糙度)为230nm左右的粗糙度(p-v为1.7μm左右)的直径为6英寸的lt基板。在该lt基板上,以硅烷和氧气作为原料气体,通过等离子体cvd法进行沉积而形成10μm左右的sio2膜。对该sio2膜实施400℃左右的热处理,进行研磨而使其镜面化,将所述sio2膜精加工成膜厚为约2μm。准备直径6英寸的蓝宝石基板,并在其上通过等离子体cvd法形成约5μm的sio2膜。然后,通过800℃的热处理对该蓝宝石基板上的sio2膜进行烧结,进行研磨而使其镜面化,将sio2膜精加工成膜厚为1μm。对在lt基板上成膜的sio2膜和在蓝宝石基板上成膜的烧结sio2膜双方实施等离子体活性化处理,贴合两基板,施加120℃的热处理,然后对lt进行磨削和研磨,将其薄化成20μm,得到了复合基板。将该复合基板的晶片切割成2mm见方,通过使200℃的加热板和金属制的冷却台架往复(在加热板和冷却台架中分别保持30秒),调查了耐热性试验。尝试了100次往复,但未观察到剥离等。从本实施例可知,可以使用蓝宝石基板作为支承基板。另外,可知在贴合前设置于支承基板侧的中间层(即第一中间层)能够使用对通过cvd而成膜的sio2进行加热烧结而得到的热合成二氧化硅。[实施例13]准备了具有ra(算数平均粗糙度)为230nm左右的粗糙度(p-v为1.7μm左右)的直径为6英寸的lt基板。在该lt基板上,以硅烷和氧气作为原料气体,通过等离子体cvd法进行沉积而形成了10μm左右的sio2膜。对该sio2膜实施400℃左右的热处理,进行研磨而使其镜面化,将所述sio2膜精加工成膜厚为约2μm。准备直径6英寸的蓝宝石基板,在其上通过pvd(磁控溅射)形成了10μm左右的sio2膜。然后,通过900℃的热处理对该蓝宝石基板上的sio2膜进行烧结,并进行研磨而使其镜面化,将sio2膜精加工成膜厚为1μm。对在lt基板上成膜的sio2膜和在蓝宝石基板上成膜的烧结sio2膜这两者实施等离子体活性化处理,贴合两基板,施加120℃的热处理,然后对lt进行磨削和研磨,将其薄化成20μm,得到了复合基板。将该复合基板的晶片切割成2mm见方,通过使200℃的加热板和金属制的冷却台架往复(在加热板和冷却台架中分别保持30秒),调查了耐热性试验。尝试了100次往复,但未观察到剥离等。从本实施例可知,能够使用蓝宝石基板作为支承基板。另外,可知在贴合前设置于支承基板侧的中间层(即第一中间层)能够使用对通过pvd而成膜的sio2进行加热烧结而得到的热合成二氧化硅。[实施例14]准备了具有ra(算数平均粗糙度)为230nm左右的粗糙度(p-v为1.7μm左右)的直径为6英寸的lt基板。在该lt基板上,以硅烷和氧气作为原料气体,通过等离子体cvd法进行沉积而形成10μm左右的sio2膜。对该sio2膜实施400℃左右的热处理,进行研磨而使其镜面化,将所述sio2膜精加工成膜厚为约2μm。准备直径为6英寸的蓝宝石基板,反复进行数次在其上旋涂有机硅化合物溶液(全氢化聚硅氮烷的二丁基醚溶液)的工序和在350℃下进行加热固化的工序,形成了约3μm的sio2膜。然后,通过900℃的热处理对该蓝宝石基板上的sio2膜进行烧结,并进行研磨而使其镜面化,将sio2膜精加工成膜厚为0.5μm。对在lt基板上成膜的sio2膜和在蓝宝石基板上成膜的烧结sio2膜双方实施等离子体活性化处理,贴合两基板,施加120℃的热处理,然后对lt进行磨削和研磨,将其薄化成20μm,得到了复合基板。将该复合基板的晶片切割成2mm见方,通过使200℃的加热板和金属制的冷却台架往复(在加热板和冷却台架中分别保持30秒),调查了耐热性试验。尝试了100次往复,但未观察到剥离等。从本实施例可知,能够使用蓝宝石基板作为支承基板。另外,可知作为在贴合前设置于支承基板侧的中间层(即第一中间层)能够使用涂敷有机硅并进行加热烧结而得到的热合成二氧化硅。[实施例15]准备具有ra(算数平均粗糙度)为230nm左右的粗糙度(p-v为1.7μm左右)的直径为6英寸的lt基板。在该lt基板上,以硅烷和氧气作为原料气体,通过等离子体cvd法进行沉积而形成了10μm左右的sio2膜。对该sio2膜实施400℃左右的热处理,进行研磨而使其镜面化,将所述sio2膜精加工成膜厚为约2μm。准备直径为6英寸的石英玻璃基板,反复进行数次在其上旋涂有机硅化合物溶液(甲基三甲氧基硅烷的丙二醇单乙醚溶液)的工序和在350℃下进行加热固化的工序,形成了约3μm的sio2膜。然后,通过1000℃的热处理对该石英玻璃基板上的sio2膜进行烧结,并进行研磨而使其镜面化,将sio2膜精加工成膜厚为0.5μm。对在lt基板上成膜的sio2膜和在石英玻璃基板上成膜的烧结sio2膜双方实施等离子体活性化处理,贴合两基板,施加120℃的热处理,然后对lt进行磨削和研磨,将其薄化成20μm,得到了复合基板。将该复合基板的晶片切割成2mm见方,通过使200℃的加热板和金属制的冷却台架往复(在加热板和冷却台架中分别保持30秒),调查了耐热性试验。尝试了100次往复,但未观察到剥离等。从本实施例可知,能够使用石英玻璃基板作为支承基板。另外,可知作为在贴合前设置于支承基板侧的中间层(即第一中间层)能够使用涂敷有机硅并进行加热烧结而得到的热合成二氧化硅。[实施例16]准备了具有ra(算术平均粗糙度)和rsm(轮廓(粗糙度)曲线中的要素的平均长度)为同等程度的凹凸构造的多个lt基板(ra=300nm±10%,rsm=3μm±10%,rz=2.0μm±10%)。在此,lt基板的凹凸构造是通过使用游离磨粒进行研磨而形成的。这里,ra、rsm的定义是按照jisb0601:2001和iso4287:1997,根据使用afm(atomicforcemicroscope;原子力显微镜)测量出的轮廓曲线计算出的。接着,在lt基板的具有凹凸构造的面,使用等离子体cvd法在35℃下沉积10μm左右的sio2后,对沉积有sio2的面进行研磨并进行镜面化。此时,根据lt基板来改变研磨量,使得sio2的厚度成为1.5μm~9.5μm。通过在氧气氛中在850℃下对成为支承基板的si基板实施热处理,从而在si基板表面形成了0.5μm的热氧化二氧化硅。然后,对sio2镜面以及形成于si基板表面的热氧化二氧化硅双方实施等离子体表面活化,并进行贴合,然后对lt基板进行研磨而制成复合基板。此时,根据基板来改变研磨量,使得lt基板的厚度成为5μm~25μm。将各复合基板晶片放入烘箱中逐渐加热,测量了lt基板开始剥离的温度。另外,在各复合基板的表面形成电极,进行了表面弹性波特性的评价。将这些评价结果示于表3和表4。[表3][表4]根据该结果可知,lt基板的厚度越小,并且中间层的厚度越小,则剥离开始温度越高,耐热性越优异。在考虑到后工序中的200℃的加热的情况下,如果将lt基板的厚度形成为15μm以下,则能够与2~10μm的中间层的厚度无关地使用,故优选。另外,在这种情况下,在将lt基板的厚度形成为17.5μm时,优选将中间层的合计厚度设为9μm以下。另外,进一步地,在lt基板的厚度厚至20μm时,优选将中间层的合计厚度设为8μm以下。另外,在考虑到在后工序中更高温的250℃的加热的情况下,若将lt基板的厚度形成为15μm以下,则更优选将中间层的厚度设为7μm以下。在将lt基板的厚度厚至20μm时,更优选将中间层的厚度设为6μm以下。另一方面,可知中间层的厚度越小,q值越大。另外,若将lt基板的厚度设为小于1.5波长或超过3.0波长,则q值有降低的倾向。另外,无论lt基板的厚度或中间层的厚度如何,寄生强度均被抑制为低至1.0db以下。[实施例17]准备了具有ra(算术平均粗糙度)为20nm的粗糙度的直径为100mm、厚度为0.35mm的lt基板。在该lt基板上,通过pvd法形成200nm左右的sio2膜,研磨至50nm并进行镜面化,确认了表面粗糙度以rms表示为1.0nm以下。接着,在剂量为7.0×1016atoms/cm2、加速电压为100kev的条件下向形成有sio2膜的lt基板注入氢离子(h+)。另外,准备si基板作为支承基板,并生长500nm的热氧化膜。对lt基板和si基板实施等离子体活化处理,进行表面活化。然后,将两基板贴合,实施100℃24小时的热处理。接着,将楔形的刀刃紧贴于以这种方式贴合的基板的侧面的离子注入界面附近,机械性地进行了剥离。这样,能够得到在si基板上隔着sio2层而层叠有约600nm的lt薄膜的复合基板。在实施研磨并进行镜面化后进行了评价,在热耐久性试验中未观察到剥离。另外,在实施例17中,也能够在形成sio2膜之前进行氢离子向lt基板的注入。即使这样,也可获得与在形成sio2膜之后注入氢离子的情况同样的效果。另外,只要将氢离子的剂量设为6.0×1016atoms/cm2~2.75×1017atoms/cm2的范围,就能获得同样的效果。另外,通过以3.0×1016atoms/cm2~1.37×1017atoms/cm2的范围注入氢分子离子(h2+)来取代氢离子,也可获得同样的效果。[实施例18]准备了具有ra(算术平均粗糙度)为20nm的粗糙度的直径为100mm、厚度为0.35mm的lt基板。在该lt基板上,通过pvd法形成200nm左右的sio2膜,研磨至50nm并进行镜面化,确认了表面粗糙度以rms表示为1.0nm以下。接着,在剂量为7.0×1016atoms/cm2、加速电压为100kev的条件下向形成有sio2膜的lt基板注入氢离子。另外,准备si基板作为支承基板,并生长了500nm的热氧化膜。对lt基板和si基板实施等离子体活化处理,进行表面活化。然后,将两基板贴合,实施100℃24小时的热处理。接着,通过使用闪光灯退火(fla)装置,从lt侧向以上述方式贴合的基板照射闪光,从而在离子注入界面处进行剥离。这样,能够得到在si基板上隔着sio2层而层叠有约600nm的lt薄膜的复合基板。在实施研磨并进行镜面化后进行了评价,在热耐久性试验中未观察到剥离。另外,在实施例18中,也能够在形成sio2膜之前进行氢离子向lt基板的注入。即使这样,也可获得与在形成sio2膜之后注入氢离子的情况同样的效果。另外,只要氢离子的剂量设为6.0×1016atoms/cm2~2.75×1017atoms/cm2的范围,就能获得同样的效果。另外,通过以3.0×1016atoms/cm2~1.37×1017atoms/cm2的范围注入氢分子离子(h2+)来取代氢离子,也可获得同样的效果。[实施例的变形]上述实施例和参考例全部使用lt基板作为压电单晶基板,但即便使用ln基板来代替lt基板,也会成为完全相同的倾向的结果。另外,即便代替sio2而将第二中间层设为sio2以外的siox、al2o3、aln、sin、sion、ta2o5等,也会成为同样的结果。另外,关于中间层的膜材质,在上述研究中全部使用了sio2,但即使像sio2±0.5那样并非是严格地为化学计量组成的材料,效果也完全不会发生改变。这可以认为是由于中间层主要通过填埋凹凸而起到上述效果的缘故。另外,即使在将支承基板变更为硅、碳化硅、氮化硅或氮化铝,在其表面通过cvd、pvd或涂敷有机硅而形成合成氧化硅膜,并且在800℃以上的温度下进行加热烧结,由此形成热合成二氧化硅的情况下,也能够良好地进行接合,切割成2mm见方并实施了温度循环试验,并未发现剥离。符号说明100支承基板200压电单晶基板300中间层310第一中间层320第二中间层330第三中间层。当前第1页12